Introduction: Light-Sensitive Geometric Animal Sculpture
I wanted to make something that would automatically get brighter as it got darker outside and had been planning to do something with brass wire for a while. After some deliberation, I decided to make a Taurus sculpture with embedded LEDs.
Supplies
Tools:
- needle nose pliers
- side cutters
- soldering iron
Material:
- 1mm brass rod/wire ~4m
- SMD LEDs 1206 or smaller if you want
- solder
- some high awg wire
- photoresistor
- resistor 10k Ω + 1k Ω
- transistor (2n2222a / bc54)
Optional supplies:
- 3D printer
- regular printer
- drill
- colophony
- ceramic tweezers
- double sided tape
- multimeter
Step 1: Choose Your Design
We need a template to create the wire structure. I decided to make a bull's head and design it in Fusion360. How exactly you can create your own design in Fusion360 is explained in the next step.
If you prefer to build this project, the finished STL file is also linked here.
Attachments
Step 2: Turn Your Design Into a Template (3h)
First you'll need to decide whether you want to print your design using paper as a template, or create it in a CAD programme to get a 3D printable STL file.
regular printer: If you want to use a paper template, just print out your drawing. Later you'll be able to use double-sided tape to hold the LEDs and brass wires in place.
3D printer: I prefer this method because it provides a more secure frame for the LEDs and wire. It also doesn't leave residue on the brass like the double-sided tape would.
I've just started using Fusion360 and found myself googling a bit to understand what I need to do. Since it is relatively easy to create a flat 3D model and the software is free, I decided to give you a full rundown of what I did. I'm sure you'll be able to follow along even if you've never used Fusion360 before.
- Open Fuison 360 and create a new sketch
- Start by placing a long vertical construction line (click on the first icon behind "Linetype"). This line will be our mirror line. Deactivate the construction line type.
- Add more normal lines on either side until you are happy with your design.
- Select all the lines except the horizontal line and choose "mirror" from the "create" tab. In the new window that opens, click on "Mirror Line" and then on the line you placed in step 2.
- Open the "Solid" tab and select "Extrude". In the window that opens, click on "Thin Extrusion", uncheck " Chaining" and click on each line individually. Once this is done, set "Distance" to 5mm, "Wall Thickness" to 4mm and "Wall Location" to Centre.
- Open the "Sketches" folder on the left and double click "Sketch1". Repeat step 5 but set Distance to 1mm, Wall Thickness to 1.8mm, Wall Location to Centre and Operation to Cut.
- Lastly, click on File, Export and select STL from the drop down menu.
You will notice that the design linked above has small holes in it. I put them there to make it easier to remove the wire at the end, but I didn't use them. So I have decided to leave them out of the description.
Finally, print out your finished template. We will use the free time for the next step:
Step 3: Plan Out LED Location (20min)
We need the LEDs to separate the positive wire from the negative wire. It takes a bit of thinking, but for most designs there are a lot of possibilities, so everyone can find something they like.
Simply open your design in Paint and draw some coloured lines + dots for the LEDs until you are happy with the amount and location.
Step 4: Start the Soldering(3h)
First of all, a few tips in advance:
- Colophony makes soldering the brass rods much easier. Simply dissolve it in a little alcohol (e.g. isopropanol) and apply it to the ends.
- If your brass wire is not straight, you can clamp one end in a cordless screwdriver and hold the other with pliers. Let the screwdriver turn until the wire becomes a rod.
- The wire gets quite hot when soldering - ceramic tweezers are helpful here, but a cloth can also be used to hold it in place if necessary.
Next we can finally start with the actual construction.
Take the copper wire and cut it to the required length for a straight rod and place it on the template. Continue in this way until you reach the first LED. First we solder the previous brass rods, then we put the LED on the template and solder it. Don't forget the colophony here either. I found it helpful to have the previously made plan of the positive and negative sections open so that I don't solder the LEDs the wrong way round (long side of the triangle is positive, the tip ground).
Once all the LEDs and wires are in place, we can remove the template.
The 3D printed template might have a few wires fused into the plastic, but this is not a problem. If the construction does not lift out easily in some places, do not try to force it, but heat the plastic with a lighter. Then you can simply bend it over.
The paper template with double-sided tape is a little more difficult. The wire can be removed easily, but the adhesive residue is hard to remove completely. I think nothing helps here but isopropanol and patience.
Before you apply any current to the wire, it is a good idea to check the continuity with a multimeter.
Step 5: Building the Base With Sensors (40min)
brighter in darkness:
Here we build the base that holds the rest and has the electronics built in. For this we need the transistor, the two resistors (1k & 10k), a photoresistor and the high awg wire. The bc54 and 2n2222 transistors are quite common and cheap to get. I used a 2n2222a transistor, if you have another one, compare the pin-out to connect it correctly. However, if you also have a 2n2222 transistor, you can rebuild everything as shown in the picture (the semicircular side facing up).
The sensitivity can be changed with the second resistor. The higher the resistance (e.g. 22k Ω) the darker the LEDs for a given light level and the lower the resistance (e.g. 5.6k Ω) the brighter the LEDs for a given light level. I liked a value of 10k Ω because the LEDs are off during the day and slowly start to light up at dusk.
When you have finished the bracket, you still need to connect the power cables. The positive wire goes to the upper left corner (picture 3), the ground wire between the transistor and the photoresistor (picture 4).
brighter in brightness:
Leave out everything shown in picture 4 except the photoresistor. The photoresistor must be placed between the power wire and the brass rod.
Important:
With the resistors I used and the number and colour of the LEDs, I had no problem putting 5V directly onto the brass. If you have not used exactly the same materials, you should start with the recommended number of volts for the LEDs. This way you are always on the safe side and can slowly increase the voltage until your multimeter shows the highest voltage your LEDs are rated for.
A few standard values for LEDs are:
- red: ~2.2V, 20mA
- yellow: ~2.2V, 20mA
- green: ~ 3.0V, 20mA
- blue: ~ 3.2V, 20mA
- white: ~ 3.2V, 20mA
Step 6: Connecting the Frame With the Base (10min)
Now we connect the base to the actual wire sculpture. The right rod will be our positive pole and the left one our ground, which also means that they will have to be attached in different places.
The lowest LED in the horns is a good place. The left rod is placed above the LED and the right one below it. To make sure that everything will be straight later on, we will leave the left rod a few millimetres longer.
I also added a rod in the middle, which gives the whole frame a lot more strength.
Finally, you only have to solder the 3 rods to the base, as shown in picture 4, and check everything for continuity one last time.
Step 7: You Are Done!
Enjoy your very own, handmade, light-sensitive wire sculpture!
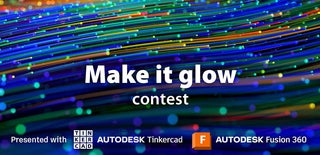
Runner Up in the
Make it Glow Contest