Introduction: The Electric Motor, DC Motor Theory Project.
This is a very nice little project, it uses lots of really useful hand skills, including marking out, cutting, filing and drilling, it also uses different materials, wood, metal, silver steel, brass shim, and copper, and at the end you have a really nice looking motor which works really well.
The tricky bit to make is the horse shoe magnet. I have made a jig to use on my 10 tonne press but you should be able to find a suitable former and bend the rod around it?
So how does it work??
Its really simple you have an electro magnet which when energised will attract the rotor, however when the rotor is near to the poles of the magnet the magnet is turned off by the cam and points. The rotor then freewheels past the magnet before the power is then turned on again attracting the rotor again and so on. If you get the timing correct the motor will run very nicely and by adjusting the tension on the brush you can increase the speed.
Step 1: The Parts Required.
As the pictures show you will need Some wood bits which I have described in the "Wood" section.
A piece of sheet metal about 1.0mm thick and about 150mm square this is described in the "The sheet Metal Parts" section.
You will need 10mm diameter steel rod to bend into a horseshoe magnet and 0.5mm diameter enamelled wire to wind the coils.
A piece of 5mm diameter silver steel 72mm long.
Brass shim to make the brush. 70mm * 12mm * 0.3mm thick
copper to make the cam 25mm square and 3mm thick.
6 off M5 nuts plus one M5 washer.
1 off M5 screw to retain brush about 6mm long "pan head"
1 off No10 * 2" wood screw
3 off No10 * 1 1/4" wood screw
12 off self tapping screws No4 * 13mm long
1 off M5 20mm allen head screw (brush adjustment)
And what ever paint finish you wish for the wood and metal bits.
Step 2: The Horse Shoe Magnet.
The horse shoe magnet is made using 10mm diameter steel bar (lowest quality you can get, which is soft and easy to bend!) , I have a jig which allows me to bend these on a 10 tonne hydraulic press. Once formed using the press I then finish it off by bending in a vice until true.
The hydraulic press forms the bar into a internal diameter of about 50mm, so internally its 50mm and 70mm width. You should be able to bend 10mm rod around a suitable 50mm diameter former, but you may need to keep the starting length long to give yourself some leverage.
Now the magnet needs cutting to size, I find positioning the magnet next to an engineer’s square and marking off at 110mm works well. Then cut to length and true the ends. While I have the square out I also mark off the 35mm from the end where the wire start.
I start the wire coil by taping the 0.5mm diameter enamelled wire and bending it to a right angle, I have also wrapped the end of the wire around the magnet so it doesn’t get moved around too much. (It would be heart breaking if you finished the coil just for it to break at the start)
At this stage I should point out that there are 4 layers of wire and each layer has about 60 turns of wire, making 240 turns total. Having said that it is worth taking your time with the first layer as this will make the rest much easier and neater.
SO do 4 or 5 turns of the wire keeping it very tight and close then while keeping the tension on the wire put a drop of superglue on the wire to keep it in place.
Then continue to wind the wire until you get a few mm from the end, then put another drop of superglue on it. This is basically insurance as the last few turns of wire and the starting of the next row is the tricky bit and you may find the wire falls of the end and you have to try again.
I have done a few of these motors now so I seem to have the knack of winding the coils. But all I will say is take your time and put a drop of superglue every time you have a good run of wire and particularly at the ends.
Once you have completed the 4 layers lightly twist the two ends together and put more superglue over the end to hold it all in place.
Now do the other coil! The only difference is that the coil is wound in the other direction. I am not sure if this makes much difference but it seems like the wire thing to do for maximum magnetic strength?
The finished coil has some heat shrink on the wires to hold them together and in place.
Step 3: The Wood Bits
The wood Bits
There are 4 parts of the motor made from wood. The base, the magnet support, the shaft support and the magnet retainer.
Cut the base piece of wood from the plank, make sure it is cut square and at a length of 200mm. the wood is planed pine and is 93mm wide and 14mm thick, because the wood is planed timber it can vary from these dimensions, it doesn’t really matter as long as you adjust the shaft supports so that the motor shaft centre
is in line with the magnet centre.
Sand the ends to remove all cutting marks and lightly sand the edges to remove the sharp edges.
Next the magnet support and shaft support can be cut from the 44mm square planed pine plank. These should be cut to suit the dimensions of the base width approx. 93mm long, or shorter so they sit nicely on the base, either way they should be cut the same length.
Choose one of the bits and cut 45⁰ angles each end starting 10mm up from the bottom.
The last bit to cut is the magnet retainer this is cut from a plank of approx. 50mm wide by 14mm thick plank it only needs to be about 20 mm wide so you can get two lengths out of once piece of 90mm long wood.
Once I had finished all the bits of wood and drilled the holes for the magnet, I then stained the wood and varnished it with two coats to give the pine a good rich colour and nice shine!
Step 4: The Sheet Metal Parts.
The sheet metal parts
The plate steel are cut from a 150mm square 1mm thick. As shown in the picture I started by cutting 3 strips 15mm wide, true up the edges as you cut each strip. This is a good exercise for marking out hacksawing and filing. Next I cut the brush holder 30mm by 50mm.
After marking out the strips I then dot punched the holes and cut all the bits to length. The offcuts (marked with a cross) should be kept to allow the bends to be formed.
Now I moved onto the brush holder take care to cut on the correct side of the line as shown in the photos, this makes it easier to bend later.
I have jumped forward a bit. I have files all the radiuses and drilled all the holes. I did all the drilling in one go.
To bend the rotor pieces first position the strip in the vice at the lower bend line and make sure its square.
Bend over the end to 90⁰, I use a bit of wood and a plastic hammer it makes a nice sharp bend and leaves no marks.
Once you have bent over all the ends choose the longer off the two rotor bits and using 3 off cuts hold the rotor in a vice and bend the end over the 3 off-cuts. (As shown in the picture) Try to aim the hammer blow in a downwards direction and not towards the front which could bend the whole lot back.
You can see the result. Don’t try to bend it right back (with the hammer) just take the lot out and finish the bend by squishing in the vice. I should point out that this little vice has no serrations on the jaws so won’t leave a mark. Repeat for the other end. Then take the short rotor and bend the ends over but this time only use 2 off-cuts.
You should now have two rotors which are the same length but the distance of one piece of metal different in height.
If you find that one of the ends isn't square don’t worry but squeeze it in a vice and true it up. (As shown)
The brush holder is a bit fiddly so take your time and before you make a bend confirm which direction you should be bending.
Mark out the bend lines and then bend the top line first, as before bend it to 90⁰ in a vice then squish it in the vice so it doubled over.
Mark out and drill a hole in the middle of the turned over section, drill 4.2mm then tap out M5.
Position back in the vice at the second bend line and this time just bend to 45⁰ (opposite direction to the first bend)
The last bend is the horizontal bend, because the saw cut was on the right side of the bend line it should be neat once bent.
The completed items are shown in the last picture
Step 5: The Shaft, the Cam and the Brush.
The shaft
The shaft is made from 5mm silver steel. Firstly cut it to length (72mm long) then file a good chamfer onto both ends then cut a M5 thread 12mm long on each end. Finally lightly file where the thread ends on the shaft as there will be a little burr and make fitting the shaft into the 5mm hole hard.
This is how I cut the threads on the shaft, I hold the shaft in a pedestal drill chuck and with the die fully split open I put light down pressure on the drill handle then turn the chuck by hand. The "G" clamp stops the die holder
spinning. Once I have done 12mm of thread I then close the die in a little and go over the thread again. If you try to cut the thread in one go the shaft will spin in the drill chuck and mark the shaft, and the green stuff is cutting
compound which helps.
The Cam
The cam is one of the most important bits to get right, the more accurate this bit is made the better and smother the motor will run. I start with a strip of copper bar 25 mm wide and about 3 mm thick, you need to square one end of first the mark 25mm long.
Square up the cut edge and make sure the piece is 25mm square. Then mark out diagonals and then 3mm either side of the diagonals, it is very important that the diagonals are 90degs apart, check with a square before filing out.
Mark out the largest circle you can fit on the square and then file out in-between the 3mm guide lines. The radius should be about 10mm you can check using a 20mm hole saw. Or as I prefer just gage it by eye. Before filing the remaining points drill the centre hole first 2mm then check the alignment (and correct using needle files) then drill 5mm. Lastly file the points, try to stick to the circle and not just flat. And that’s it! The final truing can be done on the motor
The Brush
Lastly I forgot to take a picture of the brush but it’s basically made from a strip of brass shim (0.3mm thick), 70mm long and 12mm wide drilled 5mm at the bottom for fixing to the holder. The actual design of the brush is quite important to the running of the motor, the thickness and length and shape all can have an effect. For a good running motor what I have said will work fine however if you are looking for top speed then you will need to reduce the length and width to avoid it flexing too much and bouncing off the cam.
Step 6: The Build
The build
Take the magnet support and drill a 3.3mm hole through the centre (centre long wise and width) then screw the block to the base using a No 10 * 1 ¼” screw, the base hole was drilled 5mm and countersunk.
Now position the magnet on top of the block, and once you are happy it is straight and central mark a line either side of the magnet with a pencil.
Using a half round file cut a grove in the centre of the pencil marks just over the edge of the wood, this will be where the holes are drilled to hide the magnet wires. The picture shows the base on the pedestal drill at an angle. I made a jig to achieve this but you could just clamp the other 44mm square piece of wood to the other end.
Looking at the side view you can see what I am trying to achieve, the 3.3mm drill has been put right at the end of the chuck so it has enough length to make it through the wood.
With the holes drilled you can the drill and countersink the retainer, and then put it all together.
The rotating assemble starts but fixing the two bits of the rotor on the shaft using M5 nuts either side, obviously the two bits should be perfectly square to each other and square on the shaft. I had to try different M5 nuts as some are not very square. Then mark out the wood half way along and position the shaft support and mark out the holes pilot 2mm and then fix the support into place.
Do the same for the other shaft support then screw it in place and fix the cam using a nut either side and a washer in-between the nut and support. There should be a small amount of end float, and the cam should be positioned in-between the rotors.
This picture shows how the cam is positioned relative to the rotor. It’s not exactly in the middle which doesn’t really matter it will just make the motor run better one way then the other (or it will only run one way)
To get the position of the brush assembly, make sure the brush is bolted to the holder and is straight up at this point you should also remove the paint from where the brush fixes to the holder. Then position the assemble next to the cam so it’s just not touching, Also at this point turn the rotating assembly 360deg to check all the points of the cam just miss the brush. If the cam is not true you may have to correct this prior to fitting the brush assemble, else just make out the holes and fit the brush assembly with self-tapping screws.
Now onto the tricky bit mounting the rotating assembly. I have put a bit of masking tape onto the base under the assembly and also fitted a spacer between the magnet and rotating block, this helps keep everything square, but only works in the magnet block and magnet are both square. the distance between the two blocks can vary but in my case it is 51mm which makes the gap between the rotor and magnet poles about 3mm.
Using a pencil draw around the front of the rotating assembly, this will be used as a guide to drill holes just behind the brush assembly and shaft support so we can hide the wires behind.
Remove the rotating assembly and mark out two holes as explained above, then also mark out the main fixing holes which should be 20mm in from both sides and about 20mm front the front of the block. Drill all 3.3mm.
Refit the block with the spacer bit of wood then clamp with a "G" clamp as shown, then using a battery drill pilot the mounting holes from underneath.
Once piloted remove the rotating assembly and drill out the fixing holes to 5mm and countersink underneath. Then fix the block down using 2 off No10 * 1 1/4" screws.
Next we have to undo the front bits to allow the fitting of the hidden wires. I have used a small round file just to clear the holes drilled earlier. The paint will have to be removed from the back off both items, the wires will be clamped behind where the bottom screws are so just remove the paint in these areas.
You can see in this picture the shaft support has been screwed back into place (with a wire behind it) and the brush assembly is next to be fitted clamping the tinned wire behind the screw.
You will need to find a M5 screw to adjust the brush but for initial testing you can adjust the brush by hand.
And one last consideration is feet, I screw little rubber feed onto the base corners which helps stop damage to tables the motor may be sat on and lowers the noise!
Lastly you need to turn the motor over and finish connect the wiring. the first thing I like to do is connect a battery to the coils and arrange the ends so I have a north and south pole when connected in series then add the link between the two coils. One of the other ends of the coil needs to go to the battery and the other end needs to go to the shaft terminal. The brush wire then goes to the other side of the battery to complete the circuit. I have included a photo so you can see how this is achieved.
Step 7: Testing and Fine Tuning.
If you have managed to follow my instructions you should have a nice working model.
Firstly check that the cam is not in line with the poles of the magnet and check that the brush can be adjusted so it wont make contact when you connect the battery.
I am using a 3 cell LiPo battery connected via a deans plug which gives a good turn of speed, but you do need to be careful off shorts as a LiPo can give out a lot of current.
You will need to give the motor a flic to make it start and you may find it will run one way better than the other.
These motors will run very well if the timing of the cam is correct and if the brush to cam contact is true.
So when checking the trueness of the cam disconnect the battery and turn the motor by hand and see the contact with the brush, lightly file the cam until the brush contacts the cam at the same point each ¼ revolution.
If you looking for maximum speed you will need to experiment with the brush shape and length less mass seems to be better. AND if you wire the two coils in parallel then you will find this gives loads of extra speed, but also quadruples the current! And because the motor doesn't have bearings either the shaft or shaft support will wear (or both) if you are look for max speed then think about proper bearings.
Look out for the next instructables as the motor goes electronic with a optical pickup and microchip controlled mosfet switched coils (fully adjustable timing and coil duration plus "hit and miss" speed control).
Attachments
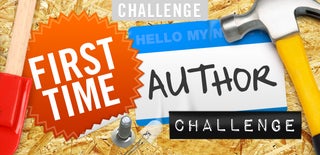
Participated in the
First Time Author Challenge