Introduction: Coffee Table - Walnut, Maple and Steel
Finished product first.
Step 1: Dimensioning the Lumber 1/5
I got really lucky and saw an ad on Craigslist for walnut that had been drying out for 20 years for $4 a board foot. It was all rough-sawn, so I need to mill it down. I also picked up a maple board from the local woodworking store for the stripes.
Step 2: Dimensioning the Lumber 2/5
I started by running a face of each board through the jointer...
Step 3: Dimensioning the Lumber 3/5
... and then running the flat face against the fence of the jointer to flatten an edge (in this particular shot I was running an edge through first because this board had to be ripped on the table saw before it could fit through my 6 1/8" jointer-- I went back and re-milled it afterward).
Step 4: Dimensioning the Lumber 4/5
I then planed each board with the jointed side down, resulting in 3 out of 4 sides of the boards being flattened/true.
Step 5: Dimensioning the Lumber 5/5
Lastly, I ripped each board to its final width-- 6" for the 3 walnut boards and 3" for the 2 strips of maple. I also trimmed all 5 boards to their final length of 48".
Step 6: The Glue-up 1/3
Here I am starting the glue-up. I just used regular Titebond II. My next project will be a nice, big, flat workbench, after doing this on the floor of my garage...
Step 7: The Glue-up 2/3
Glue-up went pretty well... I think I had everything in place and clamped within about 10 minutes.
Step 8: The Glue-up 3/3
I've learned from the past that wiping off the excess glue with a wet rag before it dries is WELL worth it.
Step 9: Filling Holes With Epoxy
I filled in a couple little wormholes with regular 2-part epoxy. I think the brand I used was Gorilla Glue.
Step 10: Sanding
I sanded all the way up to 320 with an orbital sander, then hand sanded with 400-grit.
Step 11: Finishing the Wood 1/2
I used Watco Butcher Block finish as the only finish on the tabletop. It isn't the most protective finish, and requires a little maintenance, but I love the look and feel of it.
Step 12: Finishing the Wood 2/2
You can see here how it really brings out the natural character of the wood, and leaves the maple nice and white.
Step 13: Cutting the Base
For the steel base I used 1/2" angle iron. The final dimension were 1/2" shorter than the top on all sides to leave a 1/2" overhang, so 23" x 47".
Step 14: Welding the Base
I welded the base together, keeping everything as square and lined up as possible.
Step 15: Painting the Base
I used this flat black product by Rust-oleum and am very happy with the results. I got a couple of drips, but I sanded them off and applied a light second coat.
Step 16: Attaching the Top to the Base 1/3
At first I was going to just drill holes through the base and screw the top right to it, but then considered that as the wood naturally expanded and contracted over time, it wouldn't have any room to do so if it was mounted directly to the steel frame. Instead, I used these clips that are meant for window screens.
Step 17: Attaching the Top to the Base 2/3
I drilled pilot holes first, as I really didn't want to split the wood at this point...
Step 18: Attaching the Top to the Base 3/3
The clips have been working great-- they keep the base on very firmly, but do have some give to them if the wood decides that it needs a little more breathing room someday.
Step 19: Finished Pictures
And here's the finished product in the place where it'll live for quite some time, hopefully!
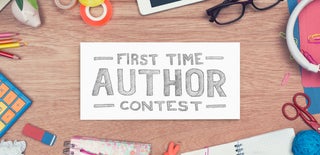
Participated in the
First Time Author Contest 2018