Introduction: MulTable - the Modular/Flatpack Coffee Table
The MulTable (Multi-Table.... Get it?!) is a brain child of mine that Ive been working on for several years. I have built several iterations of this design, but this one is my favorite so far. I actually built this a few years ago, so forgive the fact that some of the steps wont have picture documentation, particularly with the legs, since they were actually cannibalized from a previous version. The Idea behind the MulTable is that it is a 3 piece coffee table that can be assembled in a ton of different ways, allowing it to have different looks, and different heights. It an also be flat packed for easy storage or transport...
Step 1: Designed in CAD
These days I design pretty much everything in CAD before I even buy materials. This allows me to really fine tune the look of the piece, work out all the kinks, ensure that it makes for the best material yield, and even drop the piece into the virtual CAD model of whatever house I'm living in to make sure it fits well! The CAD model can then easily be broken down into simple shapes that can then be imported into the CAM software which runs my CNC router.
Step 2: Select Wood for Top, Legs, Gather Other Materials
The legs on this piece are just made from layered MDF with a truck bed liner paint for surface treatment. The table's top however, is the main focus of the piece, so I wanted to do something a little different and more intricate. I had a whole tree worth of alder milled up and sitting perfectly dry in my shop, so I decided to pick through and find a couple nice matching boards to start with. I managed to find two live edged boards that I could "bookmatch" meaning they were essentially one thick board sliced lengthwise into two thinner boards, allowing them to be flipped over and the grain would be symmetrical. Typically when bookmatching two boards with a live edge, the opposite flat edges would be glued together creating a live edge on both outer edges of the the finished piece. I decided to do the opposite, by positioning the live edges towards each other and with a gap in between. I would then tie these two boards together with my own version of inlaid "bow-ties". The bow-ties are a unique shape that reflect the shape of the legs, and are made of Baltic birch plywood, with walnut veneer applied to the top. As for surface treatment, I decided to use a two part epoxy resin finish which is often used for bar tops. I decided to treat both sides of the table top so that it could be flipped over for different looks, or to get a fresh surface if one side gets too worn over time.
Step 3: Prep Boards for Top, and Mill Inlay Pockets
First I planed the boards down nice and flat, but with care not to take off too much thickness, from the sides which were to be bookmatched. The more you remove from the matching faces, the less identical/symmetrical the grain will look...
Once the boards were nice and prepped, and carefully laid them out on and clamped them to my CNC bed, ensuring that their placement together was exactly how I wanted them to be permanently once tied together with the inlays. I designed the inlay pocket file to cut each pocket continuously regardless of how far apart or close together the boards would be. I then ran the file and crossed my fingers!
Step 4: Cut the Inlays and Assemble Table Top
After I laminated some solid walnut veneer to a piece of 3/4" Baltic Birch plywood, I cut my unique inlay shapes out on the CNC router as well. I offset these shapes less than .01" to allow room for glue when it came time place them in their corresponding pockets. The shapes cut out nicely, and to my excitement, fit perfectly in their homes. I glued them in and allowed a little time for the glue to partially set. I then sanded while the glue still had a little bit of sticking power, which then picked up the fine saw dust from sanding and automatically filled any minor gaps in the inlay. I ended up sanding all sides of the table top to about 320 grit if I remember correctly.
Step 5: Surface Treatment, Oil Based Stain and 2 Part Epoxy
To give the wood a richer, deeper color, I applied 2 coats of Watco Natural danish oil according to directions and allowed plenty of time for it to dry thoroughly. Then came the step that I had been dreading all along, as it was outside of my comfort zone and a totally new experience for me. Epoxy resin finishes are notoriously difficult to pull off flawlessly, and I had never tried it before so I did a ton of research before attempting it. The particular epoxy resin finish I used is a pour-on type, meaning you mix the two parts together actually pour it over the piece and allow it to spread out and self level (you can help spread it around a little at first with a piece of carstock). This is the type of finish that usually results in a ton of hardened drips at the bottom edge of the table surface, which Im sure most people are familiar with. I did not want this drip effect, so I lined all edges with a couple layers of blue masking tape which stuck up a good 1/2" proud of the surface, to create a dam which wouldnt allow the resin to flow over any of the edges. Sorry I dont have pictures of this step. I will not go into all the intricacies of how to apply this type of resin, since there are plenty of through resources online and all types are a little different. I will list a couple tips however...
1. Remove as much dust as possible from your work area before doing any of this.
2. Create some sort of box to cover the entire piece with so that no ambient dust settles on it, or god forbid, a fly gets stuck in there
3. Check on it frequently, as you will need to continuously (for the first hour or so) use a torch to pop all the bubbles which will inevitably rise from the grain of the wood. Again, find more about this online...
So the first side came out almost perfect, save for a couple spots where there was excessively bubbling, which I had to keep popping, resulting in a slightly low spot at the very end. Hardly noticeable though. I let that side completely dry before flipping it over to do the other side. This time around I did not do the masking tape dam, and used my experience from the previous side to get the resin to flow just right to the edge and begin to flow over. I then continuously brushed it out along the edges to make sure it make any drips. This technique allowed me to full envelope the entire table top with epoxy resin with 2 (almost) perfect faces. The edges were a little bit imperfect, but were not very noticeable in the scheme of things. The two faces have about an 1/8" thick coating that is insanely durable. It can be scratched, but no moisture will be getting in there. I make a point to tell my guests to put their beers and drinks directly on the table, as we are a coaster free household!
Step 6: Build Legs
Sorry again, but no pictures for this step because I reused the legs a built for a previous version. Its an easy step to explain though. I used two layers of ultralight 3/4" MDF laminated together, so the legs ended up being 1.5" thick. I used my CNC router to cut them out, and included holes for the 1.5" closet rod doweling which would secure the legs together. I used some of this same doweling to create the nubbs which would help hold the table top in place in the various configurations. I then applied several coats of spray on truck bed liner paint to the MDF legs. This paint is durable, and easy to spot repair if necessary... I also used some loop side of some adheseive backed velcro in any areas where the top would contact the legs. This ensures that the paint doesnt rub off on the resin finish...
Im sorry but I'd rather not supply the file/designs for the legs, since I have put a lot of work into perfecting the designs and Id like to sell these someday. Im sure anybody determined enough to build these can come up with something similar though...
Step 7: Assemble the Table and Try Some Configurations!
There it is! I also included a quick composition I made of a previous all-MDF version I did showing some more configurations. Enjoy and check out my websites @ www.p-artcraft.com and www.makingitthere.com . Also follow me on instagram @making_it_there
Thanks!
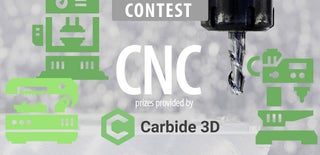
Participated in the
CNC Contest 2016
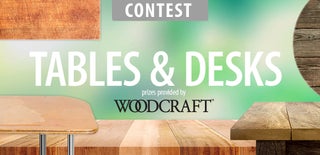
Participated in the
Tables and Desks Contest 2016
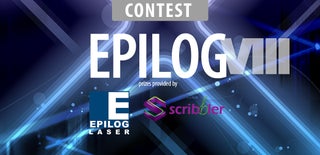
Participated in the
Epilog Contest 8