Introduction: Making Custom GFuel Stands - Craft Fair Idea
I've been wanting to make a dedicated wooden stand for my GFuel for a while now. The jig really made the process a breeze! I made one for myself, one for Keemstar and one for Faze Banks.
Supplies
Materials Used:
- White Oak, American Black Walnut & Padaulk
- Perspex (for the jig) but you can use MDF or Plywood too
- Screws (for the jig)
- Rubber Feet
- Gloss Spray Lacquer
Tools Used:
- Router
- Straight Cutting Bearing Guided Router Bit - T8024B
- Chamfer Bearing Guided Router Bit
- Drill
- Screw Driver
- Bandsaw
- Belt Sander
- Orbital Sander
- Laser Engraver (for the decorative parts and for creating the jig I made) not essential
Step 1: The Jig/Template
The biggest take away from this project should be how useful jigs and templates are! The jig I use for this project was made from perspex cut on my laser cutter. It is essentially a rectangle, with rounded corner and 2 circles cut out of the middle. This can be replicated using MDF or Plywood cut and shaped by hand to the rectangle shape. Then using a hole saw and a drill, the circles can be cut out. Using a bearing guided router to follow the shape gives the same results. Give it a try.
Step 2: Mount the Jig
I decided to make 3 stands at the same time. I used White Oak, American Black Walnut and Padaulk.
To start the project I placed the jig on the board and positioned it to make the most of the material I had. Placing it close to one corner will help reduce waste.
I could then mark the screw holes with a pen. Drill pilot holes for screws and secure the jig to the board with 2 small wood screws. The area these screw go into will be cut away later so the holes wont be an issue.
With the jig secure, I could then move on to using the router to carve away material.
Step 3: Remove Material Inside the Circles
The bit I used is a straight cutting bit that has a bearing. This bearing will follow the jig to create the exact cut I want. I used it in the router to remove material inside the circles and around the outside edge.
I first used the bearing to ride along the edge of the circles, cleared away the chips and then used the same router bit to remove the bulk material inside the circles.
The bit produces a really nice clean cut. The edges are perfect as the bit follows the jig. No steady hand needed. I cut down roughly 4mm deep.
Step 4: Router Around the Outside Edge of the Jig
The same bit can be used to follow the outside edge of the jig too. The bearing rides along the outside edge and gives an outline to follow later. The cut is perfect as it follows the jig. Cutting the outside edge like this makes sure its precise and exactly the size you want.
The jig is removed at this point. The nubs protruding at both sides with the screw holes in will be cut away.
Step 5: Cut Away the Bulk of the Waste Material
To make things easier on the router, I took the boards to the bandsaw and cut away the bulk of the waste material. I could really close the edge but made sure not to touch the edge with the blade.
The nubs on both sides were cut away too. I just made sure I didn't cut too much material away, these will be flattened late.
Step 6: Flush the Edges With the Router & Belt Sander
With the bulk waste material cut away, it was back to the bearing guided router but to now follow the edge of the wood. Its following the cut edge it made when it followed the jig.
I took multiple passes with the bearing guided bit. Lowering it a little with each pass until I made it all the way to the bottom of the board. This process would go a lot quick with a longer bearing guided bit.
I then took the boards to the belt sander to removed the remnants of the nubs on the side. I made sure they were all sanded flat.
To neaten up the underside of the boards I used another bearing guided bit. This time a chamfer bit. This bit cuts a 45 degree angle. The bearing follows the outside edge of the boards. I only added a chamfer to the bottom of the boards at this point. I will add the chamfer to the tops later. First, I want to add some decorative logos.
Step 7: Engrave Logos
I engraved some logos at my laser engrave. I engraved Keemstars Logo, Faze Banks' Logo and the GFuel Logo. I then sanded them to remove any burn marks.
Step 8: Apply Finish
The boards then got the same chamfer added to the top as they did to the bottom. After sanding by hand to get the smooth I applied 3 coats of gloss spray lacquer. Sanding between each coat. The last thing to do to this project is to add some self adhesive rubber feet and they're done!
Step 9: DONE!
I really hope this project has given you some inspiration. I think these can be adapted for lots of uses. Jigs can be really useful and help a lot to speed up making multiple items.
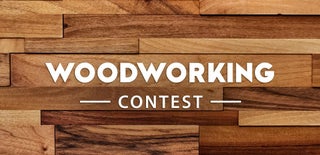
Participated in the
Woodworking Contest