Introduction: Tiffany Lamp With Tin Sheet Base. (no Jig)
Tiffany glass table lamp with tin sheet base. With Filament LED bulb.
Tiffany glass work is something I have done for years, but a while back I realized there really wasn’t any point in trying to make a business out of it, as there really isn’t any profit to be made. As an example I could make a nice simple lamp start to finish in 3 hours. The material cost were about £10 but you would be very lucky if you could sell the item for £40 which means an hourly rate of £10 which for me is not worth it. So I only do it now for myself or presents.
Attachments
Step 1: Foiling the Glass and Getting the Shape.
So what you see is a relatively simple lamp using two different colors and a total of 12 pieces of glass. The height was dictated by the maximum length of the glass which is 12”. I then decided to make the base from tin sheet (which I already had) and attempt to follow the lines of the glass. I think it has turned out quite well and the method I used to hold all the glass in place doesn’t use a jig so is simple to do.
So the first stage was to design the lamp. I did a little video about this as it hard to explain, but you need to decide various parameters before you really start. This includes how many sides, the height, and how angled you want the sides to be. I start with a blank piece of paper and draw a center line then I add a top line perpendicular to the center. In my case I wanted to use the full length of the glass so I knew it would be about 305mm high, so I drew a line at that distance. Draw the shape you want and copy to the other side. if you are happy with this shape then on the top line draw half a circle with the radius on the top marks, then using a protractor divide the half circle into 6 sections (if you have chosen 12 sides) then measure the distance between points, this will give you the width of the glass at the top. Now measure down the length of the glass and draw a horizontal line it should be near the original line you drew but if you have a wide angle then line will be further up from the original. Then repeat the drawing circle and dividing by 6 to finally get the bottom width of the glass. Now you have all the measurement required to cut out the glass. But what I like to do is write down a list of all the measurement across the glass for top and bottom, then you can cut it all out at once, what you must make sure is that you "top and tail" each section.
Cutting the glass is a bit of a technique and I don’t really want to go into much detail here. But once you have marked out the glass find a suitable rule and position it away from the marked line so the wheel of the glass cutter will be exactly on the line. Then starting from the furthest edge make one firm score and that is it. To break the glass position a toothpick under the score line and carefully apply pressure to either side, the glass should then break down the score line.
With Tiffany glass work you use copper foil which has a sticky back, you pull of the backing paper and stick the foil around the glass and then fold over onto the front and back of the glass. There isn't much to this part, but it is worth taking your time and try to get the joints at a corner.
I have said this is a "NO JIG" design and what i mean by that is you don't need any special former to hold the glass at the correct angle for soldering, instead as you can see in the pictures i line up all the glass sections and place a strip of tape on the back at the bottom and the top. Then using a foam ball on a piece of string i put gentle pressure on the string and the pieces off glass all align correctly. and lastly in this part i soldered a ring of copper wire onto the top to hold the bits in place.
Step 2: Soldering the Glass Sections.
Now its a simple matter of soldering over all the joints. In the first instance i tacked the bottom sections of glass and then using a plank of wood through the middle i was able to solder the lengths with the joint very near horizontal. this makes it much easier as if you try to solder with the lamp upright then the solder will just run down to the bottom!
I use a 9mm solder tip in a 75 Watt soldering iron. and i use 50/50 solder (lead/tin) and you may be able to see in the last picture i use a acid based flux and brush it down the joints first. i have tried "safer" flux's but always find that an acid based flux is better.
Step 3: The Tin Sheet Base.
I decided to make the base of this table lamp out of 0.6mm tin sheet. The reason being i happen to have loads!
So i worked out the angles and lengths and marked out the required pattern onto the tin sheet using a marker pen. 0.6mm tin sheet can be cut with a decent pair of scissors but it does start to hurt you hand after a few sections!
In one of the picture you can see i have also cut out a template which i used to bend the edges over. this template was made from 2mm aluminium.
I started building the base by firstly cutting out the 12 sided sheet to fit on the bottom of the lamp, this was cut by drawing around the lamp as it isn't exact, i made a point of making sure i marked which face of the glass matched which edge of the tin sheet.
And before i got carried away i drilled a hole in the center and screwed and soldered the lamp fitting into place.
Step 4: Building the Base From Tin Sheet.
This was very "free style" i basically cut the sections out and one by one added them to the base. Each time i used a hacksaw blade taped to the glass to align the tin sections to match the same line. and after soldering the sections into place i then taped the tin and glass together to stop gaps appearing with the heat of the soldering.
I wasn't to careful about how i soldered these sections as i wanted a "man made" look? i can solder very accurately but in the past someone commented that the joints looked like it had been done by machine!
Step 5: Finishing the Build
So the last part of the base was to add the bottom. Again this is cut from tin sheet and cut using the base as a template. as you can see in the pictures i have firstly cut a hole in the middle using a hole saw then folded over the edges to make smooth "safe" edges for the cable. Also you should be able to see the 3 small holes which were enlarged to suit brass bolts which i sourced from dad's garage!. the bolts had the hex heads sanded off on a belt sander and were then cleaned up before soldering into place.
Once i had solder the base into place, i then wired up the lamp fitting (BC(bayonet connection)) It is very important to note that i use a 3 core cable. A tiffany lamp is effectively metal framed and the lamp holder is soldered directly to it, so you must use an earth wire.
Then i got the glass lined up correctly with the base and soldered the two bits together.
The last bit was to clean up the joints and wash away any remaining flux, then work out how to fit the bulb!
The LED Filament style candle bulb was fitted using a tube of cardboard and then the lamp was tested.
I was really happy with the results the two colors of glass i choose work really well together and look totally different colors when the light is on!
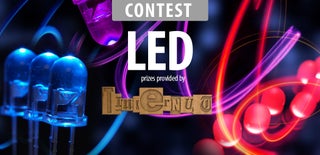
Participated in the
LED Contest
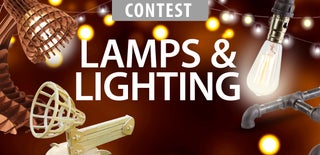
Participated in the
Lamps and Lighting Contest 2016