Introduction: Simple Roller Style Rolling Pin
When thinking of gifts for my family, I often try to make something in my shop. Not only can this save money, but it also tends to mean more to the recipient. This year was no exception. With a recently purchased lathe, I knew that a rolling pin would be in the works. Having never made one, this is my take on a classic roller style rolling pin design. The handles spin freely from the body of the rolling pin on a HDPE bearing surface attached to stainless steel carriage bolts to prevent rust. A simple cutting board that matches the rolling pin makes it the perfect gift for anyone that enjoys to cook.
Step 1: Tools and Materials
Materials:
- Hardwood (I used walnut and maple)
- Stainless Steel Carriage bolt - 3/8 in - 16 x 6 in
- 3/8 inch Pex
- 3/8 inch Nylon washer
- Wood Glue
- Epoxy
- Butcher Block Conditioner
Tools:
- Lathe
- Drill Bits
- Table Saw
- Clamps
- Router
- Micro-Mesh
Step 2: Create Rolling Pin Blank
I wanted a rolling pin with a finished diameter no bigger than (but close to) three inches. Since each of my boards were around 3/4 inch I glued together 4 three inch wide boards. This resulted in a blank that measures 3 x 3 inches and about 14 inches long.
Step 3: Center and Turn Rolling Pin Body
Mark the center of each end of the blank. Mount the blank between centers and turn round. Sand smooth to 320 grit. I applied a coat of Butcher Block Conditioner because I couldn't wait to see the beauty of the wood grain (not yet needed).
Step 4: Turn Dovetail and Drill Pilot Hole
Mark and turn a dovetail tennon on each end (only one end is pictured here). This dovetail will allow the rolling pin to be held by a nova chuck so the pilot holes can be drilled precisely in the center of the rolling pin. If this hole is drilled even slightly off square you will notice it when using the rolling pin.
Once mounted in the nova chuck, drill a hole the size of the minor diameter of the threads being used to tap the hole. If using a 3/8 inch bolt, use a 5/16 drill for this pilot hole.
Repeat on each end.
Step 5: Create a Wood Tap and Thread Rolling Pin
I wrote a very detailed instructable on how to make a wood tap from a bolt. The tl;dr version is:
- Taper the end of the bolt on a bench grinder
- Cut flutes in a bolt using files or an angle grinder
- Clean up threads with a nut
In that instructable the head of the bolt was removed. In this application the head is very helpful with threading the rolling pin. Please see that instructable for clearer directions.
With the rolling pin still secured in the nova chuck, position the tap in the pilot hole with a socket supporting the tap in the tailstock. Using the tailstock in this manner will allow you to apply pressure to start the tap but then allow the tap to pull the threads through at the correct feed rate. You will not need to continually apply pressure from the tailstock once the threads start, you will only need to keep the socket in the correct position to hold onto the head of the bolt. If it isn't obvious, do not turn your lathe on for this tapping process. Thread the entire hole by hand, clearing out the chips every 1/2 inch to an inch.
Thread two inches into the rolling pin. Repeat on each end.
Step 6: Polish Carriage Bolts
The slot cut in these bolts is not necessary. This was the first time I had ever done anything like this and didn't know if I would be able to grip the bolts when epoxying in place without a slot. I will talk more about this in step 12.
Grip the carriage bolts in the nova chuck with the faceplates removed. Using a metal file, remove any manufacturing marks on the head as well as turn the head completely round. Make sure to grip onto the threads and not the square portion of the carriage bolt. Don't worry about possibly damaging the threads towards the head of the bolt, they will not be used as threads and will only be used as a bearing surface.
Not needed unless you are worried about precise adjustment of the carriage bolt when epoxying in place. Using the tool rest, mark a line through the center and cut a slot using a cutoff wheel in a rotary tool.
Using the file, remove the square on the carriage bolt. (not shown)
Polish to your liking. Wet sand from 120 grit through 600 switching to micro-mesh. If you'd like a more brushed finish, you can stop at 600 grit or anywhere in the micro-mesh.
Repeat with the second bolt.
Step 7: Turn Handles
I created a template drawn in solidworks and glued it to a piece of cardboard to determine my overall shape.
Once the blank is glued up and mounted between centers, mark the transition locations. Use calipers and a parting tool at these locations to cut to the correct depth. Connect the cuts and sand smooth. Be sure to cut a dovetail tenon on each handle so they can be mounted in the nova chuck in the next step.
Attachments
Step 8: Drill Handle
Cut out the handles on the bandsaw and mount them in the nova chuck.
Flatten the end of the handle. This can be done with a forstner bit as show above or by using traditional turning tools. I used a forstner bit because I wanted an exact 7/8 circle (just bigger than the head of the carriage bolt) on the end of the handle.
Drill a hole just bigger than the outside diameter of the PEX that will be used in the next step (mine was just under 1/2 inch so I drilled using a 1/2 inch drill bit). Drill completely through the handle.
Step 9: Insert Pex
Since the carriage bolt is what the rolling pin will turn around, I didn't want the threads to eat away at the wood overtime. PEX is made from HDPE which means it's really tough and slippery (perfect for a bearing surface). Cut two lengths of pex as long as your handle. Use sandpaper to rough up the outside of the PEX, this will give more surface area for the epoxy to hold onto.
Mix epoxy and apply it only on the inserting end of the PEX (not in the hole before inserting it). As you press the PEX in the hole the epoxy will coat the entire outside of the tube. If you don't get the entire tube in place that is fine, cut off any extra. Once dry (this can take longer than expected because air can't get to the epoxy, I waited 24 hours) drill out the inside of the PEX slightly larger than the carriage bolt. I drilled this hole using a 25/64 inch drill bit. Sand and repeat with the other handle.
Once finished, cut the tenon of each handle and sand smooth.
Step 10: Cut Flutes
These handles were not designed to be removed so we want to give more surface area for the epoxy to hold on to and keep from coming unscrewed. Using a cut off wheel on a rotary tool or an angle grinder cut 4 or 5 flutes along the bottom inch of threads in the carriage bolts.
Step 11: Remove Tennon and Dress Edge
Using a crosscut sled, remove the tennon from each end of the rolling pin body. If I had thought about it earlier, I would have used the lathe to dress the end with a chamfer. But since I did not, I cut this with a router.
Step 12: Epoxy Handles Into Place
Mix epoxy and place it in the threads of the rolling pin body. Do not place it on the threads of the carriage bolts. We don't want any epoxy escaping the hole to accidentally glue the handle in place.
Place the nylon washer on the carriage bolt to act as a bearing surface between the handle and rolling pin body.
Tighten the carriage bolt in place.
This was the point where I was originally concerned about being able to adjust the carriage bolt of the rolling pin. We don't want it too tight or it will not spin, we don't want it too loose or it will slide around and make noise. With the slot in place it was really easy to make this adjustment, but there is this permanent slot visible. I found that the epoxy acts as a lubricant until it starts to set. Because of this, on the second rolling pin I made (shown in the cover image and next step) I didn't cut these slots. I was able to fine tune the bolt using a pair of pliers with duct tape attached to the jaws for padding. This worked better than expected and if I make any in the future this will be how they will all be done.
Step 13: Alternate Patterns
The options for rolling pins are endless. This was my second attempt and I love this pattern.
Once the blank was glued together the extras were cut off and the rolling pin was made the exact same way as shown in previous steps.
Step 14: Matching Cutting Board
A rolling pin makes a great gift, however it is much better when paired with a matching cutting board.
I wanted a cutting board that measured 1 inch thick, 14 inches wide, and 11 inches deep.
Cut strips 1 1/8 inch wide and 14 1/8 inches long from the previously mentioned 3/4 inch thick boards.
Alternate the wood standing it on edge and glue together.
Step 15: Flatten Cutting Board
Scrape off as much dried on glue as possible to protect your planer blades.
If your board is not flat, you can shim up the high point for flattening one face. Hot glue a shim in place.
Pass the cutting board through your planer but remember to use a sacrificial board ahead and behind the cutting board. This will keep planer snipe to a minimum.
If you used a shim, remove it once one face is flat and flatten the other face.
Step 16: Square Ends
Once flat, cut the ends even and square using a crosscut sled on the table saw.
Step 17: Sand, Router, and Finish
Chamfer the edges of your cutting board and sand to 320 grit.
Apply a few coats of butcher block conditioner to finish the project.
Step 18: What Will Be Your Design?
This was a surprisingly simple project that anyone can do. I'm thinking of making a segmented rolling pin in the future using this sled. What rolling pin designs have you made?
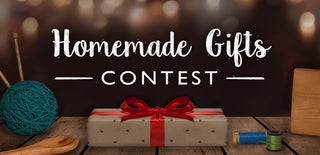
Participated in the
Homemade Gifts Contest 2017
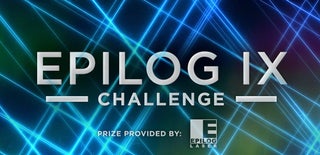
Participated in the
Epilog Challenge 9