Introduction: Modern Bedside Lamp From Scraps
For this project I will be making a modern bedside lamp, it is my homage to Brutalist architecture with extreme minimalism and harsh lines.
The idea of this lamp is to create an ambient atmospheric light. It uses 0.2w and can be run continuously for around 6 years.
The difference between this light and other DIY lights is the ability to change the LEDs. You can use any usb powered light that is small enough to fit, such as the ones shown in this build. Some like the Soshine 6 led keychain (the 6 led version of the one used in the build) even have a built in switch and dimmer function.
I hope you enjoy it and if you make it please drop me a picture I'd love to see!
Step 1: Materials
For this project I used:
1 x Pocket Card USB Power LED Keychain (£2.32)
1 x 1m usb female panel mount to male connector cable (£2.99 for one but I bought 3 for future projects)
1 x scrap piece of wood (free)
1 x scrap acrylic (free)
1 x Epoxy glue ( about £3.00)
Step 2: Tools
For this project I used:
Two chisels (6mm and 20mm)
A mallet
A screwdriver
A saw (I used a Japanese pull saw as I like them but any woodworking saw will do)
A square
A ruler
Sandpaper (80, 120, 180)
Stanley knife (optional)
Some clamps (any will do)
( I also used a table saw and a bandsaw to cut the acrylic but there are many ways to do this)
Step 3: Making the Notch
This project will require two pieces of wood with at least one flat face (any timber yard can do this). You can use any prepared piece of timber for this and change dimensions as and when you please. As I started out with a scrap of poplar that cut in half I will move straight on to making the relevant cuts and recesses.
To make the notch I marked out a small rectangle on my piece of wood (see first picture for measurements). I used my ruler to mark my distances and may square to mark the lines (always use to top edge of the square).
Once everything was marked up I used my saw to cut the corners of my notch making sure not to go over the lines. At this stage it really doesn't matter about being overly accurate, cut as close to the lines as you feel confident to. The only reason I cut so close is it saves me some pairing (chiseling downwards) later on.
Once the you have sawn the edges clamp you piece down over the leg of a table placing your chisel as shown in picture two. To make yourself extra accurate you can first mark the line with a knife so as to give your chisel a groove to sit in although this is entirely optional.
Take two or three good hard wacks at it, making sure to keep your chisel nice and straight.
After go round to the other edge (as shown in picture three) and give it a couple of gentle taps. You only want to remove 2-3mm at a time (about the distance you should be going down when you first use the chisel)
Keep going until you reach your desired depth.
This is the same way you can cut the slots for half-blind dovetails by hand it just has angled sides not straight ones. But if you can do this you can definitely cut a dovetail.
Step 4: Recessing the Usb
This process is very similar the previous although this time it is a lot more intricate.
For this step you will not be able to saw the edges of all the sides so instead you will have to chisel down first and then cut across. Again only removing 2-3mm at a time.
As in the last slide the dimensions are on the first picture.
The two depths not shown are as follows:
Deepest - 11mm
Shallowest - 6mm
Step 5: Acrylic
Please refer to the picture for dimensions.
To cut the acrylic you can use all sorts of tools, I used a table saw and a bandsaw but as shown in the pictures above there are many ways to cut acrylic. If you don't have access to any of the tools above you can always get it laser cut.
The height is 210mm.
Step 6: Glue !!
To glue the wood to the acrylic together I used a two part epoxy from gorilla glue but any epoxy will do with.
You can drill a small hole on the inside faces of the pieces to put in a pin to stop them sliding, this will making clamping a lot easier but It's optional.
I also had to glue the two pieces of acrylic I used to get my desired thickness together using a solvent cement ( I do not recommend this. I only did this so I could use scraps.
After Gluing I sanded using 80 grit around a square block of wood I had lying about, working my way up to 180. Sanding is what gives the acrylic it's diffused look.
Step 7: CAD Files
Here is a link to the cad file for this project, enjoy :)
Step 8: Finished! (well Minus Finish)
So this project is pretty much all done, except for a bit of finish.
For finish I'd go with a nice simple finish like tung oil applied with a lint free rag, or some beeswax. Anyhow finish it however you see fit and enjoy!
Total cost to date: £9.31
If you've enjoyed this project you can follow me and / or check out my page for similar projects.
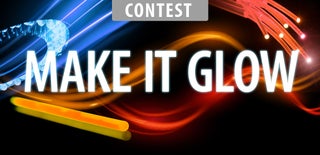
Runner Up in the
Make it Glow Contest 2016
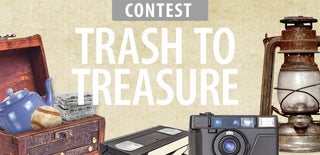
Participated in the
Trash to Treasure Contest 2017