Introduction: De-nailer Deflector
I got a new tool!
It's a reverse nail gun, AKA "The Denailer." (affiliate link) Pinhead better skip my house this Halloween!
(Thanks @JackmanWorks for convincing me I needed it!)
I sort of-ish read the instructions (come on it's one page and it's a picture for makers sake!), oiled the tool, hooked it up to my compressor and KaThunk! We're in business, lets de-nail something stat!!!
Little voice in my head - Should we be wearing gloves for this adventure?!
Other voice in my head - No time, new shiny tool, must play with NOWWWWW!
My voice in my head - Should I be worried about all these voices?!?!?!
I thought I was being smart and put the board with the nail in it over a bucket, there's no way this thing is punching a twisted pallet nail completely out of an oak pallet board right?
Wrong.
It KuThunked the nail out of the board hard enough to ricochet off the bottom of the bucket past the board and into my ring finger. Not really super bad, but hard enough to make sure I noticed and break the skin enough for a bandaid. (Yes, yes, I know, this is why I can't have nice things, etc etc...)
Hmmm. maybe gloves would have been a good idea... do better at listening to the little voice next time, but right now we need to fix this cuz I wanna do some more denailing!
Enter - The build a tool so you can actually use your new tool without hurting yourself tool. AKA: We're gonna make a deflector that clamps onto the top of a 5 gallon bucket for the denailer!
Step 1: Tools and Materials
Tools and Materials
-Bucket of the 5 gallon variety.
- I got lucky and didn't have to run to the Depot's of Home, I found a bucket in the shed that didn't have stuff in it and was cleanish.
- (I am kinda partial to the Ol' orange Homer bucket though)
- ((Dude, wayyyy off tanget, get back to the tools and materials))
- (((I'll show you a tangent little voice...)))
- *Eherm, sorry about that... Back to the regularly scheduled programing now.
-4x 1" ish or longer #8 screws
-8x #8 washers
-4x #8 wingnuts
- (Nuts would also work, wingnuts just make it easy to remove and empty the bucket)
- Or CNC, Jigsaw, a coping saw, or possibly anything that cuts wood would work, use whatcha got!
- (Ha, wood would... like wood wood but not. Hey, it made me laugh! Wait, was that me or was it one the voices...)
*Note: My posts may contain affiliate links to products I use and feel comfortable sharing. Which means when you click the marked product links in my post nothing changes on your end, and I earn a small % on qualifying purchases. Thank you for your support!*
Step 2: Files
How'd you find the dimensions? AKA, is this going to work?
First I tried to be lazy and started by just googling the dimensions of a 5 gallon bucket. But that took me down a rabbit hole... I had no idea there was a debate about what specs a 5 gallon bucket was made to.
Anyhoo, I'm proud of myself (pat, pat) for not getting caught up in a bucket tanget and I got off my buttox and I measured a few different 5 gallon buckets. With a ruler. (FYI buckets do have a tangent point since they're round right? Right. Good. Motion carries, on with the show. Again) And I added about a 1/4" tangential rabbit hole factor. That will be plenty good enough for what we need today.
Are we done talking? Can we pleeeeaaaseee fire the laser now?!?! No, not yet... we still need to create the digital file. Go fire up Fusion 360 and I'll be there in a minute.
A few specifically sized rectangles, radiuses, holes and slotes later; here's the finished plan! You got three parts:
1. The top, yes you're right we need a fancier name. But you've already probably figured out that this is the part that goes on the top so I guess lets just stick with calling it that for now since we're both invested. It has a rectangle cutout for the nails to go through.
2. The spacers. You'll need 4 of them. I thought about glueing them on or adding an indexing tab, but really, they work fine as-is so I didn't overcomplicate the spacers (yet?!). When using 1/4" plywood, this clears the top lip on most 5 gallon buckets perfectly.
3. The slidey parts. Yep, you guessed it. These are the parts that slide to clamp onto the sides of the bucket under the lip on the rim. You need two of these.
The Fusion 360 model file is also included in case you want to tweak the model to fit your needs better.
Step 3: Assembly
Cut and assemble
Pew, pew pew! Yeah, I know, but come on laser burninating is never going to get old! I was able to use some cut off scraps, so my top is just a teeny bit undersized so that's why it doesn't quite look like the model in some spots. Other than that the files cut fine. I used 1/4" birch plywood, my GF laser cut settings were 140 speed, Full Power. I didn't mask anything, so you will see some smoke residue.
If you're anything like me, you're not reading this part and you're looking at the pictures to see how everything goes together. The spacers align with the holes on each corner, then the slidey bits go on and everything gets secured with the bolt, washer wingnut combo. But you already knew that didn't you ;-)
Once it's assembled, put it on the bucket, slide the slidey bits snug to the bucket and tighten down the wingnuts. Finger tight works fine and I like having the wingnuts on the top so it's easy to loosen them to dump the nails out of the bucket.
That's it. Time to make more KaThunks!
Step 4: KaThunk All the Things!
Done! KaThunk all the things!
It verks! The first time!! I didn't even have to "clearance" any of the holes!!! Am I finally getting better at working with me?!?!
So yeah, there we go. I've run through about 4 pallets worth of wood as of this Instructable and the deflector is doing it's job great! No more rouge ricocheting nails!
One thing to watch out for, I did have a couple "misfires" where the nail wasn't lined up with the opening and it hit the top deflector plate (hey, that's what we should call it instead of "The Top Part!"). The misfire made the pallet board jump a little and put a good dent in the deflector plate, but it's still totally functional. Plus if it ever does break we've got the template to easily cut another one!
Hey, look at me, I'm learning to not say that's all before it really is all at the end of my Instructables! Yeah, so if you read this far please do me a favor before you leave this caffeine and sugar fueled tirade and toss me a vote in the build a tool competition!
OK, that's all, thanks for playing!
_____
If you'd like to see what I'm up to when I'm not Instructable-ing you can also find me at these places:
My Website: https://www.makerneer.com/blog
Instagram: https://www.instagram.com/makerneer
Facebook: https://www.facebook.com/Makerneer/
Pintrest: https://www.pinterest.com/makerneer/
Note: This post contains affiliate links.
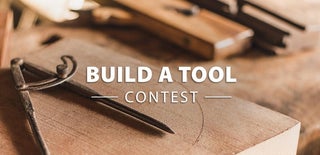
Participated in the
Build a Tool Contest