Introduction: DIY Custom Wedding Bands
So this instructable is how to make your own wedding rings if you are on a tight budget like we are. It does involve a lot of tools/equipment that the average Joe probably won't have laying around. So just FYI.
Here is a list of tools you will need: A ring to design from if you wanting it to match (we have an heirloom that we wanted to match up with)
A measuring caliper
3D design program (I used 3d Studio Max 2015)
A clean surface and proper ventilation
Casting flask and rubber flask bottom
Hot pen for sprueing and any minor fixes.
Wax sprues
Needle file set
half round fine file
goo-gone
nylon
mold investment powder and distilled water
a bowl for mixing
a scale
a graduated cylinder
a spatula
masking tape
a vacuum table for the investment and casting
a kiln
heat proof gloves
a heat apron
latex gloves
safety glasses and welders glasses
a electromelt crucible (or a way to get your metal to melting point)
tongs to take your mold out of the kiln safely
a big tub of water
a torch
pickling liquid
sand paper of different grits
a dremel tool with attachments
polishing compound
Step 1: Measuring and Designing
When you have an engagement ring that is an heirloom and doesn't have a matching wedding band. A good way to get what you want is to take it to a jeweler and ask them to design something. OR you could do it yourself if you have the tools readily available for you. If you do have the tools and the ability to make them on your own, it could save you a lot of money and trouble.
When I started thinking about what I wanted for a wedding band, I knew I wanted something that my engagement ring would set into.
Grab your measuring calipers and start measuring every last measurement you could get from the ring. The height of the band, the diameter of the pearl, the width and height of the table, the size of the prongs, any tapering the band may have, etc. and write them all done. Also make sure you get the ring size you want the ring/rings to be. You can find a ring size converting chart online so you can get the diameter you will need.
At this point you could sketch out your idea, but its not necessary if you don't think. Mine was pretty simple, so I went straight to the next step.
Step 2: Modeling Your Idea for Printing
You then will go into your 3D designing program (I used 3d Studio Max) and start modeling. Make sure you have your units set up for easy measurement so you get the right dimensions on your model.
I started by making a sphere for the pearl and then started making the ring models. Both mine and my fiancee's rings set on either side of the pearl. So I needed to make a spot for the prong in the model as well as make it so it would wrap around the pearl.
Once you have the look you want, export it and get it printed in castable wax. You can print it yourself if you have the tools and ability, but we just ordered it off of Shapeways.
Step 3: Fixing and Polishing the Wax
When you get the castable wax, it is very fragile. So if you break it, like I did, you might need to fix it. So what I did was take a wax sprue, and lightly heated it to where I could flatten it to match the width of the band and made a new band to attach. I then took a hot pen and attached it. Then you will need to take your needle files and clean it up a bit. Be careful as the wax is still very fragile. Gentle touch is key. Use the files to file away any extra wax and match it up with the engagement ring as close as you can get it. You can see in the second photo how our rings sit perfectly with it.
Once you have it filed down and nice and clean, you can use Goo Gone and some nylon (the little nylon socks you can get at shoe stores work great) and lightly wipe the surface of the wax. The Goo Gone will "melt" the surface and make it nice and clean. It will get rid of any print lines or file marks. But don't use too much, since it melts the wax, you could end up ruining it.
Step 4: Sprueing the Model
So once you have your model all ready to cast, the next step will be adding the wax sprues for the channels in which the metal flows through. You want the shortest sprues, because the longer they are the more weight it will add to the model and the more metal you will need to melt to cast. You can see in the photos I kept them very short. I casted both rings together as to save on materials and time. When you sprue, a good idea is to make sure #1 that you don't have any 90 degree angles. Metal doesn't like to flow at a 90 degree angle. And secondly, I like to have the "heaviest" spot towards the bottom of casting flask. It has worked the best for me in the past.
On these I sprued right on the front so it was an easier clean up at the end. So get your hot pen out again and sprue your model. Before you sprue it to the flask bottom, you want to weigh your model. The weight of it will determine how much metal you will need when you go to cast it. You want to weigh it in grams if possible.
Then after you weigh it, you want to sprue it on the flask bottom, attach it to the "button". What you want to also make sure of is that your "joints" on your spruing, is a nice flowing look. Almost like a flare out on each. Even when you put it on the flask bottom, make sure it flares out so the metal flows well.
Step 5: Making Your Mold
Once you have your model sprued to the flask bottom, you are ready to start pouring and setting your investment. You will put the casting flask onto the flask bottom and make sure there are no openings. Make sure it is on nice and tight. Next, you will want to take a piece of masking tape (I use the extra wide tape) and put it around the top of the flask. This will minimize investment "splashing" when you vacuum it.
Depending on your flask size, you will need to figure out the amount of investment powder and distilled water you will need. Mine was 1.8 pounds of investment powder and 267 milliliters of water. You want to make sure when you are pouring your water, that you pour it like a good beer pour. turn the graduated cylinder sideways to prevent bubbles forming. Same when you pour it into the mixing bowl with the powder to mix. You want to pour it on the side.
Once you have the mixture mixed to a good "yogurt" consistency, you want to put it on the vacuum table with the cover over it to vacuum out all the bubbles. A good 90 seconds will work. Then pour it into your flask. Pour it around the sides of the mold, the weight of it could hurt your wax. This way it will move around the wax without hurting it.
Once you have it in the flask, put that on the vacuum table and do the same as you did with the mixing bowl. After the 90 seconds, let it sit for a good 20 minutes.
Then pop the flask bottom off and clean up any extra investment that splashed up. Don't forget to remove the masking tape as well before putting it in the kiln.
Then put it in the kiln, "button" side down and bake it so the wax melts out of the mold. Wax melts at around 1200 degrees. I usually do the kiln for a good 24 hours. That way it can get to temp and lower back down again before I use it.
Step 6: Casting Your Metal
Once your mold has went through the kiln, the next step is to cast your metal.
So remember the weight of it? Depending on which metal you are casting in, determines how much metal you use. I used silver. There is a different formula to figure out how much metal you use for each. With silver it is:
the weight of your wax + 15% X 11 + 3
Once you weigh your metal, you can then melt your metal to get ready to cast. Now there are different ways you can do this. You can use a torch and a crucible to melt it, but I used an electromelt. It will heat up to the correct temp you need for you metal and it also allows you to prep while it is heating up.
Before you put your metal into the crucible, make sure there are no particulates in it that can contaminate your metal. Take a graphite stick and lightly scrape the bottom and then lightly dump anything out of it. Put the crucible back into the electromelt and turn it on and set it to the temp you need. For silver I needed 1740 degrees. Put you metal in now so it can heat up as you prep.
Next you want to put on your heat gloves and take your tongs and flip your flask over so any toxic wax fumes come out. Let that stand in the kiln that way for about 10 minutes. That will give your metal a good amount of time to melt.
After about 15 minutes, use your welders glasses and check to see if your metal is liquid in the electromelt. Once it is, it is time to start.
Make sure your vacuum table is prepped and ready to go. Make sure there is a good vacuum and everything.
Get on your other heat gear. One thing I do is make sure you have latex gloves under your heat gloves so when you dunk your flask, you can then take your heat gloves off and you are ready to dig in water.
Once you are geared up, take the tongs and put your flask on the vacuum table. Turn it on and make sure it gets to full suction before going to pour your metal. Pour it in and wait about 10 seconds before turning off the vacuum.
Once you pour your metal in, wait until your "button" is a dark gray without any glowing left. Then take your tongs and dunk it in your big tub of water to get your metal out of it investment.
If it casts correctly, you should have something like what the second photo on the step looks like.
Step 7: Cleaning and Polishing
Now you're ready to start cleaning and polishing your rings.
First you will need to anneal the model and quench it about three times to get any excess investment off the metal. Once its all off, stick it in a pickle for about 10 minutes or so (longer if your pickle is cold). I like to sandblast after this, but I dont think its necessary if you aren't planning on using the metal from the button again.
Once you have your metal clean, you can then saw off the sprues. After that you will take your half round file and your needle files and start cleaning it up. You might need to file down where the pearl sets a little, or even resize the rings. There is some shrinkage that happens in the casting sometimes. They say up to 10% shrinkage can happen.
Then taking different grades of sand paper and smoothing out the surfaces. And then I use small polishing wheels to smooth it out more. Once I have that all done, I go over it with fabulustre polishing compound to make it all super shiny.
and ta da! You have wedding bands!
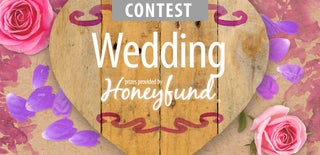
Second Prize in the
Wedding Contest 2016
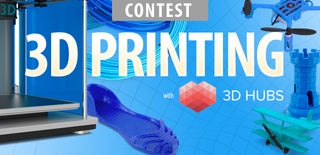
Runner Up in the
3D Printing Contest 2016
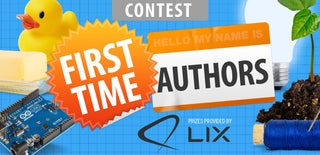
Participated in the
First Time Author Contest 2016