Introduction: A Watch Like No Other
3D printers have been around for the general public for quite some time now and creations of 3D printed objects of all kinds are flooding on the internet.
On the other hand, one hasn’t been very successful, the watch.
I don't know if it’s because it no longer appeal to anyone, because Smartphones are here to tell the time or if it's due to 3D printing limits.
So a little challenge. I'm starting to design a 3D printed watch.
It’s sure that I will buy the movement, the glass, the screws and the crown. The rest will be 3D print.
Supplies
Price list:
Movement RONDA 505 10 1/2": 14.22 €
Watch strap: 0.96 €
Strap flange: 0.05 €
Case middle: 0.13 €
Box bottom: 0.04 €
Pin buckle: 0.05 €
Tip Pin buckle: 0.01 €
Handle screw: 0.62 €
Dial: 0.02 €
O-ring seal: 0.14 €
Hour hand: 0.10 €
Minute hand: 0.10 €
Second hand: 0.10 €
4 stainless steel screws M1.2x3.2mm case bottom: 0.40 €
4 Nuts M1.2mm case middle: 0.085 €
Acrylic glass: 7.90 €
Crown: 0.17 €
Battery Renata 371: 0.50 €
Total: 25,595 € excluding VAT
Links for components:
FILEMENT Ø1.75 PLA BLIN orange DAILYFIL 0.5kg
FILEMENT Ø1.75 TPU FILAFLEX RECREUS vert 250g
FILEMENT Ø1.75 PLA blue/grey ARIANE-PLAST 1kg
Assortment of black hands for watches BA180 réf 7072gs-H-05
Set crowns for quartz watches with seal réf 7029fn-T-45
BULLONGÈ assortment of 40 Handle screws réf 0905abh-H-34
Set of watchmaker's screws BULLONGÈ MICRO réf 7722gh-A-34
Seal PREMIUM Ø 0,7mm réf 0270ae-A-28
600pcs Stainless Steel Screws and Nuts
Step 1: For Designing
I've been using a little drawing software for quite a few years. I bought a license years ago because free industrial design softwares were not available and not very advance. Today anyone who wants to draw has all kinds of free options and doesn’t need to ruin himself to draw, they do the job really well (example: autodesk fusion 360)
Step 2: For the 3D Printer
I am equipped with an artillery sidewinder x2.
Here too the choice is vast. The only constraint I recommend is to have the "direct drive". This means that the filament is driven as close as possible to the extruder. So there is no long ptfe tube between the filament driver and the extrusion part.
Step 3: The Watch Strap
As the watch strap will be printed with a flexible material, it is important that the drive motor of this filament is done as closer to the extrusion, otherwise there will be fluctuations in material flow because the filament can twist in the ptfe tube.
This does not mean that it does not work, but there may be large irregularities in the printing of the watch strap and therefore the chances of achieving the precisely drawn geometries will be compromised.
Step 4: Choice of Plastic Material
The choice of plastic material for the watch strap is a TPU with a hardness of 82 shoreA.
The elastic properties of this plastic are excellent, it can stretch by 700% while regaining its original shape and strength.
Step 5: Important
This is very important because the case middle part, which is the central part that will house the movement, will be in PLA, it will be forced in the central part of the watch strap.
Step 6: This TPU
For this TPU, it is not necessary to put the heating bed surface. But in order to avoid havingthe reliefs of my Ultrabase bed under the surface of the watch strap, I decided to heat it to 60°. The extrusion temperature at 235° with a speed of 30mm/s, a 0.3mm nozzle and 0.2mm thick layers.
The rectangular central part of the watch strap must have good rigidity so it will not deform when the branches of the watch strap are on the wrist. I therefore apply a filling rate of 60%. The branches of the watch strap will remain very flexible thanks to the fluted lower shape.
The grooved shape in contact with the skin will also serve as an antiperspirant thanks to the circulation of air through these grooves.
Step 7: Here the Bracelet Being Printed
Step 8: I Also Print Other Bracelet Colors
Step 9: The Ring
Step 10: The Case Middle Part
For the case middle part, which is the central part hosting the movement, I will use a PLA plastic with a metallic finish thanks to its high glitter content.
The advantage, apart from the aesthetic side of this plastic material, is that it’s very robust due to its high glitter content load compared to other standard PLA. I need this solidity because the circular sections of the central part are thin. The part must not shear during its introduction into the watch strap.
Step 11: Print on the Face Side of the Watch
The part is printed on the face side of the watch in order to avoid making bridges for the support on the bottom side, as there will be a small section Oring seal in the groove. This groove must be kept clean. The watch must be dustproof. Bridges are needed during extrusion to support overhanging material.
For extrusion settings:
- 0.3mm nozzle
- Speed at 30 mm/s
- Extruder temperature at 215°
- Bed temperature at 70°
- Filling rate at 60%
- Layers thickness 0.15 mm
Step 12: The Box Bottom
I immediately print the box bottom with the same parameters.
Step 13: The Pin Buckle
With the same parameters, I print the pin buckle at 100% filling.
To transform the 3D part into a file for printing on your 3D printer, I use paid software "Simplify3D" called slicer.
I recommend that you rather use free software like "Cura", it is very widespread and the evolutions are well followed whereas on Simplify3D, there are no more updates and it crashes regularly. The reason why I use Simplify 3D is that I don't know Cura, but I will make the switch soon.
Step 14: Attach the Pin Buckle
To attach the pin buckle to the end of the watch strap, I use a handle screw that I cut to the same width as the pin buckle. To assemble it, it is necessary, on one side to force the rivet in the form of a screw into the metallic handle tube, and on the other side to screw the appropriate screw.
Step 15: Stainless Steel Handles Tube
The box of the different versions available of stainless steel handles tube. For the project, I used the Ø 3.5 mm screw head.
Step 16: The Dial
The printing of the dial was the most delicate step because its thickness must not exceed 0.4 mm. The space between the movement and the hands does not tolerate more than 0.5mm, otherwise the hour hand will rub against the dial.
Step 17: Printing of the Dial
The printing must be done in two times.
• Once for the colored number which will be extruded with a thickness of 0.1 mm and in inverted mode on the bed. The visible face of the dial will be face on the bed of the printer.
• And the second time, the printing of the white dial in two overlapped layers of 0.2mm. As the first layer of the dial is 0.2mm thick, it will pass over the numbers covering them. There are two separate files and they will be printed separately.
You must leave the heating bed at temperature between the two filaments changes.
The origin reference for the position of both files must be the same on the bed.
To improve the adhesion of the dial to the bed during the extrusion I gave a small spray of adhesive on the surface of the bed. Don't put to much of the adhesive spray because you won't be able to peel off the dial anymore. Use a thin blade to peel it off.
Step 18: Different Elements
Here above, a sectional view of the different elements that make the watch.
- We can clearly see the little space left between the dial and the hands.
- The box bottom is screwed to the case middle by 4 M1.2x3 stainless steel screws.
- 4x M1.2mm nuts are inserted into their housings provided in the case middle.
- An Oring seal is in the groove of the case middle and ensures dust tightness.
- The acrylic glass is bonded with a silicone adhesive to guarantee watertightness and its good hold in the housing of the case middle.
- The movement is held in position on the internal stop in the case middle, the box bottom locks it once in place.
Step 19: Nuts M1.2
The 4x M1.2mm nuts have been inserted.
Step 20: Insert the Case Middle
Insert the case middle in the center by pulling on the watch strapp. Do not hesitate to force the watch strap to put it in place. Pull with small pliers the tiny cylinder through the passage hole for the crown rod of the watch.
Step 21: Case Middle Is in Place
Once the case middle is in place, cut the excess of the cylinder flush.
Step 22: Go Down by Punching
Down punch with the tip shank of a Ø1.2 mm drill bit previously ground to a point.
Step 23: Center Point
The center point is created on the 3D file of the bracelet, it is made during the print.
Step 24: To Punch in the Axis
I made myself an assembly with a stem and a small vice to be able to punch in the axis of the hole for the passage of the crown rod.
I heat up slowly the tip with a blowtorch for "Creme brulee" then I punch in the axis.
Step 25: Assembly Acrylic Glass
Assembly of the Ø 25mm acrylic glass.
Acrylic glass is made of so-called plexiglass. It is sensitive to scratches. For handling, I use finger guards.
Step 26: Bonding the Glass With Silicone Glue
I apply the silicone glue using a toothpick only in the interior corner of the circular groove of the case middle.
Step 27: Pressing the Glass
Pressing the glass for a few moments. Allow 24 hours for the bonding to take before handling.
Step 28: Preparation of the Swiss Movement Ronda 505 HT2
Step 29: Remove the Crown Rod
To remove the crown rod, take a small cylindrical rod and press in the hole provided for this purpose while pulling on the crown rod.
Be careful, before pressing, the position of the crown rod must be in position n°2, the date change position.
To support the movement in good conditions, it is preferable to use a movement holder.
Step 30: Dial Above It
Flip the movement in the movement holder. Carefully position the dial above it, orienting the date window in front of the number at 3 o'clock, to the crown rod side.
Step 31: Assembly of the Hands
The assembly of the hands on the movement must be carried out with the tools for fitting the hands.
Match the diameters of the tool tips with the hand axis diameter.
Example: hour hand with the gray tip tool Ø1.50
Step 32: Choice of Hands
The choice of hands is given by the technical characteristics of the diameters of the axes of the movement.
For this Ronda movement, the diameters of the hands are:
- hour hand = Ø 1.2 mm
- minute hand = Ø 0.70 mm
- seconds hand = Ø 0.20 mm
The maximum length I need for the seconds and minutes hands is 11 mm so that they don't touch the inside diameter of the case middle.
Step 33: Fitting the Hands
Maximum driving force:
- Hour and minute hands: max. 40N
- Seconds hand: max. 30N
When fitting the hands, the movement must be supported with the appropriate movement holder to prevent the pivot stone from coming out of its housing when fitting the seconds hand.
Step 34: I Take the Risk
Not having a movement holder recommended by the manufacturer, I take the risk to put the hands.
Step 35: Always Put the Hands at 12 O'clock
Putting in place the hands is done in the following order: hour hand, minute hand and second hand.
Always put the hands at 12 o'clock so that the date change takes place at midnight.
Step 36: Put the Movement in the Case Middle
Match the two top and bottom notches with the same shape in the inside diameter of the case middle.
Step 37: The Crown
My choice is determined by the diameter of the crown tube. This tube will correspond to the diameter of the punching carried out on the watchstrap while keeping a little tightness to be able to keep the seal against dust. Here it is 1.2mm
The diameter of the crown must not exceed the thickness of the watch strap, I chose a diameter of 4.5 mm, which is still sufficient for a good grip for setting the time.
Step 38: Screw the Crown on Its Rod
I screw the crown on its rod and I introduce it into the punching hole while making a few rotations until the movement. Once the assembly is well positioned, I measure the space between the edge of the watch strap and the inside of the crown.
I then turn the watch over and remove the stem crown as indicated in the "preparation of the movement" by putting the stem in position n°2 and using the small cylindrical stem to press in the hole provided for this purpose to remove the rod.
Step 39: Cut the Rod
I cut with a cutting pliers the value that I measured beforehand, leaving 0.2mm more.
Step 40: Deburr
I deburr, on a stone, the rod mounted in a small hand chuck.
I screw the crown until it locks so that it does not loosen during time-setting operations.
Step 41: Clean the Rod
I clean the rod with Rodico paste to remove any filings from cutting and deburring.
Step 42: Lubricate the Parts
Before putting the crown rod back in position in the watch, it is necessary to lubricate the parts which will be in contact with the gear mechanism.
For this I use a small watchmaker's tool equipped with felts previously coated with Microgliss D5 oil.
This tool allows you to grease just the right amount on the rod.
Step 43: Insert the Crown Stem
Insert the crown stem assembly into the watch as far as the back, rotating the crown slightly.
Step 44: The Battery Location
Turn the watch and put the insulator where the battery location is.
Step 45: Insert the Battery
Completely loosen the battery compartment retaining screw.
Insert the Renata 371 battery into its housing using non-conductive tweezers to avoid discharging the battery.
Step 46: Replace the Screw
Step 47: No Dust
Before closing the watch with the box bottom, I make sure, by applying the Rodico, that there will be no dust.
Step 48: The Seal
In this assortment of seals with a section of 0.7mm, I chose a Ø26mm outer seal.
I put it around the box bottom diameter.
Step 49: Screwing the Box Bottom
Screwing the box bottom with 4x M1.2x3.2mm stainless steel screws.
Step 50: Put the Watch on My Wrist
Step 51: The Challenge
This is the project coming to an end. If you want to take up the challenge.
Step 52: For Christmas Caroline's Gift
With wood boxes cut to custom made by the laser machine.
Step 53: For Christmas Jessica's Gift
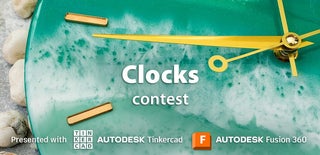
Runner Up in the
Clocks Contest