Introduction: 3D Printed Natural-Color Cost-Effective Worklight (Extreme Attention to Detail)
So first let's clear things up. This light is:
- NOT messy job site type of work light.
- NOT weatherproof.
- NOT passively cooled.
This light is for individuals who want:
- Natural color lighting (High CRI of 90, no color shift).
- Bright and efficient light (105lm/w).
- Significantly extend the lifetime of an LED (by running it at low temp with active cooling).
- Light with a narrower illumination angle of ~100 degrees (narrower angle = more light in that spot).
- Cost-effective solution.
Why 3D printed > Bought one?
With all this out of the way, let's talk about why this light is better than those you can buy. Long version short - there are no lights that provide this quality-lighting with high efficiency and great cooling at the $50 price point. You either can buy work lights that have terrible color rendering or you can buy expensive studio-grade gear that has excellent colors. There is nothing in between.
But what does "color rendering" even means? Well, it means how well LED recreates visible colors to human eyes. The most basic system that classifies that is Color Rendering Index or CRI for short. The higher the value the more colors LED recreates. Our everyday light from the Sun has a CRI of 100. Cheap floodlights usually have a CRI of 65-70. Regular lighting at homes is around CRI80. Lights somewhere like in the art gallery CRI90+ and movie maker lights - CRI95+. And you probably heard that saying - that those incandescent light bulbs were better and LEDs doesn't feel right. And it is true if we only look at CRI. Because those very warm-looking bulbs have a CRI of 100. Yes, like the Sun. But as they are so inefficient (14lm/w) and short-lasting they just become completely obsolete.
So yes, colors are important but why cooling is so important too? Well, it not only extends the lifetime of the LED but also helps to maintain the higher brightness output. The hotter an LED chip runs the dimmer it gets, it's just a basic thing about the led chips, I won't go into details as it is very technical and boring for most folks (but here is the read for those you want to know).
3D printing provides that solid bought-light look. It is not necessary to print all those parts to enjoy the quality lighting, but it is necessary if you want the complete package that bought ones have - protected LED, protected fan blades, reflector for narrower illumination angle and etc.
In the next to the last picture, you can see how bad colors can look on a medium-quality worklight LED. I used one in my Portable-Indoor-Light project. It had decent brightness, but nothing compared to what you can buy now for the same price and way better colors.
In the last picture, you can see how much it cost me to make this light. Heatsink+fan cost me nothing because I had a few of them lying around for ages from my older CPUs. Other item prices can vary depending on where you live, but hopefully, it still will be ~$50.
So let's make it?
Provided links are affiliates.
Main Tools:
- 3D printer https://amzn.to/3syckJk
- 12V drill https://amzn.to/2U5QQmL
- Fretsaw https://amzn.to/33LcvVr
- Soldering kit https://amzn.to/2X0eCVq
- Multimeter https://amzn.to/3bLuEIx
- Wire strippers https://amzn.to/2ZR3KJp
- Cutting pliers https://amzn.to/3qTLNWC
- Hot glue gun https://amzn.to/3De5Jcx
Main Components & Materials:
- PETG filament https://amzn.to/3uF5QuC
- Intel stock cooler LGA1155 (local deals)
- Cree CMA 1840 90-95CRI LED https://bit.ly/cma1840 (Mouser.com)
- LED holders (choose CXA1830) https://s.click.aliexpress.com/e/_AKuJYf
- 50W LED driver https://amzn.to/302p8ix
- 50W LED driver Mean Well (alternative) https://amzn.to/3izJd5Y
- Step-down module LM2596HVS https://amzn.to/3B8xSRE or https://amzn.to/3B8xSRE
- M3x4.2x4.5 brass inserts https://s.click.aliexpress.com/e/_9jyysX
- M4x8 threaded inserts https://s.click.aliexpress.com/e/_AefWJv or https://amzn.to/3DL4BgP
- Light stand adapter https://s.click.aliexpress.com/e/_9hOWFt
Other Things:
Cables, wires, aluminum tape, double side tape, Kapton or electrical tape, wing nut, bolts, washers
Attachments
Step 1: LED on the Heatsink
For this build, I will be using an Intel stock cooler made for the LGA1155 CPU socket. It has mounting holes spaced 105mm apart diagonally, 115mm maximum width, and 48.5mm height. It is important to check those dimensions because those coolers have so many revisions and different sockets.
The fan has 4 wires, we only need yellow positive and black negative to power the fan later.
The Cree CMA1840 LED is only 18x18mm (17.85mm with 0.2mm deviation by datasheet) and it perfectly fit on this cooler. My heatsink variant had a copper core, which will make it more difficult to drill and tap holes. There are variants without the core, so I highly suggest using those if you want that this part would be way easier.
I used a 2.5mm drill bit and the M3 thread tap to make threaded holes for the M3 bolts. LED will be secured by the holder that is designed for different name CXA1830 LEDs. But as those LEDs have literally identical dimensions to the one that I am using in this project, it fits perfectly (the exact part link is on the first page). Add a thin thermal pad or thin coat of thermal paste on the back of the LED and secure it to the heatsink. I used MX-4 thermal paste.
To remove the spring clips from the cooler's legs you just lift the pin on the side and both parts come off.
Step 2: The Beginning of 3D Printing
With LED secured, I designed the housing for it. I just love the looks of it! But you know what I love even more? All the parts are designed in a way that you won't need any supports when 3D printing, NONE!
I used PETG filament, 3 walls, 25-30% zig-zag infill ratio, and 50% fan. Basically, you don't need any special settings to print this or any other parts.
Step 3: The Reflector
Next, I printed the reflector. It is a separate part because you can modify it yourself to fit any LED you want. If you gonna make one just a tip - make the part wider on the bottom and narrower at the top. You will need to sand it until you get an absolutely perfect and very firm fit.
I added aluminum tape to make the surface reflective. This is the only spot where the light doesn't look professionally made. I guess you could sand the surface and paint it, but remember that PETG isn't the greatest material to paint.
Then same with the inside ring of the mainframe. To trim the tape we need to use a sharp knife and it will be a piece of cake.
Step 4: Sanding the Spots; the Inserts
Usually, the top of the print will have small bumps and won't be perfectly flat. We need to fix that by sanding spots where other parts will be attached.
With that done, I started melting in the inserts. It is a very easy and satisfying process. You take the soldering iron with a clean tip, set it to the lowest setting (200C in my case), push in the insert and press it down with some sort of a block and hold for like 30 seconds until it cools down. This will give excellent results.
Those inserts at the top are for bolting the back fan grill. And ones in the bottom (the front of the light) for a protective glass holder.
Step 5: Reflector in Place
If the reflector fits perfectly in the frame and around the LED holder, we can glue it in with epoxy. Use just 8 small drops around it. It will hold firmly in place, but that will also let you rip it off if you want to change it like for a different size LED.
Step 6: Protective Glass
I used a fretsaw and cut a ~80mm circle from a 2mm thick acrylic (the hole in the holder is 83mm in diameter).
You can use anything that has good light transmission. Acrylic and plexiglass usually have ~92% light transmission. Yes, that means that you will lose ~8% of the brightness.
The cover can be secured with four M3x8mm bolts for now. Later you will need to secure the heatsink with M5x40mm bolts. It is easy to do while pinching the nut on the top and screwing the bolt from the bottom.
This already looks great!
Step 7: Power the Fan
As for this build, we will be using a constant current driver which will give ~37V with connected LED, we need to convert those 37V to lower 12V for the fan. So this part is a housing for the LM2596HVS step-down module.
Like before sand all surfaces that are going to be connected. To secure the part to the man frame I will be screwing in the M4x8mm threaded inserts. They are used in wood but work great with non-brittle plastics too. You will need four inserts. Two from both sides.
But I underestimated the strength of PETG. I printed the part with 75% infill and 5 lines. That made a hole that is such strong that the bit just splits the top of the insert when screwing in. I fixed it with the soldering iron just by melting in.
I used these inserts in other projects and it worked really well. So a suggestion for you is - use like 3 walls, 25% infill and it will be fine. And if you are still having problems, screw in the insert only halfway and then use the soldering iron to fully set it in.
Step 8: The Last Parts
To complete the printing process I printed the final three parts - the cover, the angle adjustment, and the clip holder part.
The last two parts use an M6x35mm hex head bolt, washer, and a wing nut to easily clamp at the required angle. Again no support is needed when printing. It is a great design. :)
Step 9: The Nut
You can mount the bottom piece to the light stand, but it is better to trim the wide M6 washed that all the clamping forces from a nut would spread over the bigger surface area of the plastic part.
Step 10: Light Stand Adapter
This part is designed to go onto the light stand adapter that has a 1/4" screw. It does not only provide a more secure hold but also allows for fast detachment from the stand. You will need a 10mm socket to secure the holder to the adapter.
And as you previously saw that the bolt was too long, I trimmed it from 40mm to 36mm to perfectly fit in this application. If you are wondering what jig it is, here is my instructable how to make one.
Step 11: Attaching Parts
To secure the mainframe to the step-down module housing part you will need two M4x20mm flush head bolts.
Step 12: Wiring Options
So, there are two options to wire this light:
- First - we use a short cable that goes from the AC-DC driver, which reduces power losses.
- Second, we use a long cable that goes from the AC-DC driver, it is more convenient but you get more power loss.
That is exactly what you see in the two photos. The first one is with the short cables and the second is with 5.4m of AWG 18 (2x0.75mm2) cable. And it is only a 0.4V drop. And I will need only ~3m of cable. So the drop will be even lover. Convenient option it is.
Step 13: Wiring Module
If you wonder what is the purpose of those weird shapes on the mainframe, well this is it - to more easily route the wires.
The hole in the side of the step-down module part is for a 5mm diameter cable. If it is too narrow you can always use a drill to widen it, and if it is too wide you can add heat shrink tubing on the cable to make it thicker. Before pushing in the cable make the surface of it rougher, because we will later need to hot glue it, it will bond way better.
To reduce the voltage from ~37V to 12V for a fan I am using the previously mentioned LM2596HVS step-down module. It is rated for 4.5V - 53V of input voltage.
Solder positive and negative wires from the LED and the constant current driver (I am using a Chinese 50W Chanzon brand driver) onto the module where it says IN+ and IN-.
DO NOT solder the wires from the fans next. First, we need to rotate the potentiometer and set it to desired lower voltage like 9-12V by using a multimeter clamped to the OUT contacts of the module.
Only then we can solder the fan wires. Also do not connect the step-down module alone to the constant current driver. It will not work or it can even damage the module. Always connect it with LED.
At this point, I already have printed the back grill. So I added it and measured the temperatures of the heatsink as close as possible to the LED. I ran the fan at 9.3V and after 10 minutes it only reached 33-34C. Remember that the temperature of the LED itself will be 10-20C higher, so don't lower the voltage for the fans too low.
Step 14: Module and Power Cable
Finally, we need to solder the wires from the fans to the module. Add Kapton tape (regular electrical tape works fine too) and glued the module with double side tape. And to secure the cable add a lot of hot glue around it.
Step 15: Finishing Assembly of the Light
Finally, to finish the assembly of the printed parts, you will need eight M3x10mm pan head bolts.
And to attach the angle adjustment part to the module housing part we will need two M4x15mm pan head bolts. Just don't forget to add the cover in between them.
And the light itself is done. Now we just need to wire it to the driver.
Step 16: Finishing the Light
So the final thing that we need to do is to power the LED with a constant current driver. What I like about this one is that you can disassemble it, desolder the wires, and solder your own cables from the LED and from the AC power cable. Remember that here we are dealing with the mains AC voltage so make sure you know what you are doing.
Those plastic covers that have screws clamp the cables very firmly and if not just add some heat shrink tube or electrical tape to increase the thickness of the cable.
With this done, I secured the driver and the cables neatly with velcro cable ties to a light stand.
Step 17: WE MADE IT!
The light quality is just beautiful! And it is a lot of light for the power. And if you wonder why the heck I need such a long cable from the driver to the light, well because the light stand extends and the length of the cable will need to be longer at the highest position.
The weight of the light with some cable is only 559 grams (20 oz). I probably could get away with a more simple angle adjustment. But this one requires very little force to firmly lock it in place so I can't complain.
The total power consumption at the socket is 58.1W. From previous measurements, the LED itself consumes 52.98W. Plus the 0.91W of the fan (fan @9.3V + step-down module). That leaves us with ~4W of wasted power (58-52.98-0.91=4.21W). That is ~93% (53.9/58.1*100=92.77%) efficiency.
The CMA1840 4000K LED itself makes 4817lm when ran at typical specifications (34.7V, 1.1A, 85C). We run it a little bit higher at 1.436A and cooler ~55C. So from the datasheet, we can calculate the approximate brightness when running at the higher current. That would be 4817lm x 1.27 = 6118lm. This is the number that everyone specifies on their products. That is 115lm/W for LED itself and 105lm/W total efficiency rating with a driver. Also, remember that higher color temperatures like 5700K will provide more lumens and that higher color rendering reduces lumens (the same LED with a CRI70 rating makes 6012lm vs 4817lm CRI90). With that in mind, 105lm/W is a great result even for store-bought studio light.
For people who want to shoot videos with this light:
For this build, I used the Chanzon brand power supply which is basically no name. I am very sensitive to a flicker on lights, but I don't see any with my naked eyes with this LED driver. However, when shooting videos you can slightly see the flicker if your shooting settings are incorrect. Meaning that you must use PAL(50Hz) or NTSC(60Hz) format correctly. This just means that for example in Europe (where AC mains power runs at 50Hz) you will set the format to PAL and you will shoot @25fps or @50fps. And in the United States (where AC runs at 60Hz), you set to NTSC, which makes videos @30fps or @60fps. This will eliminate any flickering.
I hope you liked the build. I spend a lot of time perfecting the design. So maybe give it a try if you need a light like this. :)
If you really like what I do you can support my work with Patreon - https://www.patreon.com/DIYPerspective
I hope you liked the project, till next time! :)
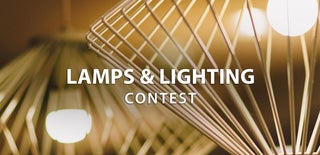
Second Prize in the
Lamps and Lighting Contest