Introduction: Cinematic Spotlight RGB Panels for Creative DIY Color Mixing
In this instructable/video - how to make spotlight type RGB panels for getting cinematic and creative lighting. The key part of the panels is the light diffusion sheet from a broken laptop screen. It gives spotlight type effect for way better color mixing than without it. You can get really good contrast lighting with panels like these.
Provided Amazon links are affiliates.
Main Tools:
- 20V cordless drill https://amzn.to/2MY3GRt
- Jigsaw https://amzn.to/2rg4uXx
- Router https://amzn.to/2DVXXZC
- Rotary tool https://amzn.to/2MWaP4H
- Speed square https://amzn.to/2Ee6lDh
- Clamps https://amzn.to/2YKWmRS
- Acrylic cutting knife https://amzn.to/2TZ1645
- Tape measure https://amzn.to/2rfS4Ph
- Multimeter https://amzn.to/2MTl4Xs
- Diagonal cutting pliers: https://amzn.to/2E8vOz5
- Wire stripper: https://amzn.to/2E8Qk2W
- Wire cutting pliers https://amzn.to/2rvrL80
- Soldering kit: https://amzn.to/2Q613Bf
- Hot glue gun https://amzn.to/2PdCgpI
Main Components & Materials:
- RGB LED strip 16.4ft/5M https://amzn.to/2skbFCc
- RGB LED music controller https://amzn.to/2Q64WVk
- Electronics component box (local electronics shop)
- 3.7V 18650 batteries (can reuse it from an old laptop or can buy from a local electronics shop)
- 12.6V 3S 5-8A battery protection and charge circuit https://amzn.to/2Q2lc9U
- (Instead of using 3-5A circuit, better just add a fuse of the max discharge rate of your batteries. HOW TO CONNECT scheme you should find in the item pictures http://bit.ly/356IpMu)
- 18650 battery holders https://amzn.to/356xAKh
- Switches https://amzn.to/2SG1BhD
- Power connectors https://amzn.to/2ZyYWru
- Battery capacity indicator https://amzn.to/2SC68kP or alternative https://amzn.to/2SC68kP (can connect directly to the batteries as it already has an integrated switch)
- Polystyrene/plexiglass sheet (local hardware shop)
- Plywood or wood strips/boards (local hardware shop)
Other Things:
Camera hot-shoe adapter, wires, rosin flux, fuses, battery pack PVC heat shrink wrap, aluminum tape, double side tape, small screws, small metal or plastic bolts and nuts, step drill bit.
You can follow me:
- YouTube: https://www.youtube.com/diyperspective
- Instagram: https://www.instagram.com/diyperspective
- Twitter: https://twitter.com/diyperspective
- Facebook: https://www.facebook.com/diyperspective
Step 1: Preview
The key component here is the light diffusion sheet from a broken laptop screen.
Without it, you will get only bland effect, meanwhile with it - really good contrast, two-color lighting. Panels also can be used as music lighting, as the controller has an integrated microphone.
Not only that, panels don’t make any visible flicker on cameras, even on the low brightness, which is great if you are recording a video.
Like what I do? Consider becoming a PATRON! This is a great way to support my work and get extra benefits! https://www.patreon.com/DIYPerspective
Step 2:
Once these laptop displays were pretty good, but now they aren’t worth reusing anywhere. I am talking about CCFL TN display panels to be exact.
Color reproduction and viewing angles are quite bad on these, so there is no reason to make it into a standalone display. And as they use CCFL lighting, which basically is a thin fluorescent light tube, efficiency and longevity are already gone after many years of use.
You possibly could make a regular light panel from the displays, but as fluorescent lights need converters to raise the voltage to something like 1500V, I am not really comfortable messing with it.
Step 3:
If you take your time and willing to carefully disassemble the screen, you can find very unique diffusion sheets inside. And by careful, I mean by not smashing or bending the panel. Because if you brake CCFL light in the panel there are mercury vapors inside like in any fluorescent light. And they are toxic, so you definitely don’t want to breathe them in.
Once you have completely disassembled the panel (I tested only TN CCFL and TN LED panels) you will find some different types of layers.
First is the matrix, which I think doesn’t have much reuse value. Then we can usually find two basic light diffusion sheets and two unique ones. Those have two different sides. From one side, light is diffused to the center, and you can’t see much at an angle.
Step 4:
Another very interesting effect that those unique diffusion sheets make is this - when looking at an angle, it makes individual led strip diodes look like they are tied in a wavy pattern. It definitely looks really cool and can be made into a very unique lighting solution.
But for this project, we only care about the unique sheets, because they make spotlight diffusion effect.
Step 5:
We can reuse a thick transparent plastic layer. Just keep in mind that it is always thinner on one side. As this is a 17-inch panel, I cut those parts in half. Because for color mixing, we need at least 2 panels.
Step 6:
To make the frame for the diffusion parts, I cut them from a 12mm thick plywood. The frame will make some space for the wires inside and will give more sturdiness. If you don’t care about aesthetics, you can easily just cut 4 strips from a thin wood board and later just screw the diffuser on top without routing the rabbets.
Step 7:
Next, we need the exact same size plastic sheet as the outer frame that we made. I used a new polystyrene/plexiglass sheet because it is very easy to cut it. But if you have patience you can reuse the back plastic of the screen frame in which the panel was.
On the back sheet, we need to glue reflective aluminum tape. It will also help with heat dissipation from the LEDs. I glued 10 rows of 15cm length strips, but you can easily double it if you need more brightness. You can always lower it later with a remote. I just ran out of the RGB strip. But also remember the more strips - the more soldering it will be.
Step 8:
And oh boy, the soldering will take a lot of time. You better have the patience for it. Not only you need to cut billions of wires, but you also need to very carefully solder them to the contacts. We will definitely need a rosin flux which helps the solder to stick instantly to the surface.
All the strips need to be soldered in series, it’s a good idea to add electrical tape where the end of the contacts are.
Step 9:
One big problem that you might encounter after soldering all wires - is flickering of other color LEDs.
As contacts are so tiny, this usually can happen because of the bad solder joints or not cleaned leftover rosin flux. What I recommend, is to power each color LED channel after soldering one strip at a time. This way you will always know if wires are soldered properly.
Step 10:
Now I should overview other components that we will use for the one panel. We’ll need:
- 1x electronics component box
- 3x 18650 3.7V li-ion batteries
- 6x DIY holders for batteries
- 1x ideally 3-5A protection and charge circuit board for the batteries
- 1x switch
- 1x charging port
- 1x battery capacity indicator
- 1x RGB music controller
This controller has function to flash LEDs by the rhythm of music, but it also doesn’t produce any flickers on a camera. A few other more expensive ones that I tested, had very bad flickers, so be aware of that.
Step 11:
In the box we need to make a hole for the display, it can be done with a Dremel like tool and some sanding. Three holes for the switch, charge port, and the receiver can be easily made without cracking the box with a step drill bit.
Step 12:
To protect the batteries, we need to place them into the holders, glue protection circuit and add rosin flux on all contacts where wires will be. Now we can add solder and start connecting wires to the circuit first and then to the batteries.
To be correct, this is not the circuit you want to use for NOT high discharge rate batteries. This is a 20A discharge circuit and the batteries usually have ~5A max discharge rate. So, you should use a protection board similar to that rate.
Step 13:
After I sprayed the frame with black paint, now we can start assembling the panel. First, we just glue it with double side tape to hold the parts in place. Then we can make the hole for the wires from LEDs to the box, make four holes for the screws and secure two parts together. I used plastic screws as this is a very light panel. And for the outside – regular small wood screws.
Step 14:
Next, we can solder extension wires to the nearby contacts and add some hot glue.
We don’t really need the enclosure of the controller as all wires will be re-soldered to better fit in the main box.
On the other side, we can solder them to the controller by the name of a color. Again, as I want to have less clutter of wires, I just de-soldered, trimmed and re-soldered wires.
Step 15:
It’s a good idea to insulate battery contacts with some heat shrink plastic wrap, it is a very satisfying and quick process.
Step 16:
This is how it looks with everything inside. The connection of all parts is pretty straight forward.
- Charging port wires with a fuse connects directly to the protection circuit on the battery.
- Negative wires from the display and RGB controller also goes to the battery.
- Positive wires to the switch and then to the batteries.
And that’s it, a very basic circuit.
Step 17:
On the back cover, we can glue the standard camera hot-shoe adapter for placing the panel on the articulating arm. And of course, the hole for the microphone on the controller board if you will use it to recreate rhythm of the music with the lighting.
Step 18:
To secure the front diffuser, I just used four screws. And like that, the panel is finished. To charge it we can use a basic 12.6V 2A Li-ion battery charger.
Step 19:
And now here are the results with spotlight diffusion and without it. There is a huge difference in angle the panel is lighting everything up, but not much to the overall brightness in the center. So why you would want to do that? Well, again it’s all about the color mixing.
This diffuser gives pretty much perfect spotlight for that. It is not too hard and narrow, and not too soft and too wide. Without the diffusion sheets, you would never get this kind of high color contrast lighting.
So yeah, it seems it is a very simple thing to make, but it is not if you really care about getting that creative lighting by mixing the colors.
Step 20: END
I hope this instructable / video was useful and informative.
If you liked it, you can support me by liking this Instructable / YouTube video and subscribing for more future content. Feel free to leave any questions about this build.
Thank you, for reading / watching! Till next time! :)
You can follow me:
- YouTube: https://www.youtube.com/diyperspective
- Instagram: https://www.instagram.com/diyperspective
You can support my work:
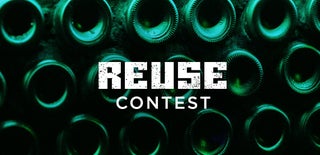
Participated in the
Reuse Contest