Introduction: Mint Green Concrete & Steel Stool
This instructable shows how to make a mint green concrete stool with a welded steel base (and also a white concrete one to go with it). Yes, the concrete is mint colored :)
I entered this in the Colors of the Rainbow contest, and would greatly appreciate your vote (if you like the project, of course :) ). Winning the 3d printer in the green category would be awesome...hint, hint ;)
I also made a white concrete stool to go with it, using the same process (minus the green pigment). The mint concrete color was achieved by using a combination of green and white powdered pigments in Fishstone’s glass fiber reinforced concrete (GFRC) concrete mix.
The steel legs for the stools are made from 3/8” steel rod. I used a Lincoln Electric flux core welder for the welding.
To achieve the curved concrete shape for the seat of the stool, I used a piece of acrylic cut to slightly longer than the melamine base, so that the acrylic would flex and bow when inserted into the form. This created the curved surface to form the concrete against.
CONCRETE (GFRC) PRODUCTS:
• GFRC Concrete Mix: https://goo.gl/keUX8H
• 1.5 Bag of AR Glass Fibers: https://goo.gl/t4qpTN
• Cake Fondant Tool for perfect edges: http://amzn.to/2w0JCVx
• Concrete mixer (HUGE help for GFRC): http://amzn.to/2kEnZFi
• White concrete pigment: https://goo.gl/w5KnHK
• Green concrete pigment: https://amzn.to/2JMRRtW
• concrete sealer: http://amzn.to/2xW7Gth
• Black 100% Silicone Caulk: http://amzn.to/2B64iRY
• Paste Finishing Wax: http://amzn.to/2kF565e
• Compaction Roller for GFRC: https://goo.gl/KJV3nv
• GFRC Recipes (w/ product links): https://goo.gl/35RvFM
• Hopper Spray Gun (for spray-on face coat): http://amzn.to/2Cf9dxi
• Air compressor (for spray gun): https://amzn.to/2G333Fo
WELDING TOOLS:
• Lincoln Electric Welder: https://amzn.to/2HWQ1ul
• Welding Gloves: https://amzn.to/2Ip7laD
• Welding Helmet: https://amzn.to/2whYHpq
• Magnetic arrow welding holder: https://amzn.to/2I1hdE8
OTHER TOOLS I USE:
• RZ dust mask: http://amzn.to/2wM8F1t
• Bosch 18V cordless circular saw: http://amzn.to/2wcDgnN
• Bosch 18V cordless Drill & Impact Driver Kit: http://amzn.to/2BCI753
• Dewalt Table Saw w/ 32” Rip Capacity: http://amzn.to/2yQd2Fy
• Dewalt 12” Miter Saw: http://amzn.to/2yQRgS6
• Cordless Track Saw: https://amzn.to/2Glyf2c
• Router: https://amzn.to/2G5e70P
Step 1: Build the Melamine Forms for the Concrete
This is a pre-cast design, so the stool seats are being cast upside down. The instructions are for a 16”x8” seat.
To make the form for each stool, you'll need to do the following:
(a) Cut melamine strips for the sides of your form to the height of your stool + 3/4". In my case, the stools were 2" thick (at highest point) so the sides were cut at 2.75". It is easiest to cut these strips on a table saw, but it can be done with a circular saw if you are very careful to make cuts consistently. Cut all the strips at once, so the height is identical. Then use your miter saw to cut the strips to the lengths you need. Cut each side a few inches longer than the base (e.g., 18" or so for a 16" side of the stool). The extra overhang gives you leverage to pull the sides away from the concrete when you demold.
(b) Cut a base piece of melamine to the size of your table, in my case 16" x 8".
(c) Cut a sheet of acrylic or other smooth plastic material to be about 1/8” longer than the melamine base; e.g., 16.25” x 8” (white dry-erase board might also work). I used ¼” acrylic, but would recommend using thinner acrylic and supporting from below. You will bend it so it bows upward when inserted into the slightly shorter concrete form.
(d) Cut support piece(s) for acrylic sheet. I did not do this in my build, but recommend it, due the issues mentioned and shown in the video. The support could be as simple as an 8” long ¾” dowel placed in the form, under the middle of the acrylic sheet. Better yet, use a jig or band saw to cut a couple pieces of scrap wood or melamine to the inverse curvature (e.g., convex) that you want your seat.
(e) Pre-drill holes in your sides, and then screw the sides to your base. I used 1.25" drywall screws for this.
(f) Apply paste wax to the inside of your melamine form and top of your acrylic sheet.
(g) Insert the support for the acrylic sheet, then bend the acrylic and wedge it into the bottom of the form. I also recommend applying some black silicone caulk to the sides of the form where you are inserting the acrylic before you insert it, so it is caulked from below, as well as from the top.
(h) caulk the inside edges using black silicone caulk, then run a metal ball tool around the edges to give you a perfect caulk line, let it dry, then remove excess caulk on either side of the line. (See my previous instructable for more detail: https://www.instructables.com/id/DIY-White-Concre... )
Step 2: Mix and Pour the Concrete
Check out my previous Instructables on GFRC concrete for more details on mixing. For this project, I used a just-add-water Glass Fiber Reinforced Concrete (GFRC) mix from Fishstone. You mix it by adding 1 gallon of water (8.2 lbs) for every 50 lbs (one bag) of mix. Just adjust the ratio for the size of your stool, factoring in about 10 lbs of mix per square foot (to err on the side of having more than needed). I mixed up 35 lbs for the two stools, and it was more than enough (we had at least 5 lbs leftover).
I only used about 2/3 lb of glass fibers, since I wanted the mix to be more flowable and did not do a face coat. I am able to eyeball the amount of fibers by adding slowly til I get the consistency of fibers I need, but you can get a cheap postage scale to measure them out (or if using a 1.5 lb bag, separate into two equal amounts by volume, and remove a little from one. Add fibers in slowly, e.g., a third at a time. Add a touch of water if needed to get the mix so you can pour it right out of the bucket into the form.
For the white stool, I added Fishtone’s white concrete pigment, adding about .5 lbs of it to the mix. Since I mixed up all the concrete for both stools at once, I did the white one first. I poured the white stool then added a little bit of green concrete pigment to the leftover concrete mix, re-mixed, and repeated, until I got the desired mint green pigment. Go slow here – it doesn’t take much green and IMO it looks best with a subtle pastel. If you aren’t doing white stools, I recommend adding some white pigment first, and then slowly mixing the green in.
When you pour the GFRC mix into the form, use your hands to work it into the edges and corners, and make sure it covers everything. Again, there is no need to vibrate. If you made your mix flowable (so it pours easily), it will self-level.
NOTE: I did not do a GFRC face coat for these stools, but you optionally can do this, and will likely get better results if you do. See my previous instructables for details on a face coat and GFRC in general.
Step 3: Grind Down the Underside of Stools While in Form
Option A (shown in video): after 6-12 hours, use a trowel to scrape the bottom edges of the concrete, using the sides of the form as a level guide (see video – easier to understand visually than describe in words). Make sure to crape away from (not into) corners of the concrete to avoid chipping the sides of the concrete, as you see me doing in the video. Once you’ve scraped away spillover, wet the exposed concrete in the form (which will be the bottom of the stool), and use hand diamond sanding pads at 100 to sand the concrete flat and level with the sides of the form.
Option B: Let the concrete sit for at least 24 hours (36 hours if it is under 70 degrees). Then use an angle grinder with a diamond cup (or wet sand with diamond pads) to grind down the underside, before you remove it from the form. It is important to do it before removing the top from the form, so that you can use the sides of the form as a guide to grind the underside evenly all around.
Step 4: Demold the Concrete, Slurry, Sand, and Seal
After grinding the underside down to be even with the edges of the form on all sides, it is time to demold the table top. Just unscrew / and pull the form apart.
If the side walls don't come off easily, use a rubber mallet to gently tap the sides of the form away from the concrete. If you flipped the piece over before demolding, it should be fairly easy to remove the bottom of the form (which is now on top). If it doesn't come off, then use a plastic putty spackle (not metal or anything sharp that could scratch the concrete!) to gently pry the bottom off. If it is really tough, then there is likely a vaccum between the form and concrete. In this case, you can use an air gun attached to your air compressor to shoot air between the form and concrete. This will break the seal created by the vacuum, so you can remove the bottom of the form.
Next given the whole service a quick wet sand, by hand, with 400 grit sandpaper. Just sand until you feel it smooth a bit. You'll feel it when you've removed the texture of the melamine, which is all you need to do.
If you are happy with the look at this point, there is no need to do a slurry coat. However if there are surface issues or voids, you’ll do a slurry coat. For the slurry coat, mix up some more of the GFRC mix (just don’t add fibers), and work it into the voids by hand (wearing rubber gloves of course). Let it dry for an hour or so (til it feels solid), then sand it off with 120 grit or 220 grit (try 220 first, and only go down to lower grit if you are having trouble getting slurry off. Repeat 2 or 3 times til voids are filled.
Then, apply a concrete sealer of your choice. Just follow the instructions that come with your sealer. I used Fishstone’s acrylic sealer for this one.
Step 5: Make the Steel Legs
Disclaimer: This was my first time welding, so these instructions are coming from a newbie :)
(i) I used 3/8” round steel bar for the legs. Each leg is formed from two isosceles triangles that are facing each other and overlapping. Each triangle is about 12” tall and total height of the legs is 16”. Three stretches connect at the top to form a base for connecting to the concrete seat, and one additional stretcher is used between the legs for stability.
(ii) Cut all the pieces of 3/8” steel rod (see my website for a complete cut list).
(iii) Make a plywood triangle jig you can use to weld identical triangles. I just drew the triangle on a sheet of plywood, and cut it out with a jigsaw. Then, I used a nail gun to attach it to another flat piece of plywood.
(iv) Weld four triangles for each stool.
(v) Make a second jig for assembling each leg. This jig is very simple, just two pieces of plywood that are parallel to each other and separated by the height of the seat.
(vi) Put two triangles in the parallel jig and mark the overlap on one of them for a cutout. Use an angle grinder to cut this triangle into two where marked (making a second cut to remove additional material so there is a gap for the other triangle to go through). Place the three pieces back into the jig and weld them together to make the leg.
(vii) Repeat (vi) to make the second leg.
(viii) Use right angle arrow magnets to hold the legs perpendicular to the four stretcher pieces and weld these together to complete the steel base.
(ix) Use an angle grinder with a flap disk to grind down all your welds and clean them up.
(x) Optional: use flat steel to create steel tabs at top of the steel base. Drill holes in the tabs, and weld these tabs to the steel base. This will allow you to attach the steel to the base using concrete screws (e.g., Tapcon).
Step 6: Finish the Steel
I used spray paint to paint one steel base white, and paste wax to protect the other steel base and give it a raw look.
Step 7: Assemble the Stool, and You’re Done!
I used Quikrete concrete adhesive on one stool, and clear Silicone caulk to attach the other concrete seat to the steel legs. Both adhesives worked well. (You could also use steel tabs and Tapcon concrete screws, if you like.) Before the adhesive sets, double check and make sure your table top is centered over the base (and adjust if necessary).
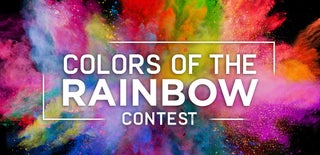
Fourth Prize in the
Colors of the Rainbow Contest