Introduction: Sandscoop for Metal Detecting
I've picked up a hobby that is most often reserved for a more mature generation: metal detecting. I guess I am in training for retirement. Like most hobbies you can easily get carried away buying up the best equipment you can('t) afford, so I elected to build my own sand scoop for those hot summer days in the water. This makes it possible to retrieve metal items from sandy beaches very quickly and move on the the next bottle cap (or coin, or even jewelry). As you will see from the list below you will need quite a few specialized tools or access to a proper shop to complete this project. I have been accumulating tools and junk for a few years, so I just needed a plan and some time.
Items you will need include:
- Cardboard for your template
- Pen, marker and ruler
- Sheet metal (2 feet by 1 foot), thicker would have been better I had 22 gauge on hand
- 1 foot of 3/4 inch square steel tubing
- 1 foot of 1 inch square steel tubing
- 1 foot 1/2 inch angle bar
- Wooden handle, mine was from an obsolete dandelion puller
- Can of metal spray paint
SAFETY WARNING: There are may opportunities to get hurt on this type of project. Make sure you know what you are doing, or get someone to help you. Safety equipment such as gloves, face shield, welding goggles should be worn when appropriate.
Tools that you will need include:
- Welder, clamps, safety equipment ect.
- Drill Press with a 1/2 inch bit and some oil
- A full set of snips, power cutter optional
- Angle grinder, with a set of metal cutting blades too.
- Metal brake, and a set of hand-held sheet metal locking pliers
- Hammer, anvil, vise
- Jigsaw
Step 1: Prototype
It is always a good idea to start any sheet metal project with a prototype with a similar thickness material; as you will inevitably find flaws and improvements to your design. Remember that your material has a thickness and folds will "eat up length" in ways you may not have thought possible.
I actually used the box from my metal detector to draw up the design, it was a little thicker than required, but it worked out ok.
I spent quite a bit of time on "Google image search" for inspiration; there are a tonne of different designs out there, many of which are simpler and cheaper than what I made. I initially planned to make a 4 sided design, but I was concerned that the base would deform quickly and lose its rigidity. The extra fold from the 5 sided shape plus the angle bar I added on the outside of the scoop really toughened it up.
Step 2: Cutting Out the Template
I then unfolded the cardboard template and traced the pattern onto the sheet metal with a marker. This is your last chance to incorporate any changes you were considering from your prototype: it is sad to throw out a piece of sheet metal due to your lack of planning.
Cut around your pattern as a rough cut first, I invested in a cheap power shears to do this: worth every penny. You can clean up the cuts later with your right handed and left handed snips. I cannot claim to be an expert, so please research on instructables and YouTube. I can provide you with a template if you would like; please just send me a message and I will gladly give you an improved version.
Step 3: Holes and Folds
I actually bought a new drill bit for this project because I knew the cheap ones I had were going to make this job a nightmare. Make sure you oil your bit and surface sufficiently to ensure you don't overheat the bit and shorten it's usable life. I avoided drilling close to folds and edges to avoid weakening them. This made the folding a little more complicated; as the areas with holes were more susceptible to unintentional folding.
I didn't draw out a drill plan, but I tried to make a logical pattern that would not be too distracting. This step took me 1.5 hours, and I suggest to not attempt it in one stretch. Make sure to clean up after this step as you will have shards of metal all over the place.
I was keen to start the folding straight after the drilling, but resisted the urge. I could tell that there was a certain order to the folding that was going to be optimal and that that the welding of the handle and and spine were going to present a challenge. After staring at the pieces for a while I realized that there only a couple of folds that were possible in the sheet metal brake, and in a few cases, I couldn't complete the fold (just get it started). I think that I could have used the brake more had I elected to make 2 pieces, but I really like the idea of folding it from a single sheet, plus it gives a little more rigidity. Particularly given that I am a terrible welder. The folds that could not be completed in the brake were either done with the hand tools, or scored with a chisel and hammer and forced by hand.
Step 4: Welding
I learnt so much about my welder on this project because I welded tubing to tubing, tubing to sheet metal and sheet metal to sheet metal. This mean that I had play around with the limited settings on my econo-welding kit to get the desired results. I am definitely no expert in this department, so I can't really give much advice: do your research.
I cut my square tubing so that the angle spine met the square tubing with as much weldable contact as possible. This intersection is really crucial as there will be a lot of stress on this joint. I then welded the spine onto the sheet metal trough.
I know my welds are ugly and they are bound to fail. I can live with that.
Step 5:
The exit of the 3/4 inch tubing from the top of the scoop was perpendicular to the spine, and I wanted to have the handle at an angle to make the digging and dumping more ergonomic. Most commercial scoops have an angle of 10-20 degrees, and after using it, I can see why. So I made a slot in a piece of 1 inch square tubing and welded the pieces together (please see the photos).
The full inch tubing afforded a slightly larger handle space, the updated version might have a circular tubing. I cut off the handle from a dysfunctional dandelion puller, cut one end square with a jigsaw and hammered it into the square tubing. I was going to put a bolt through it, but there is no way it will be coming apart.
Step 6: Paint and Verdict
Although I like the look of the raw steel, I elected to put a few coats of rust proof paint to protect it. Much of the paint has come off along the edges and the spine as expected, but it will still help protect the other areas.
I used it for 5 hours so far in rather difficult circumstances. The beach sand was often a mix of gravel, shells, and clay, but it worked very well. I had a few lead sinkers slip through the holes, but there is no way to avoid this. The front edge is getting a little mangled, but nothing a few hammer strikes every couple outings can't fix (you can see the extent of the damage in the video).
Future improvements will probably include a handle of some sort; maybe just a length of 1/4 inch steel tubing along the top of the scoop to help grip it. It is quite bottom heavy; especially when full, and I dropped it several times while shaking out the sand. I would also have made the basket a little less high (not shallower), by an inch maybe.
Any suggestions would be well appreciated. I suspect that this is not my last scoop!
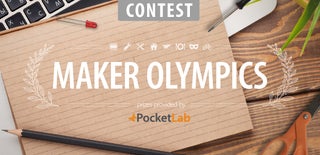
Participated in the
Maker Olympics Contest 2016
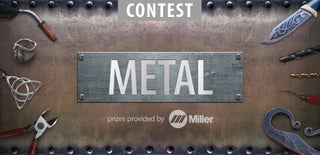
Participated in the
Metal Contest 2016