Introduction: DIY Bluetooth Boombox - Repurpose Your Old Hi-Fi
For this project I will be making a bluetooth speaker using secondhand bookshelf speakers. I will go through the design process and all the different stages of construction, this will be a comprehensive guide to building a your very own Hi-Fi quality boombox.
You will need:
- A pair of bookshelf speakers
- TDA7492P Wireless Bluetooth 4.0 Audio Receiver Digital Amplifier Board
- A latching switch (optional)
- A power supply between 9v and 24v (higher the better)
- 2 part automotive body filler
- Primer
- Top coat
- A small piece of perforated steel or ally (optional)
- pcb stand-offs
Tools:
- Soldering iron (can possibly use chocolate boxes for connections instead if no switch is used)
- Electric Drill
- Screwdriver
- chop saw or a table saw or even a bandsaw ( could also be done by hand if careful)
- Router (optional)
- Sander (optional)
- Jig saw (could also use a coping saw or hole cutter on a drill)
Step 1: What Speakers?
In short you can use any bookshelf speakers to make this project work, I purchased three pairs. One for £5, one for £8 and the last for £20.
I started by looking at the quality of speakers I purchased, I noticed a broad variety of construction methods.
The most expensive speaker cabinet was made from a variety of materials. It has rigid composite supports that tie the baffle board to the rest of the enclosure. The moulds required to make this speaker would have been costly to make. The mid range speaker is made from chipboard and is relatively strong. It has a thick, strong baffle board. Recessed into it are the tweeter and bass driver. It is a simple but tried and tested method. The last cabinet (cheapest) is thin, flimsy chipboard. It is joined in a basic fashion using glue and small nails. It is cheap, mass produced and is the weakest of the three.
Step 2: An In-depth Look
I decided to take a closer look at most expensive of the three, the Mission 731. It uses three different seals to keep the enclosure as airtight as possible.
Seal one: rubber gasket running around the edge of the baffle board. This is compressed to form a tight seal as the enclosure is put together.
Seal two: a foam pad around the front of the bass driver. This is squeezed shut when the driver is mounted to the baffle board.
Seal three: there’s a relatively thin gasket around the tweeter; however this is all that is needed. This is due to the large surface area the gasket has. Unlike the bass driver, the tweeter is able to have large mounting flange due to its compact size.
Step 3: Calculating Volume
To measure the volume of the enclosure I needed to think outside the box. I knew I could not calculate the volume like I would a normal box, using maths. This was due to the complicated bracing system used inside the enclosure.
While 3D scanning and photo-mapping could have been used to get an accurate volume measurement it would’ve been expensive and hard to calibrate.
I also considered using callipers to take height and depth measurements. This could’ve made a rough plotting guide I could use to make a model in CAD. All of these ideas where unnecessarily complicated.
In the end I decided to use a measuring jug full of water to fill up the cabinet. This allowed me to accurately measure the internal volume of the cabinet in litres.
Before I could start pouring water I first needed to plug the binding post terminal holes. I used the original binding posts and silicon to do this.
I also sprayed to inside walls of the enclosure to stop the distorting when filled with water, thus giving an inaccurate reading.
We need to calculate the volume so as to replicate the tuning of the original enclosure, keeping the speakers sounding clean and refined.
Step 4: Designing an Enclosure
I used an online speaker box calculator (diyaudioandvideo.com/Calculator/SpeakerBoxVolume) to make a box the same volume as two enclosures and then made it from birch ply.
I used a jigsaw for the speaker holes, but a router and a circle guide would be neater.
The corners are mitred at 45 and the front panel is sitting in 5mm groove 10mm inset. The groove adds a lot of strength and is a great help when gluing up those tricky mitres (use a tacky glue).
The baffle on the front driver is doubled up for a bit of strength and rigidity. 9mm ply was cut for the back, it was hand planed to a tight push-fit (boxes never end up as square as you hope!)
I used a 1/4 round-over bit on a handheld router to round the edges but sandpaper will work fine too.
Step 5: Finishing
I painted the front panel with some cheap black paint and mocked everything up to make sure it fit.
After this I filled all the holes with a 2 part car body filler as it works a lot better than nasty wood filler.
The four holes you can see in the second picture are for the machine screws that attach the pcb stand-offs to the enclosure.
After filling and sanding I sprayed the enclosure with two coats of white primer, then sanded to 240 and sprayed my top colour coat. I then cleaned up the front and back edges with a block of wood and some sandpaper to show the birch ply.
Walnut offcuts where screwed to the bottom (countersunk) to make feet. This allows space for the driver, as well as preventing scratches to the finish.
Step 6: Electronics
I ran my speakers bridged from the amp as I wanted more power, however it does distort slightly at it's highest volume. Use the amp normally - left speaker output to left speaker and so on - if you want to avoid this.
I use 3mm dowel to push the surface mount switches on the PCB.
At this point in time there are no batteries. When I find a suitable charging system I may well consider them.
The electronics in this circuit are quite basic, all you need is a soldering iron and a bit of patience. There are many tutorials on soldering here on Instructables should you need any help.
Step 7: Grille
For the grille I used a 1.5mm plate of perforated steel, I bent it using a mallet a bit of 2x3. I used a chop saw to cut the corners.
The grille will eventually be powder-coated in an off-white (when I have the time!).
Step 8: Finished!
I now use this everyday to play music while I'm in the shower and getting ready for work. It's not crazy loud, but is clear, crisp and clean. I occasionally use it for garden parties as background music, it always gets compliments on the sound and aesthetics, so overall I'm very pleased.
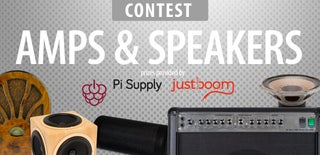
Runner Up in the
Amps and Speakers Contest 2016
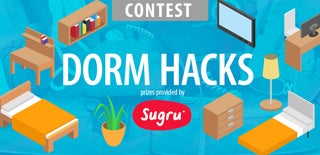
Participated in the
Dorm Hacks Contest 2016