Introduction: Homemade Bandsaw by DIY Enthusiast
Hey, if you don’t know me, I am an all-around DIY enthusiast that makes all kinds of projects. But making DIY tools is something special for me. The process of figuring out how it should work, designing, building, and seeing them in action is what makes me love this so much.
So I designed and made my first 8-inch bandsaw with variable speed-control, soft-start function, 45-degree tiltable table, and adjustable dust collection port.
I am not a pro in fields like woodworking, electronics, or 3D printing, I just love making stuff. My goal of this instructable/video is to show step by step building process that combines those fields and that you don’t need to be a pro with a decked-out workshop to make projects like this. Hey, look at me… I only have my tiny work-corner, it is not even a workshop!
You can follow me:
- YouTube: https://www.youtube.com/diyperspective
- Instagram: https://www.instagram.com/diyperspective
You can support my work:
Provided links are affiliates.
Main Components & Materials:
- Blade for curves (1425x3x0.35mm 14TPI) https://s.click.aliexpress.com/e/_ACsfYi
or https://amzn.to/37r2uku - Straight cut blade (1425x6.35x0.35mm 10TPI) https://s.click.aliexpress.com/e/_AM7zy6 or https://amzn.to/2ZsDcOH
- Plywood (12mm thick) https://amzn.to/2R1IsVL
- MDF (18mm thick) https://amzn.to/3qJpWRf
- Wood glue https://amzn.to/2UvRrjX
- 30-minute epoxy https://amzn.to/365rq0d
- Polyurethane wood floor finish https://amzn.to/3p8AuJt
- Stainless steel shaft/rod (12mm diameter) https://amzn.to/395lXZm
- Bearings for wheels KFL001 https://amzn.to/3p7IdHG
- Bearings for guides 606ZZ https://amzn.to/361JKY0 or 6062RS https://amzn.to/361JKY0
- Hanger bolt (for tensioning part) https://amzn.to/2YaHt8x
- Threaded inserts (I used M6 and M4 size) https://amzn.to/3qGpFyu
- Clamping knobs https://amzn.to/3c8V3BT
- Slip joint hinges for the table https://amzn.to/3p8kNlv
- Aluminum U-channels https://amzn.to/39NEoRe
- Rubber feet https://amzn.to/3o93a3E
- 24V 250W DC motor https://amzn.to/3sOe6Hy
- Sprocket 25H 55T https://amzn.to/3paGQYv
- Roller Chain 25H 04C https://amzn.to/366Ssoa
- DC 6-60V PWM Controller w/soft-start https://amzn.to/39YOZJc
- 24V 350W PSU https://amzn.to/3bZpZUY
Main Tools:
- 3D printer https://amzn.to/3o7DGn6
- 12V drill https://amzn.to/2U5QQmL
- 20V drill https://amzn.to/2MY3GRt
- 90-degree adapter https://amzn.to/394eERz
- Drill press https://amzn.to/35f93nO
- Jigsaw https://amzn.to/2rg4uXx
- Router https://amzn.to/2DVXXZC
- Rotary tool https://amzn.to/2MWaP4H
- Chisel set https://amzn.to/2KCCquy
- Fretsaw https://amzn.to/33LcvVr
- Speed square https://amzn.to/2Ee6lDh
- Carpenter L square https://amzn.to/365L6RH
- Combination square https://amzn.to/2oLYnwv
- Clamps https://amzn.to/2YKWmRS
- Small clamps https://amzn.to/39CliLU
- Forstner bits https://amzn.to/3azsfOZ
- Cutting saw bits https://amzn.to/3iE30zS
Other Things:
- Bolts, nuts, washers, wood screws, electrical or grip tape, wires and connectors to power the motor.
Step 1: PREVIEW
Like I said before, this bandsaw has variable speed control + soft-start function, a tiltable table to a 45-degree angle with a very rigid clamping system, and a direct and adjustable dust collection port.
Are you ready?! You better be, it's a long one, haha!
Step 2:
This is quite a big project. Not because of the scale, but because of how many parts need to come together and fit perfectly as in the sketch. If you like me and never made something like this before I suggest taking it slow.
This isn’t a speed building contest, take your time and make every cut as precise as you can. This will eliminate all the fitting problems later that usually cause a lot of headaches.
I used high-quality Baltic birch plywood of 12mm (1/2 inch) thickness. I made the frame from two pieces, but before I cut out a slot for the motor.
Step 3:
I had to trim the spot further that I could properly fit the motor later.
Making all these cuts is just a breeze on the jigsaw table. One thing to note here is that I always use the orbital setting on the jigsaw. It makes the blade go forward and backward allowing for a faster cut, but then the blade cuts at an angle. So when I am near the end of the cut, I switch to the regular setting to get a straight end cut.
And to make a more complex inside cut, I drill a few holes alongside the edge with my made 90-degree drill guide. Then I connect them with a drill-and-saw bit or something like that.
To make the top cutout (where the tensioning mechanism & wheel will be) I am taking the easy route by drilling holes in the center of the cut lines. It is way faster to cut it like that. It doesn't look great, but hey who cares it won’t be visible anyway.
Step 4:
In the base, I made one 20mm hole for the 12mm thick bottom wheel shaft and one 35mm for the motor.
I had only 100mm length calibrated stainless steel shafts, so I had to make a slot for the bearing. This will make more sense later as there will be more parts at the back, which will increase the thickness.
Step 5:
I cut more parts for the frame and started gluing them. I can position them exactly how I need and later additionally secure them with wood screws.
It looks good, but I forgot to cut out that tiny part. Thankthufylly I still could do it the hard way.
The thicker the frame of a bandsaw the less flex it will be, so additional plywood piece like in the last picture won’t hurt.
Step 6:
Now it is time to attach the frame to the base, which I made from two glued plywood sheets.
I glued more pieces together to make the part that will reinforce the bottom wheel shaft and overall rigidity from the frame to the base.
And after the glue dried out, I additionally secured the frame to the base with big wood screws.
Step 7:
To make the wheels of the bandsaw I used an 18mm (~3/4inch) thick MDF sheet and routed 210mm(~8inch) diameter circles with four passes.
Making the hole for the rod on a wheel, in my experience, are quite tricky to do absolutely perfectly. Because even the slightest degree offset will be extremely amplified when it will spin.
In my experience, the easiest way is to drill or sand an existing hole that it would be slightly larger. This way you will be able to set it at a perfect angle later.
Step 8:
Make sure to countersink inside holes and roughen the rod for better bonding.
I used a cold-weld bonding compound, it has an extremely high and bad odor, but it great for this job. I used it when making my sander and it holds without any problems to this day.
With larger holes, you now can adjust it to the perfect angle as shown in the photos.
The next, day I added more of the compound around the rods, as I couldn't add it before.
Step 9:
To power the bandsaw I used a sprocket and chain system with the 24V 250W DC motor. I went this way because I already had the motor and it had the mounted sprocket, but more about this later.
Now, to mount the sprocket perfectly in the center would be very difficult on the first try. But if you have a 3D printer, you can quickly make a basic centering ring. And now it is perfectly in the middle. Uses like these make me so satisfied that I finally enterer into 3D printing. WORTH IT! :)
To make the holes I used a smaller chuck as the regular one is too wide… And to secure the sprocket - a few bolts washers and nuts.
Step 10:
Do we make the wheels with a groove for the blade or with a crown? It seems that the groove is the right answer. The blade will be in that groove and won’t fall off, right? But actually, the right answer is the crown. But wouldn’t the blade just fall off to the lower point?
Well, no. To keep it short, the blade will ride on the highest point on a wheel. There is a written article and demonstration by the one and only Matthias Wandel, who made a lot of great bandsaws.
So to make some crowns on the wheels I quickly assembled a jig. For now, to power the motor I used my made variable voltage power supply as my speed controller didn’t arrive in time.
First I trimmed the wheel that the balance of it would more decent, with less wobble it will be fewer vibrations, which is always better.
I shaped the wheels that they would have a crown inside and outside wall to protect the blade from slipping off the wheel. This is a DIY project after all, so extra safety won’t hurt, that’s my thinking.
But maybe there is a catch somewhere because commercially made bandsaws have just a crown and I didn’t find any information about the reasoning for it. Probably the main reason is that it will be able to run wider blades, that’s my best guess.
To protect the MDF wheels I used polyurethane based wood floor varnish. It creates a hard and durable coat of protection. And it is very satisfying to see how the color changes after the first coat. I did 3 coats in total.
Step 11:
With the wheels done, I secured the front bearing with two big wood screws and routed a slot for the back bearing. Again this is because I had short shafts for the wheels.
Using two spacing blocks of plywood I secured the bearing that the wheel would be parallel to the frame.
Step 12:
At this point I noticed that one of the wheels was heavy on a side. Usually, MDF is a very even density material and this is a non-issue. Well, whatever. It is easily fixable by taking away some of that weight.
Step 13:
Using combination squares I marked and made holes for the bolts. It’s a good idea to make larger holes for adjustability for optimal chain tension. That means bolts won’t be flush to the bottom. But four rubber feet solves that problem and also gives more grip, and reduces vibration transfer.
Step 14:
It is time to make a top wheel tensioning mechanism. This will be a very simple and effective system, not really much to say here.
Step 15:
At the top of the wheel-tensioning part, I made a hole for this unusual bolt. You can see that I use my made drill guide a lot, well because you can make straight holes almost everywhere, I love it!
Step 16:
To align the top wheel perpendicular to the base I glued a temporary sheet of plywood and used a few squares and a ruler. Just don’t forget to sand the parts first that they would slide smoothly.
Before mounting the blade I added two layers of electrical tape that the blade wouldn’t slip. And to finally see for the first time that the blade perfectly tracks in the middle is an extremely exciting and relieving moment.
And if it is not tracking properly, you can change the angle of the wheels by slightly repositioning the back bearings. The blade should right in the middle and be perpendicular to the base, there is some wiggle room so you can easily do that.
So far the tracking of the blade looks great. No matter how
much I tension the blade it stays mostly around the middle. That indicates that the frame is rigid and has very little flex.
The reason I ditched the top wheel angle adjustment that all of the commercial bandsaws have is that intend to use this bandsaw only with few types of blades. So once I adjust the tracking for them I won’t need to change it anymore. I am too lazy to change blades anyways, so why overcomplicate things, right? And if someday I magically need that I can modify it very easily as everything is secured with screws.
It is important to not forget to make grooves for the back bearing screws. It is easily accessible and it is easy to line up to the made spots. Meanwhile the front ones, I just firmly tighten as there is very little space.
Step 17:
At the top, I carved away some of the plywood for the 3D printed knob. Then roughened an M10 nut, heated it, and fused it into the knob. Easy peasy!
Step 18:
Well, we need a few blade guides. So I designed and 3D printed the guides. It uses M6 hex head bolts. I attached the bottom one for now as there is more work till I get to the top one.
Guides have an infill ratio of 100%, which means that inside of the object is fully filled with plastic. That makes this part very rigid. And as it is also made from PETG filament is very hard to break, really really hard to break.
Step 19:
To make the base, I cut more parts. I routed grooves on the bottom and the top part of the table, that hinges would sit perfectly inside. To temporarily secure the hinges on the top part of the table I used some double side tape. And to drill pilot holes perfectly in the middle of the hole I used self-centering drill bits.
The motion feels excellent – no unnecessary play at all and very smooth.
Step 20:
But now is the part that annoyed me the most – making the insert hole. Setting up this was a nightmare, I really need to make a jig for this kinda work… As the table is from two parts, I first made the top slot as accurate as I could and then the bottom one, which doesn't really need to be super accurate, but needs to be bigger.
Step 21:
With few passes, I routed a groove for the aluminum profile and cut an opening for placing the bandsaw blade.
The aluminum profile can be secured with several small screws and the end of the profile cut off.
Like the wheels, I coated the top of the table with a polyurethane-based wood floor finish. Also at this point, you can glue the table as we won't need to disassemble it again.
Step 22:
To secure the table to the frame, I needed to make additional supports. I glued parts and additionally secured them with screws.
Step 23:
Then I made a part with threaded inserts that will hold the blade cover. First I clamped the piece between scrap ones that I could get the perfect angle with my drill guide and that the threaded insert wouldn't split the plywood.
I glued the part to the frame and printed tiny holders that will hold a U type aluminum profile. You might say this doesn't seem very convenient. Yes, it could be better but you only need to undo the top screw and you can take it away. And like I said before I am not looking for often blade change.
Step 24:
Next, the table securing to the frame. I didn’t want to permanently attach it to the base (later you will see why), so I used M6 threaded inserts. To do that you will need some sort of angled extension and short drill bit as there is no room for anything else, well at least in my case as this is a pretty small bandsaw, 100mm or 4inch resaw capacity.
As these threads must be strong, I additionally glued them with 30-minute epoxy.
Step 25:
To know where to make holes on the bottom table part, you can place a template and punch holes and then transfer them to the part. And like before we should make wider holes for adjustment purposes. But those M6 hex head bolts with washers must be flush with the surface as the top of the table will rest here.
Step 26:
This already feels and looks great! But we need somehow to fix the table at a certain angle. To do that, I edited and printed the template from my 3D model. I used those drill and saw bits to connect the drilled holes. Never again... That took way too long and I also needed to sand it. Well, at least I know that a router is a way to go in the future.
Step 27:
To attach the angle lock part to the table - again threaded inserts. I didn't have just a tiny bit shorter bolts, so I added multiple washers, or you can cut off the end, the choice is YOURS.
Of course, something must always go wrong. I guess I messed up the template and the slot was too short, so I had to fix that.
Step 28:
To lock it in place, I made a hole for a bolt and a slot for a nut that it would sit flush. To clamp it in place – washer and a knob. This is a very basic system but it holds the table very firmly in place.
Step 29:
I started making the top blade guide system and routed a 6mm slot for the M6 bolt.
Step 30:
I glued two pieces for the long sliding part and those usually don’t have that smooth and flush edge. So what I did, I taped the part to a straight edge plywood piece. One slow pass on a router and the part is perfectly flush. I do all my cuts on a jigsaw, it is precise but here I need absolute perfection. That's why I am routing both pieces and not only one with a flush-trim bit with a bearing.
You can easily drill perfectly centered holes with shorter bits by lifting the drill press table with an existing drill bit, realigning the fence, and changing to a short drill bit.
I used M6 flat head screw and nut on another side of the part.
Step 31:
Before gluing the last pieces, I sanded the surfaces on which the long part of the guide will slide.
On the long sliding part, I glued tiny plywood blocks that will hold the 3D printed blade guide.
Step 32:
Now what’s left is to drill few holes and secure the guide to the frame. By using bolts you can adjust how much the sliding part is clamped down. Too much and it won’t slide and too little it - will be loose, luckily we used bolts right?
Step 33:
To finish the frame I glued the final pieces that will hold the custom 3D printed dust collecting port. Like before, these small blocks are for a big screw.
Talking about the port… I don’t have a clear idea of what happened but the top slightly shifted during the print. My best guess is that the print bed caught on a loose cable or print head just slammed into the print and caused this layer shift. If it is the slamming then I could increase the lift of the nozzle when traveling (Z hop height on Cura).
However, the great thing to take from this is that the part is still usable, it only doesn’t look great. But hey, I would take that every day of the week instead of reprinting it for 8 hours.
Step 34:
As I used a DC motor it needs a power supply, it will fit neatly at the back. But I don’t want to just leave it like that with all contacts exposed, so I started making a cover. Making those complex and straight cuts on the jigsaw table is great.
Meanwhile making air passthrough port for the power supply was so tedious... Also, I am always too lazy to change to the higher speed on my drill press. That usually contributes to that chipped plywood, as bit just rips the top layer on low RPM.
With all three pieces glued, I can finally attach the cover. Like before I used threaded inserts that were additionally glued with epoxy.
I needed to attach the power supply somewhere. It has threads for the bolts, so I just had to transfer the hole spacing on the plywood.
Watching this now, it makes absolutely no sense to attach the power supply to the cover. As you will later need to route the cables on the frame. Real genius move right there.
Step 35:
Next, I need to make the door. No matter what numbers are in the sketch, you should always measure the dimensions of the already made object for the most accurate fit.
For the door to be flush with the frame I needed to route slots for the hinges.
When I secured them, I clamped the door that I could easily mark where the holes need to be.
I secured the hinges to the frame with the bolts. This will let me easily adjust the door to the ideal height.
Step 36:
I jigsawed holes for the On/Off switch and the speed controller. I needed to disassemble the controller to make it fit. Also when mounted you cant access the terminals as screws are facing away. It’s quite a ridiculous design flaw.
I also glued a strip of plywood to reinforce the door.
Step 37:
For locking the doors, I used one latch at the top and one at the bottom. Make sure that they clamp the door as hard as possible to a sensible degree.
Step 38:
Now let's finally move to electronics and how to connect everything. This is pretty much the basics of electronics, but it involves wiring AC 120-240V. So if you have no idea what you are doing, STOP, user mistakes can lead to a fatal injury.
So, first, we need AC power. Live and Neutral wires go to the magnetic switch where IN is written and ground wire goes directly to the power supply.
AC power wires from the OUT connectors of the switch goes to the power supply where Live and Neutral is written. 24V DC Output wires from the power supply go to the speed controller where POWER is written. And finally, wires from the DC motor goes to the controller where MOTOR is written.
One important thing here is that you should first power the controller without the motor. This is because first, you should set up the soft-start function. It will make a motor spin up gradually, removing all the tension that the bandsaw receives during start-up.
To adjust it, you just press the menu button once and change the value. You can set the spin-up time from 0, which is 0 seconds to 100 which is 10 seconds. In my case, I set it to 20 which is 2 seconds. And if you want to customize it further there are 4 more options to do that.
I made the hole and grouped all wires with cable sleeves. Some of them get too close to the blade for my liking, so I glued a piece of plywood to separate it.
To secure the AC wire I printed a tiny holder. This will make sure that it wouldn’t be possible to accidentally pull out the cable.
Step 39:
To finish the top of the table I printed the insert for the 90-degree cuts. Sometimes you need to print it several times to make it fit perfectly. But when you nail the size, you can very quickly print different variants of it on a first try.
The reason that I need different inserts is that I used hinges and not trunnions. And you might say what a hell are those? To say it as short and as simple, trunnions makes that the pivot point would be right at the tabletop where the blade is. That eliminates the need for different inserts.
But the reason I didn’t use trunnions is that this is a small bandsaw and they would be too small and not rigid enough when making from plywood. Not to mention harder to make. I don’t really mind changing the inserts, it is easy to do and I can have all kinds of them.
Step 40:
Now not much left to finish the build. I only needed to make the fence. I made it from four pieces of plywood.
The reason I am attaching the fence to the sliding part with the bolts instead of gluing is that I would be able to adjust or change the part if needed. I used M5 bolts here.
Step 41:
The fence will slide in this part. It is basically an aluminum profile (the same that I used to make the blade cover) on a strip of plywood. To attach it I made more inserts in the table and secured them with M6 bolts.
Step 42:
This fence clamping system is very basic and clamps very firmly. One part clamps it from the front and one at the back. It is probably not convenient for bigger bandsaws as you also need to reach and tighten it at the back. But, hey, I will always take the practically unmovable fence even if it needs more time to set it up. In my opinion, it is a non-issue on a small bandsaw.
Step 43: END of the Build / Important Info
Well, and with this step, the build is complete! Now it is time to talk about the results, adjustments, and additional important information.
I know that everyone wants to see cutting results at first, but even when you buy a bandsaw the first thing you should do is to make some calibration if necessary, before judging the accuracy of the tool.
What I am talking about is the blade drift, it happens when a bandsaw is not properly aligned. The blade should be parallel to the fence to get an even cut at both ends of the workpiece. But remember that the fence should also be parallel to the miter slot or it practically loses its point.
So to eliminate the blade drift, first, you need to make sure that the blade runs in the middle of the wheel when tightened. If you still get the drift, then you need to rotate the table itself. I had to slightly shift it from the designed 90-degree angle.
I will be using this bandsaw only with two types of blades. One for the straight cuts and one for the curved. So when I adjust the straight cut blade, I am all set. Because narrow blades lack precision on straight cuts anyway.
Step 44: Blades / Frame Flex
The obvious thing to note is that the blades of a bandsaw are flexible and not rigid like on a saw or even on some bigger blades on a jigsaw. This makes the bandsaw not really a precision tool as the blade can slightly wander from side to side. Of course, you can reduce that with wider blades if you need the most precision at straight cuts.
But then account that wider blades can stress the frame more. I made mine only from 2 sheets of plywood with covering parts that give more rigidity. In my case, it has very little flex, only 0.3mm when the blade is tensioned, but I am using relatively narrow blades (6.35mm). So just be aware of that.
Step 45: Bandsaw Vs Jigsaw Curved Cuts
I made it mostly for curved cuts on smaller pieces. As making them on a jigsaw table is the jankiest s**t ever… Compared that to the butter smooth cuts on a bandsaw… There is absolutely no competition.
Step 46: Cutting With My Bandsaw
Overall, I am happy with the accuracy of the tool. You can get very accurate cuts on smaller pieces.
Resawing is definitely not the main reason I needed the bandsaw, as I don't even have a blade with lower TPI and bigger gullets. But hey, it is nice to know that even a 3mm (1/8inch) blade can do a not terrible job at it.
Step 47: Why DC Motor?
Next, let's talk about probably a little bit unusual decision – going with the sprocket-chain system and a DC motor. From what I saw, everyone that has made a video on building a bandsaw went with some sort of pulley system and an AC motor.
But there were a lot of reasons why I went my way. First, sure, because I already had a compatible DC motor for the build. A more serious deciding factor was that they are more efficient than AC motors. This one packs more than enough power for this little bandsaw and is quite compact.
Also, it is easy to precisely control DC motor speed with inexpensive PWM controllers. This one even has a very important soft-start function. It eliminates the huge inrush current when a motor is powered, extends its lifetime, and removes all stresses on the assembly on startup.
Step 48: Why Chain+sprockets?
I went with the sprocket-chain system because the motor already had a small sprocket and I needed fewer parts this way. The only concern I had – huge sawdust accumulation on the chain. But after a week of using the bandsaw chain seems perfectly clean. This means that the dust collector does an excellent job.
But the biggest downside of the chain is the noise. This is expected as it is metal on metal action at 3000RPM. However, I don’t really care as I always use a shop vac which is already louder, and wear hearing protection anyway.
Step 49: Calculate Speeds
To calculate the optimal ratios of sprockets I used this website, it gives you a lot of details.
Using the same website you can easily calculate the speed of the blade on the bandsaw, again a lot of details here and it has metric and imperial systems.
Step 50: Improvement
The wiring in the doors overcomplicates things. I just needed to make the separate top and bottom doors and secured the middle part with screws.
Step 51: Power
I used a 350W power supply which later I find out is overkill. As power never peaks that high even when cutting 10cm/4inch height plywood piece. In my case, I could use it like 250-300W PSU. But remember that a lower TPI blade can increase the power consumption when resawing. So in this case 300W PSU is the minimum (for 250W motor), as you should have some gap to not overload it.
Step 52: Table Alignments
I specifically left a tiny gap between the base and the top of the table, that I could glue multiple layers of painter's tape and easily get that perfect 90-degree angle alignment.
Step 53: The Price / Conclusion
With all that said, I finally should say how much it cost me to make it. If you are living in America, the cheapest bandsaw price can go as low as 135 bucks. In Europe prices usually are higher, but you still can find some cheap stuff for 150 bucks.
I listed all my used parts and I got the final price of 151 dollars, yeah. I could use a cheaper power supply I guess, but still, it is so close to the commercial price.
So then, it is not worth making it, right? Well, it is not that simple. You see, I own a few of those cheapest tools and I absolutely hate them. They are inconvenient, not very accurate, and definitely not satisfying to use.
It might sound silly, but I think that psychological effects play a lot here. After buying such cheap tools you often feel the buyer's remorse which, to be honest – really sucks. Meanwhile, after making something yourself that works great, has more functions and improvements, you end up with a lot of positive emotions. So if you think you can, sure go for it and make it, you will love the feeling when you finally build it. You will be able to easily mod and with time improve it even further.
But if you don’t want to make it, my suggestion is to avoid those cheap ones. I already learned my lesson. And like someone said, “I'm not rich enough to buy cheap things”. So, I rather make my own or buy something decent that I wouldn't need to regret my purchase decision in the long run.
Step 54: Support Creator With Patreon
If you liked the instructable and you want to support my work you can become a patron. There, you will find the 3D model of this bandsaw, post-project updates, and extra DIY stuff. And if not, that’s perfectly fine, something very simple even like giving a heart on instructable always helps.
Feel free to leave any questions about this build. Thank you, for reading! Till next time! :)
You can follow me:
- YouTube: https://www.youtube.com/diyperspective
- Instagram: https://www.instagram.com/diyperspective
You can support my work:
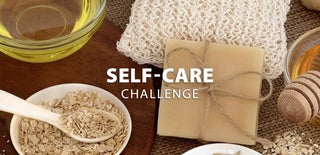
Participated in the
Self-Care Challenge