Introduction: The Ruler Project
One of the many subjects I teach is Drafting and Design which includes orthographic and isometric sketching by hand, as well as transitioning to computer aided design and manufacturing techniques. One of the most memorable projects from this class is "The Ruler Project", a project where students use CAD software to draw accurate rulers, then manufacture them using a CNC Laser Cutter/Engraver.
Everyone learns how to use a ruler sometime in elementary school, but that doesn't necessarily mean they understand how a ruler works. By the time students get to me (middle school), they often still feel uncomfortable with taking measurements and using fractions for dimensioning. My students find the ruler project really challenging, not because of the digital design tools and learning curve for CAD software, but because they've never been challenged to think about why a ruler is the way it is.
I am going to break this project down into the same steps I use with my 8th grade students to walk you through designing your very own ruler. I've also included two supporting tutorial videos as that may help walk you through the steps with greater ease.
Step 1: Needed Tools and Resources
If you plan to produce a ruler using a CNC Laser Cutter / Engraver, you could use a vast range of programs to create some type of vector image. Some programs are engineering / technical drawing focused like Onshape or AutoCAD, while others are more graphic design focused like Gravit or Adobe Illustrator. I wrote Instructables a while back about choosing free CAD programs and free Graphic Design programs that might help you better choose a software solution.
With my students, we use Onshape as its a powerful CAD program that has many of the same capabilities as Inventor, SolidWorks, Creo, or Fusion 360, but it is web-based and compatible with Chromebooks which is a must for my teaching environment. Students also use Gravit Designer, a web-based vector design program that is similar to Adobe Illustrator to add greater detail to their rulers and prepare designs for laser cutting. Both Onshape and Gravit are free for education or personal use and compatible with any device. I've made extensive tutorial videos for both of these programs on my Digital Classroom YouTube channel if you're looking for more support with either.
I also use a 40 watt Universal CO2 Laser Engraver to cut / engrave these rulers out of 1/8" birch plywood. You could use a variety of materials with a laser, apart from metal and PVC-based plastics with typical CO2 machines. There are also plenty of great brands out there for schools, companies, and hobbyists. Universal, Epilog, Full Spectrum, Glowforge, and Boss are some of the more popular names in the business.
Step 2: Guiding Tutorials
This project presents many challenges that can be difficult to follow. To assist, I've created two start-to-finish guiding tutorials. One tutorial completes the entire project, annotations and all in Onshape. The other makes the ruler in Onshape to take advantage of the linear pattern tool, but then adds the annotations in Gravit Designer.
Step 3: Drawing the Body
The first step in creating the ruler is to draw the ruler body. This is the bounding rectangle that all increments and annotations are drawn within. Typically, rulers are 6" or 12" in length. Though depending on your machine bed size you could easily make an 18", 24", 48" or whatever size ruler to fit your need. Height can also be whatever fits your need, but my students typically choose 1". The thickness of the ruler will be determined by the sheet stock you use to manufacture your ruler.
Every CAD program is a little different, but here's the steps to complete this part in Onshape:
- Create a new sketch on the top workplane
- Select the corner rectangle tool
- Click the center origin of the workplane once
- Move your mouse off to the side and click a second time to draw a rectangle (does not need to be precise)
- Type the desired dimensions (1" x 6") or (1" x 12") using your keyboard to set the rectangle's height x length
- Do not hit the checkbox to close the sketch just yet.....
We are going to put all of the details on a single sketch. In Onshape, exporting a vector file is by sketch. As a result, you want all of your ruler design to be on a single sketch or else you will need to export and combine multiple files down the road.
Step 4: Adding Sixteenths
It's time to start adding incremental lines. You can choose the level of precision for your ruler by the smallest increment. Typically, rulers use 1/16" as the smallest standard increment, though there are many machinist rulers that use 1/32" or 1/64" instead. Regardless of your choice, the process is largely the same for every increment.
First, choose whether you would like inches to be on the top or bottom of your ruler, in general they are to the bottom. Then draw a single line down from whichever edge you chose (I chose top for personal preference). Dimension this line to be 0.1" in length. Then dimension the line to be 0.0625" (1/16") from the left edge. This will act as the base for all future increments so ensure the distance between the line and the edge of your ruler is perfect.
We are then going to use the linear pattern tool to duplicate this line every 1/16th inches. In Onshape, select the linear pattern tool, then click on your line. The only two options you need to set are distance between copies (0.0625") and how many copies you want. If you are making a 6" ruler, you would need 96 (16*6=96). If you are making a 12" ruler, you would need 192 (16*12=192). You can only pattern up to 100 items at a time, so you will need to pattern 100 lines, then an additional 92 lines if you are making a 12" ruler.
Step 5: Adding Eighths
For the next incremental unit, we will be adding our 1/8" lines. After laying down 1/16" lines the entire length of the ruler, ever subsequent increment will be far easier and very repetitive.
- Go to the first 1/8" line, this would be the second 1/16" line because 2/16 = 1/8
- Extend the second 1/16" line by 0.1" by drawing an extension line from the end of the existing one
- Select the linear pattern tool
- Click on the new extension line only
- Set the distance between copies to be 0.125" (1/8")
- Set the number of copies to be 48 for 6" rulers or 96 for 12" rulers
- Double click to confirm
Now you have all of your 1/16" and 1/8" increments!
Step 6: Adding Quarters
For the next incremental unit, we will be adding our 1/4" lines. These steps are very similar to 1/8".
- Go to the first 1/4" line, this would be the fourth 1/16" line because 4/16 = 1/4
- Extend the fourth 1/16" line by 0.1" by drawing an extension line from the end of the existing one
- Select the linear pattern tool
- Click on the new extension line only
- Set the distance between copies to be 0.25" (1/4")
- Set the number of copies to be 24 for 6" rulers or 48 for 12" rulers
- Double click to confirm
Now you have all of your 1/16", 1/8", and 1/4" increments!
Step 7: Adding Halves
For the next incremental unit, we will be adding our 1/2" lines. These steps are very similar to 1/4".
- Go to the first 1/2" line, this would be the eighth 1/16" line because 8/16 = 1/2
- Extend the eighth 1/16" line by 0.1" by drawing an extension line from the end of the existing one
- Select the linear pattern tool
- Click on the new extension line only
- Set the distance between copies to be 0.5" (1/2")
- Set the number of copies to be 12 for 6" rulers or 24 for 12" rulers
- Double click to confirm
Now you have all of your 1/16", 1/8", 1/4", and 1/2" increments!
Step 8: Adding Inches
For the next incremental unit, we will be adding our 1" lines. These steps are very similar to 1/2".
- Go to the first 1" line, this would be the sixteenth 1/16" line because 16/16 = 1
- Extend the sixteenth 1/16" line by 0.1" by drawing an extension line from the end of the existing one
- Select the linear pattern tool
- Click on the new extension line only
- Set the distance between copies to be 1"
- Set the number of copies to be 6 for 6" rulers or 12 for 12" rulers
- Double click to confirm
Now you have all of your standard increments!
Step 9: Adding Metric Increments
The metric increments follows the same basic steps as the standard increments. First, choose what denomination and increments you'd like to use. In my example, I use millimeter, half centimeter, and centimeter.
Start by drawing a line on the edge opposing the standard increments. Like your first 1/16" line, this line should be 0.1" in length. Dimension this line to be 1 mm from the left edge of your ruler. In Onshape, you can easily enter millimeters by typing "1 mm" in the dimension box for Onshape to automatically convert millimeters to inches for you. This will act as the base for all future metric increments so ensure the distance between the line and the edge of your ruler is perfect.
We are again going to use the linear pattern tool to duplicate this line every 1 mm. In Onshape, select the linear pattern tool, then click on your line. The only two options you need to set are distance between copies (1 mm) and how many copies you desire. If you are making a 6" ruler, you would need 153 copies. If you are making a 12" ruler, you would need 305 copies. You can only pattern up to 100 items at a time, so you will need to pattern 100 lines at a time, then any additional lines (53 or 5) depending on how long your ruler is.
For the next incremental unit, we will be adding our 1/2 centimeter lines. These steps are very similar to the standard increments we added earlier.
- Go to the first 1/2 cm line, this would be the fifth 1 mm line because 5 mm = 1/2 cm
- Extend the fifth 1 mm line by 0.05" by drawing an extension line from the end of the existing one
- Select the linear pattern tool
- Click on the new extension line only
- Set the distance between copies to be 5 mm
- Set the number of copies to be 30 for 6" rulers or 61 for 12" rulers
- Double click to confirm
For the final incremental unit, we will be adding our 1 centimeter lines. These steps are very similar to the increments we added earlier.
- Go to the first 1 cm line, this would be the tenth 1 mm line because 10 mm = 1 cm
- Extend the tenth 1 mm line by 0.05" by drawing an extension line from the end of the existing one
- Select the linear pattern tool
- Click on the new extension line only
- Set the distance between copies to be 1 cm
- Set the number of copies to be 15 for 6" rulers or 30 for 12" rulers
- Double click to confirm
You have finished your metric increments!
Step 10: Adding Annotations
There are a few standard annotations that are included on every ruler:
- Units of measurements (IN and CM)
- Inch annotations
- Centimeter annotations
- Manufacturer, Name, or Title
Additionally, many of my students choose to add some extra features or opportunities of personalization like logos, images, fractions with increments, or even decimals with increments. If you're making the tool, you have full control over the design!
You can add text easily in Onshape by using the text tool, however the font choices are limited. It is also difficult to add unique text features like fractions with ease on ever increment as you can't pattern a text box. It is also challenging to import images or logos as well. Becuase of this, many of my students choose to export their ruler after completing all the increment lines, then add text and images in a graphic design program like Gravit Designer rather than Onshape.
Step 11: Exporting Your Design
To export your design, either after annotations have been added or prior to adding text, first confirm your sketch by clicking the green check box. In the features menu on the left hand side, you should see one sketch that includes all of your ruler detail.
- Right click your sketch in the features menu
- Select "Export as DXF/DWG"
- Select which ever format works best for your vector or laser CAM program, I typically use DXF Release 14
Step 12: Preparing for CNC Production
This step will vary depending on the brand laser you are using. Every laser runs off a different CAM programm and has its own driver to set parameters for material. My Universal runs from Adobe Illustrator into its own driver program.
Before sending to the Universal driver, we need to set the color codes on the ruler designs. For my laser, a red line set to 0.001pt stroke will be cut, blue strokes will be etched, and black fills will be engraved. For best precision, all incremental lines are blue, the outer rectangle is red, and the text and images are black. Students often customize their designs by alternating black fills and blue strokes to engrave or etch different parts of their designs.
Once opened in the driver software, the last step is to set the appropriate power, speed, and resolution for the material you are using to manufacture the rulers. For 1/8" birch plywood on my 40 watt laser, I use 100% power and 80% speed for engraving, 15.3% power and 24% speed for etching, and 100% power and 8.1% speed for cutting all with 500 PPI.
Step 13: Manufacturing!
After preparing your designs, its time to manufacture! Load your material of choice into the laser and engrave away. Once completed, you have a handy little tool that you made yourself. Well done!
As mentioned, this is one of the most memorable projects from my class because students think it will be easy, they think they truly understand how rulers work, but it turns out to be a different train of thought when you're actually drawing the lines yourself. They also get to use a ruler in their other classes that they made, and that's pretty cool too.
Thanks for reading, happy making!
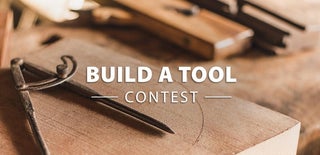
Participated in the
Build a Tool Contest