Introduction: 2001 - a Space Odyssey Aries 1B - Scratch Build
This completely scratch built project is 99-44/100% plastic with a little bit of electrical wiring (and paint) to bring it to life! It is primarily PLA (3D filament) with polystrene sheets for the exterior door panels, a little acetate for the windows and acrylic (polycarbonate) for the interior seating cabin ceiling.
So what exactly is it you might ask ???
If you are a fan of the iconic Sci Fi movie 2001 - A Space Odyssey, by Arthur C. Clark and Stanley Kubrick (1968) you will recognize this as a model of the Aries 1B which transported the Dr. Heywood Floyd from the Earth space station to the moon to investigate the monolith. The cool part about all the ships in the movie is that they went to NASA and spent outrageous amounts of time picking rocket scientist brains for what space travel might actually look like in the year 2001. So essentially, the designs have a lot of technical merit behind them. The studio (MGM) had ordered all of the models destroyed after the film was made but a few years ago the only surviving model was discovered in a warehouse in England where the movie was filmed. The model that survived was this Aries 1B and was eventually put up for auction and it sold for $344,000 to the Academy of Motion Pictures Arts.
Since the movie has been released over 50 years ago, models of the ships HAD been sold to the public back then, but since have fallen out of production and extremely hard to find. If found, they are in the several hundreds of dollars to obtain if they are available for sale. Recently, the model wass made availble for a company to reverse engineer the model, document all of the details on how the model was built. Their photos are on the internet of which I referenced to create my own affordable model to adorn my shop.
This is a complete scratch build from those reference photos, scaled to fit on a 300 x 300 x 400 mm 3d print bed. I drew all parts for this assembly in SketchUp CAD, transferred to CURA to 3D print it, and assembled and finished it off.
This is how you can do the same...
Supplies
1 and 1/2 rolls of 3D Print Filament - I used PLA for ease in printing. This depends on how many failed prints you might encounter. I used 2 rolls but many parts were printed then redesigned for a better fit up.
LEDs - 3 - Red LEDs for the pilots' cabin, 4 for the passenger deck.
Resistors for the LEDs.
A Surplus Wall Wart transformer - From an old cordless phone base. Mine was 9 vdc so I stepped it down with the resistors to get down to 3 vdc to run the LEDs.
3M Spot Putty - Used to true up gaps in the model.
CA Glue - I used Gorilla Gel Brand so I have a little time to orient pieces before setting.
CA Catylist - for those parts I want an instant bond.
Rustoleum Auto Primer (gray) & Rustoleum Flat white spray cans.
Testors Enamel Model Paints for weathering and detail painting .
a 24 x 24" sheet 0.030" thick Polystyrene for the exterior panel doors.
24 awg wire - for the leds.
a two prong, breadboard connector pins male and female to get the power to the ship.
Step 1: Create the Model Digitally
One of the most fun aspects of 3D printing is that you can readily create something from your imagination to a physical item in a relatively few steps and effort. The best thing is that it then is manufactured for you, while you do something more important like taking your dog for a walk or eating pizza!
I use a very easy to learn CAD software called SketchUp which cost me about $50. There are other (FREE) softwares out there that are much more powerful such as Fusion 360 or Blender, but they take a significant amount of effort to learn to be able to draw this type of object (but I'm still trying to make the switch). Fusion 360 is quite popular and handles very organic shapes well like curves, spheres, and such for helmets etc. Take the time to learn this software and the sky is the limit. SketchUp works better for angular items such as architectural or mechanical parts and is limited in such things as threads, gear teeth etc.
SCALE - i chose to make the model just fit on my Creality CR-10 S4 printer which has a bed of 300 x 300 mm. This means the model is about 12" in diameter. I started off with a sphere and kept editing it into key major components starting with three ship hulls (top dome, middle window hull, and lower hull). I then added the details such as creating the engine, its mounting ring, and greeblies for it. Then I went on to the landing gear which ultimately was the hardest to model.
The most fun was getting to a point where I could model the greeblies and the passenger deck, pilot cabin, and all the details for the exterior (antennas, door latches, etc.).
The best part about this is once you have the basic shape, then all I did was keep referencing the photos of the real movie model and creating the replica as best as I could see it and calling it "good enough." This is because the real model was over 3 feet in diameter which means there were scores of greeblies on the official model, of which I didn't have the scale large enough to add everything they had on their model. In the end, most people will not know where I eliminated this level of detail.
You can get the complete file set here:
Step 2: Print & Process the 3D Parts
This is a perfect model from which to consume all of the extraneous left over filament rolls you might have laying around. Often there are rolls of filament with less than 200 grams left on the spool and this model has a lot of parts that are small and can consume this surplus material up.
Print the parts according to the settings that best work for you and your printer for the plastic you choose. I would only suggest to print using a 0.4mm nozzle and 0.1 layer height to get the finest detail possible as the parts can get small such as the thruster nozzles (just under the windows) and it will help with the strength for fragile parts like the landing gear pod covers.
Browse through the photos and you can see where I test fitted the parts and adjusted (removed flashing, or deburred the edges) for getting the best part fits possible. Where I had gaps in the design, I had a choice to redraw the part for a better fit (which I sometimes had to do) or it was close enough and just puttied the gaps. In a few locations, I added some scrap plastic I had laying around to act as a cleat for more insurance of a good glued seam - see the photos on hte lower hull plate where the engines mount.
Free Locating Parts - I chose sometimes to locate parts once I had a physical piece in my hands versus doing it all in CAD. This happened on the lower crew hatch / door, the thrusters, and on locating the small round antennas just below the pilot windows. It was far easier to trace the crew door on the lower hull where I wanted it and dremel through the side wall to cut in a hole to fit the door exactly. This is where scratch building experience pays off. It allows for flexibility in designing the final outcome once you see it in 3D versus the screen. Locating the antennas on a curved surface by looking at the photos was very hard to accurately judge their location, but once I had the upper dome in hand, I was able to see much clearer where they should go.
Glueing - Once tested fitting the parts and "good to go forward" in glueing them, I used CA glue exclusively on the model as it bonds super strong on PLA and the short cure time helps when trying to hold curved pieces in place. For those challenging assemblies I sprayed the CA activator on one side of the mated pieces and put the CA glue on the other side. Be careful here because once they touch, it will be nearly impossible to reposition those accelerated pieces.
Step 3: Painting & Assembly Further Thoughts
I paint parts as I go along the assembly process. This helps in being able to get uniform coating and identifying where a part just doesn't look right due to a defect in the part or how I glued it up. Maybe I have glue runs or something similar I want to fix. Then this gives me an opportunity to clean it up one last time before it becomes unreachable but easily seen if glued up on the ship.
I spent too much time painting the small parts different colors for the engines only to later realize the ship in the movie was basically all white with dirt and weathering on the ship's panels and soot on the engine bays. Oh well, nothing that another coat of spray paint couldn't fix. So that is why everything went back to white from the photos shown.
For heavier assemblies such as mounting the engines to the lower hull plate, I scribed some cross hatching on the plate as well as the engine tank itself to provide a rough surface for the glue to grip.
Step 4: Wire It for Lights!
I needed the pilot's cabin to be red as shown in the movie and the passenger bay to be lit up as well. So for the Pilot's cabin I used 3 LEDs connected in parallel. So I had to drop 6 volts from the wall wart transformer.
See the crude wiring diagram I provided in the photos.
Using V = IR to calculate the ohms I needed goes as follows ....
Pilot's cabin... to provide a total of 0.020 amps x 3 = 0.060 amps flow through the resistor. 6 volts needs to be "consumed by this resistor... So R = V / I = 6/ .06 = 100 ohms.
Passenger Cabin - uses 4 LEDs so similarly the current needed is 4 x 0.020 amps = 0.080 amps flowing through the resistor that consumes 6 volts... R = V/I = 6 / 0.08 = 75 ohms.
Step 5: Final Thoughts ...
In the photos you can see how I weatherd the ship from the pure white paint job. I used two methods ..
- I dry brushed a little grime oround possible collection points, nooks and crannies such as panel haspes and engine thrusters. I used a burnt sienna, copper, a little gold and silver for this.
- I then followed up with a very thin wash of black to provide stains and runs. This wash actually caused my dry brushing to run as well and it turned out perfect with some minor dry brus touch ups as a third step.
Summary -
I really like the movie as it is so iconic and it is of my generation. The movie inspired George Lucas and Steven Spielberg amongst many other notables to think outside the box in movie making. To find a model like this was not within my reach so I decided to immerse myself into thinking how it was actually built which was just as fun as building it. The design process was a great joy to the point where I might just try to design my very own spaceship at the same scal to go with it. In short, I found it extremely satisfying to take a idea out of my head, CAD it, and produce it to hang in the rafters of my shop, and now everytime I turn on my shop lights, the Aries 1B is on its way to the moon!
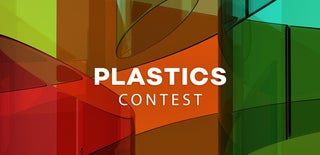
First Prize in the
Plastic Contest