Introduction: Making the ULTIMATE Drill Guide With CNC Parts
Hey, today I will be building this – the ultimate drill guide for making 90-degree holes. A lot of parts here are used in CNC machines. Will that make this the most accurate DIY drill guide ever?! Well, stick around till the end as I will show the results and also give my honest opinion if the tool like this is worth making.
I started this project in October of 2019. The first version of it didn't make me confident in the project, as it was flimsy and I understood that I had unrealistic expectations. So I left it to 'hang on'.
But later this year I felt like I really should finish what I started, as the tool like this is very useful when a drill press is not an option. So I reworked the design of the project and version 2 of it finally came out perfect without any flaws as I wanted!
Dimensions of the guide - https://bit.ly/DrillGuideDimensions
Provided Amazon links are affiliates.
Main Tools:
- 12V drill https://amzn.to/2U5QQmL
- 20V drill https://amzn.to/2MY3GRt
- Drill press (optional) https://amzn.to/35f93nO
- Jigsaw https://amzn.to/2rg4uXx
- Router https://amzn.to/2DVXXZC
- Combination square https://amzn.to/2oLYnwv
- Clamps https://amzn.to/2YKWmRS
- Small clamps https://amzn.to/39CliLU
- Spade bits https://amzn.to/2QZIEEX or
- Forstner bits https://amzn.to/3azsfOZ
Final Components & Materials:
- Plywood https://amzn.to/2R1IsVL
- Wood glue https://amzn.to/2UvRrjX
- 4x linear CNC bearings LMF12UU https://amzn.to/3duhO0Z (or you can use 2x LMF12LUU https://amzn.to/3duhO0Z Number in LMF12LUU means it is for 12mm shaft. If it is LMF10LUU it is for 10mm shaft)
- 2x linear CNC shafts 12mm https://amzn.to/3ey8kl9
- 2x 12mm linear shaft holder https://amzn.to/2ZS7pYI
- 1x 150mm x 10mm linear CNC shaft https://amzn.to/3cjF9kp
- 2x flange bearing KFL000 10mm https://amzn.to/2ZNC5KR
- 1x B12 mount drill chuck https://amzn.to/2yRFMnK
- 1x 10mm shaft coupler for B12 Drill Chuck https://amzn.to/36K60Vv
- 2x 12mm stop-rings / stop-collars https://amzn.to/2XQ5WzM
- 1x compression spring 1x15x305mm https://amzn.to/2Ak18un
Other Things:
Wood screws, bearing grease
You can follow me:
- YouTube: https://www.youtube.com/diyperspective
- Instagram: https://www.instagram.com/diyperspective
Step 1: PREVIEW
Preview of the drill guide.
Like what I do? Consider becoming a PATRON! This is a great way to support my work and get extra benefits! https://www.patreon.com/DIYPerspective
Step 2: Parts of Drill Guide V1
I started first version of the project with main parts like a B12 drill chuck, the coupler for it, a 10mm thickness calibrated rod that will go through two bearings, and will be connected to the coupler. For friction-free sliding two linear CNC bearings and two 300mm long and 12mm thick rods, two holders, and two stop-rings.
Step 3:
I cut the piece of Baltic birch plywood for the sliding part. Then marked and drilled holes for the bearings to fit. All holes in this project can be drilled with a hand drill, no drill press needed. But then you need to drill larger holes to accommodate for inaccuracy.
Step 4:
To get a nicer look and feel I marked and rounded the corners on my previously made 2in1 disc and drum sander. For the base, I used plywood of 12mm thickness. Cutting nice circles is pretty easy with a router. Of course, you can cut it with a jigsaw or even leave it as a square base.
Step 5:
With a small drill bit placed and squared to the base, I aligned that it will be in the middle of the rod’s hole and 'marked' starting points with the same size spade drill bit (just to see where the middle of the holes are).
Of course, I first tested on a scrap piece on how to make holes for the rods. The idea here is to drill with a step-bit from both sides a slightly smaller hole that the rod is. It doesn’t need to be perfect 90-degree, it just needs to be a tight fit, as the rod holders will fix the angle later.
Step 6:
In the middle of the base I made a hole for all kinds of drill bits. The size of it depends on the biggest bit you will use, but the bigger the hole the more flex the base will have and will be harder to use on thin boards.To get a nicer look I beveled the edges of the hole.
Then I aligned the rods, marked and drilled the holes, and secured the holders with pan head screws. Using this type of screws, you still will be able to slightly shift the holder in needed direction to get the rod in the perpendicular position to the base.
Step 7:
The next part is important if you want to avoid headache when aligning the linear bearings to the sliding part. What I did here, I placed the bearings on the end of the shafts, and with the sliding part in the middle, I removed everything while holding firmly in place. Now it is easy to mark the spots for the pilot holes and secure the bearings to the plywood part.
Step 8:
Finally, I secured the two bearings for the shaft, these will be aligned later. With chuck teeth inwards, I secured the coupler by a few taps with a wooden hammer. I also made two grooves for the fix-screws of the coupler.
Step 9: 3 PROBLEMS
With proper alignment, it looked really good. Perfect 90-degree angles in all directions. BUT three major problems bothered me.
The first problem was that long shafts had too much flex at the point where they are secured to the base. What I did, I cut and glued four parts that will greatly extend the rod holding point. This worked great – no more flex at the base.
Step 10:
The second problem was that the bearings weren’t the greatest quality and were too close to each other. This affected that the shaft had a small play. The longer the bit, the more amplified that play will be. So, to reduce it, I had to use a longer 150mm rod and increase the distance between bearings as much as I can.
Step 11:
What I did, I just glued some 12mm thickness plywood blocks. And that reduced the play a lot, to the point that I was really satisfied with it.
Step 12:
The third and the last problem was that the CNC linear bearing still had some play on the shaft. But with two – there was no play at all. So, it was the easiest fix of them all, just add more bearings on the top.
Step 13:
At this point, there is no way the drill guide will be at a perfect 90-degree angle. If you secured the two main rods at the perpendicular angle to the base you will only need to adjust the shaft of the chuck.
The easiest way is:
- To clamp the sliding part.
- Clamp a small combination square to the base at the bottom to properly align in one direction.
- With other square align in another direction.
- Secure the screws.
And now it has a perfect angle!
Step 14:
What’s left is to add springs that the guide doesn’t come crashing down. I used the 1x15x305mm compression spring and cut it in half.
The important thing here is that you shouldn’t place the spring directly on the plastic of the bearings. What I did here, I drilled a 12mm hole in the M10 washer. It now rests on outside metal part of the bearings which is way better than to squeeze the plastic part.
And with two new aluminum stop-rings, which is wide enough that they touch the outside metal part and not the plastic inside, the build is complete!
Step 15: Results
Now you can see the drilling results and they are excellent!
Step 16: Improvements
One thing that would be nice to do is to add like a 2-3mm thick aluminum base plate to the existing one. It will not only give more rigidity to the base but it will be more durable.
Another thing would be nice if the base would have more grip, quick and simple solution would be to glue like a 220-grit sandpaper to the bottom of the base. But then it can affect the accuracy of the tool, so it’s hard to say is it worth doing it.
If you need, you can add holders for drilling holes in the round objects or a handle or anything else you want.
Step 17: Reducing the Cost
The first version (first picture) of the guide felt flimsy and sometimes inaccurate, but the second and final version (second picture) fixed all of the problems. Now I can honestly recommend making a guide like this if you want high precision with your cordless drill. And the recommendation is even easier as the guide is so modular. If you want, you can reuse the parts in a different frame at any time, as they aren’t for one-time use.
I bought everything at a very good price, without plywood, it was only ~$50 (just for reference https://www.axminstertools.com/ujk-technology-dril...). Meanwhile four linear bearings and two 12mm shafts were more than half of the total price ~$30.
If you want to reduce the total cost of the build without hurting the performance too much, I suggest using only two but longer linear bearings (LMF12LUU and not LMF12UU which I used). You can also use thinner - 10mm rods and linear bearings (LMF10LUU) instead of 12mm ones. But don’t use anything smaller than 8mm.
Step 18:
As these are CNC parts, remember that the bearings must be lubricated and the shaft kept clean. And this design lets you do that as the bearings don’t go that low where all the mess are.
Step 19: END
So far, I didn’t notice any flaws and I love using it. If you like to tinker with stuff and you need a tool like this, you should consider making one yourself! It is accurate and the building process is so rewarding!
I hope this instructable/video was useful and informative.
If you liked it, you can support me by liking this Instructable / YouTube video and subscribe for more future content. Feel free to leave any questions about this build. Thank you, for reading/watching! Till next time! :)
You can follow me:
- YouTube: https://www.youtube.com/diyperspective
- Instagram: https://www.instagram.com/diyperspective
You can support my work:
- Patreon: https://www.patreon.com/DIYPerspective
- Paypal: http://bit.ly/SupportDIYPerspective
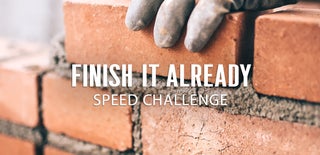
Participated in the
Finish It Already Speed Challenge