Introduction: Steampunk Audio & Chronograph Station
Thanks to all of your very creative designs and projeccts, you all have inspired me to build my own Steampunk Audio & Chronograph Station. This project took me WAAAY longer than I anticipated and went way over budget, but once I got started, I found it hard to compromise and kept getting more ideas, so it essentially evolved from a basic - "let's build a Nixie Clock" project to a Frankenstein project from hell. Here's how I did it...
1. Built the Nixie Clock from a kit ordered online from PV Electronics. Fun to build and completed it in 3 evenings approx. time 10-15 hours if I recall. $112 including shipping I believe.
2. Found a period case to put it in. This took several weeks and prying a 1902 Symphony Talking machine from an antique dealer who rebuilds all sorts of machines. This one had many parts missing so he reluctantly let me have it for $25.
3. Bought a Henry Kloss AM-FM Model One radio from eBay $102. A great quality radio with very simple controls I thought would be very easy to convert. Toughest part was reconfiguring the tuner to a new dial and knob and trouble shooting a missing ground that i failed to land. I violated my own rule of using a printschematic and even though I took lots of pics, I didn't have the one that I needed. To get the radio working, I had to take apart ANOTHER Model One I had and compare. Yep... One stinkin' wire that was easily removed inadvertently.
4. Bought the tesla coil from Edmund's Scientific on the web, and Aerolux light bulb on ebay. $12 and $9 respectively.
5. I had the old medical book for a Halloween prop. And had to cut it in half horizontally to fit it on the deck. iPod station was $60 (ouch) and I destroyed the charger taking it apart so I had to purchase another for an additional $20. Oh yeah the charger has an IR remote control so I cut a window in the pages of the book for it to work.
6. Additional Items:
Copper plates - etched with Muriatic acid and Hydrogen peroxide method.
DC Ammeter - bought off eBay approx $15
Brass knobs for Volume & Radio function - Antique Bobbin drawer knobs $10
Brass Channel for Clock Frame - Hard to find in USA, got from UK approx $20 (0.25 inch angle)
Copper Came for stained glass tuner dial porthole - $20 off web.
Tuner knob - Hobby Lobby $5
Misc switches, LEDs, wire, solder, terminal strip etc. - Radio Shack $60 all told...
So yeah... way over budget, but hey I don't drink so... well I did while making it. Let's get started.
Step 1:
Step 1: Get a DECENT work space set up. This is how I started but later it became a hassle finding screws etc. that rolled around. I know better but when I reset my workspace it went better. I had to do this 3 times so I could find my tools and parts easier. I even started with a parts tray but I got sloppy at times.
Step 2: Build your Nixie clock and find a nice compatible transformer to run it. Take your time. Trouble shooting electronics without the knowledge or equipment to do it would be heartbreaking because you rushed it. Also... NEVER throw out phone recorders or any electronic device with a wall charger. They all essentially use a very narrow selection of voltages - mine came from a phone machine.
Step 3: Find or build your case. Here is how mine started out. Note the hole for the wind up crank. This is where I put the iPOD charging eye (was an electrical fitting with a clear marble in it. If an existing case, give it a day or two and the best way to layout your project will take form.
Step 2:
Step : Take apart the radio carefully and take pictures of everything - most notably the connections. Draw sketches of how it is connected. Save all the parts until the project is done. I never throw anything away until I am completely done. Sometimes a mistake can be fixed with a part you didn't think you needed.
Note how I labled the connections with tape. I later wrote right on the circuit board what the connection went to.
The knobs were epoxied directly into the brass hollow knobs I bought. I had to cut them open first on a band saw. Just be sure to spin them as they are gluing in. One of my knbs is slightly crooked when you turn the volume all because I didn't check this.
The schematic was the connection for the AUX input to the radio. I de-soldered it from the circuit board and had to know what contact points for the direct wire onto the board. When I got NO SOUND after finally assembly, I had it trouble shot to this board, thinking I overheated it to get the solder off. But the ground was off from this switch.
Step 3:
Step 5: Figure out where the component assemblies are going to fit and not interfere. This is extremely important as space fills up quickly. Measure twice cut once. I knew the area under the Telsa would be tight, but it nearly killed the inital concept. See later pics.
Step 6. Locate by placing the components in their relative locations. If all looks good, cut your case and and start to install the key / major sized pieces.
Step 4:
Step 7: Fitting the other parts. The book was easy in that there are many instructables on making book safes. Use the same concept of gling the pages, then cutting it out. I used the method that peels the cover completely off and reattached with hotmelt glue. Worked great. Remember to save the initial pages - if I hadn't you woulldn't know what the author looked like!
Step 8. I built the Tesla stand from scrap plexiglass. I love this material as it is easy to work with and non conductive and tough. The Tesla needed 6 vdc so I tapped of the 5 volt output of the iPOD charger. It worked perfectly. It draws like 400 mA DC so I was lucky with the ammeter range.
Step 5:
Step 8: I had a lot of trouble with the etching. I really don't think the laser printout transfer on paper works at all and the transperency works far better but still requires way too much work to touch it up. Any thoughts on how I can make this go better?
Reference the methods on other links here in instructables. Take note of all safety precautions for splashes and vaoprs. This is serious chemistry that can damage your lungs and eyes, & skin. Clothes too!
Step 6:
Final steps...
continue to add in your components wiring as you go along. Use a schematic. I didn't create a full blown one (sketch only) and made mistakes to be redone. Keep wires long until final assembly. Test your system periodically to ensure the equipment still works before going to far, otherwise a mistake can be costly to fix in terms of rewireing, time and materials.
Some notes:
1. I love tie wraps to keep wires for a sub-system together.
2. Heat shrink tubing works the best but is costly especially if you rework wiring.
3. keep wire color codes consistent. I wish I had some 22 awg wire in white but i didnt so I repainted it on the ends to avoid a mistake.
4. Tin all ends first before soldering wires together, makes for a nice job with no stray pennants.
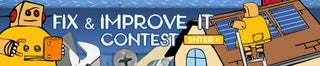
Participated in the
Fix & Improve It Contest