Introduction: Turning a 2x4 Into an Arbor Press
Late one night, music was playing and I was having a nice time doing some leatherwork. I had been working on this piece for a couple hours and one of the last steps involved setting some rivets. Reaching into my leatherworking drawer my hand touches the familiar tool and its matching anvil, "I've done this hundreds of times, it's going to be ok."
I shove the rivet post through the leather, firmly press the cap onto the backside, and place the carefully crafted leather onto the anvil. I press the die against the rivet, take a breath, and swing the hammer to set the rivet.
"GOSH DARN IT" I shout as I look at the leather. The rivet bent to the side and cut into the hide. With a gentle tug on the joint the rivet pops off as if I never even tried to set the thing.
"It's ruined...this is the last time!"
This same story has happened to me countless times but oddly enough while browsing Instructables I noticed the One Board contest and something clicked. I could just make a rivet press out of a 2x4! There's enough material there that with a bit of thinking and a lot of glue, I could make something that just might work!
Supplies
Raw materials needed:
-A single 8ft 2x4
-One foot of steel rod about 1/2" (I used 440c stainless tool steel at 9/16", but half inch would be substantially easier)
-Brass bushings with an Inner diameter a couple microns larger than than your rod
-Drill bit the same diameter as your rod
-Drill bit the same diameter as your bushing
-Spring with a force of about 1 or 2lbs per inch and with an inner diameter larger than your rod
-Shaft collar the same size as your rod
-Brass strip 1/2" x 1 1/2" x 0.04"
-Epoxy
-Elmers Wood Glue Max (any wood glue will do, but this one seems to be the strongest on the market)
-A box of 2in 6d Nails
Tools needed:
-Dust mask, eye protection, ear protection (always be safe!)
-Drill press (hand drill will work, but will make certain bits a lot harder)
-Bolt cutters
-Chisels
-Sandpaper
-Metal Files
-A way to cut steel barstock
-Some sort of saw to cut wood
-A way to shape wood (rasp, belt sander, whatever)
-A way to cut pockets into wood (chisels work, router is even better, a mill is better still)
Step 1: CAD
Full disclosure I went ahead and made some sketches as well as a whole other design that I ended up scrapping before arriving on this design. Now if you just want to dive in and follow along, here are the exact drawings I made for the press. It was incredibly handy to have these actually printed out so i could reference them without bringing my laptop into the shop.
As an important note to anyone who does engineering work, please make sure you learn how to do good drawings! Any dimension that is listed on these drawings is referencing specific edges, make sure you measure from those points.
Also attached is a .step file of the whole assembly since I'm sure that would be useful to someone
Attachments
Step 2: Measure, Mark, Cut
The very first step is pretty straight forward.
-Measure the length of board
-Mark with a sharp knife since you will get a more accurate and fine line
-Bias your saw to the waste side of your cut
-Repeat until you have all of your boards
Quick note! I'm pretty sure that all the board lengths are written out in the drawings, the one that was a little tricky to indicate was the length for the arm boards, those work great if you cut the boards to 18in.
Step 3: Mortise Jig for the Inexperienced Woodsmith
Ok, fine, you caught me, I don't know much about wood! My skillset is more in the areas of machining, metalworking, prototyping, and chopping up 2x4's with a chop saw. Without a ton of woodworking know-how I wanted to make sure that the mortise I was cutting would be nice and precise.
To do this I made a pretty simple little jig, by first cutting some reference blocks that were the distance between the back side of the support column to the lower face of the mortise (if this is confusing, I hope the diagram helps)
Then using some really nice screws (really recommend these ones to everyone since they don't require predrilling, and they are just a delight to use) I mounted the blocks to a piece of plywood which would act as a reference surface. Once I have 2 blocks mounted I clamped a steel ruler/straight edge over the marked line of where I wanted the mortise to end.
With all of this set up, I can now take a hand saw and cut out that whole area. The blocks and ruler act as little walls that minimize the amount of error I can make.
Step 4: Using Chisels to Carve Out the Excess Wood
Since using the saw from the side was taking forever I decided to make a series of long cuts along the top of the block. I then took a chisel and started to bite off little chunks of wood at a time. Initially I was coming in perpendicular to the surface but found that cutting the 2x4 that way ended up causing a lot of tear-out in the wood. Taking smaller cuts parallel to the surface yielded better results in terms of surface finish.
Step 5: I Told You I Am Not an Expert Woodworker
After using these guides and techniques the wood tore out a bunch and looked kind of awful. Fortunately there are glues out there that are really good at filling gaps, and all these surfaces wont be visible in the end.
If you are like me and are not super skilled at fine joinery I would say this is a great thing to practice with despite having less than stellar results.
Step 6: Making the Head Blocks Flat
A while ago I had seen someone use a really simple little wedge system to clamp pieces of wood in place.
All you need to do is get a straight edged piece of scrap and screw it down to a board.
Place your piece of material that you are working on against the straight edge.
Cut out a trianglar piece of scrap material and press it up against the free end of your workpiece.
Lastly take another piece of material and shove that one up against the triangle.
Screw it down.
Now if you want to lock your workpiece down, you just need to drive the wedge deeper into the setup and the workpiece will end up fixed to the board! This was the first time I have tried doing it and was stoked about how well it worked!
Anywho, once the board was clamped into place I went at it with the only hand-plane I own. It was my first time hand-planing something and I was pretty happy with the results. However I am totally cheating in those photos and not showing that the wood was not perfectly flat. At the time I was thinking that I could just fill any gaps with epoxy. That would absolutely work, but later on I did some stuff that made it so I wouldn't need to do that.
Step 7: Layout!
Using those handy drawings I made, I transferred all the measurements and marks onto the pieces of wood. Calipers are handy for this, but so a ruler and a square work just fine. I didn't end up marking out all the pin holes since the locations for them are not super critical to get right.
Make sure that you mirror all the features on the A side and the B side of each part, they should look like mirror images of each other!
Step 8: Sacrilege
Ok, some of you may look at this step and think that it's awful that i'm using a manual mill on wood. The wood could absorb moisture and cause rust on all of the precision surfaces. Well, I did it, so deal with it!
Some of you may be familiar with the post-it trick, but for those that are not, I placed a post it note on the surface i'm milling, swipe it under the endmill while raising the knee (or lowering the quill) until I can feel it drag against the endmill.
Once you feel the post-it drag, you can set all your dials, DROs, or whatever you are using to zero, and go from there.
Step 9: Milling
While milling, I didn't end up looking at the measurements much and instead just cut everything shy of the boundary lines. Since 2x4's love to tear out I took multiple passes so that the finished edges would be as crisp and as clean as possible.
Since I wasn't happy with how the hand-planning went, I also used this as an opportunity to get really a really nice flat surface on both the mating faces of the head block.
Also yes, I did vacuum every surface afterword's because I'm not a monster.
Step 10: Cleaning Up Corners
If you use a router or a mill to cut out the pockets, all your internal corners will end up rounded, which will cause your pieces to not fit. To fix this, just use a chisel and make those corners nice and square.
After all the milling was done and I fit everything up, there were some nice big gaps which isn't ideal and means that I messed up with fixturing in the mill, but whatever, we will just work with that.
Step 11: Layout of the Arm
Next up, place some layout lines for your arm pieces. They don't need to be absolutely perfect, "close enough" is plenty good!
Step 12: Pin Drilling!
Now that the arm pieces are cut out I decided to go in and drill a bunch of pin locations. These only really need to go in about half an inch, that seemed to hold perfectly well. You could just as easily drill all the way through, you would just need longer pins.
For the actual pins, a really cheap and effective pin is just a nail. I ended up using a handful of 6d 2in nails which seem like a nice size.
Initially I was pre-drilling with a smaller drill bit and then reamed out the hole by using a nail. I ended up switching to just cutting off the flat head of a nail, chucking the nail into my drill press, then using the nail itself as a drill. Oddly enough it worked out really well!
Step 13: Transferring Pin Locations
To transfer all the hole locations onto the other half of the arm, I simply cut off the head of a nail, placed the nail into a hole making sure it touched the bottom, then marked off a little above where it was coming out of the wood. I used that measurement to cut off the spike portion of the nail and repeated this for each hole.
Once there were a bunch of nail tips sticking out of the first half of the arm I pressed the other half on top. With all of the new marks, I drilled all the pin holes in the second part.
Now that all the pin holes have been drilled I made a bunch of little one inch lengths of nail, placed them in their holes and then tested the fitup.
Came out super nice and snug!
Step 14: Drilling More Holes!
Now onto the support column! Here I drilled 3 through holes on each side of the column.
Step 15: Making the Base
We haven't touched the base yet! To prevent it from feeling left out of the party I figured now would be a good time to include it.
I realized I didn't make a drawing for the base, so instead I just traced out where the support column would go with the two base parts smooshed up side by side to each other. I brought these pieces over the bandsaw and made the appropriate cuts.
Once the notches were made I lined up the support column with one half of the base and simply put nails through the support column holes, hammered them into the base part in order to leave marks that I could use in order to drill.
Step 16: Transferring Even More Holes
Moving onto the head block, I used the same technique of placing nails into the holes and hammering them to leave marks for drilling.
Make sure that you label what face touches what face! this will help make sure that the final assembly goes nice and smooth without any last minute errors.
Step 17: Everything Is Marked and Ready!
Look at you! You did it! You drilled a bunch of holes that match nicely with the other halfs!
Step 18: Glue, Heaps of Glue to Hide Your Sins
I saw once on the internet that exposed wood will form a patina which makes glues somewhat less effective, to get around this, just lightly sand all the surfaces that will touch glue.
Then just glop on heaps of glue, because if you are like me, you left a number of gaps in the fitup but don't want to take the time to start all over.
The glue I used was Elmers Woodglue Max which is supposed to perform quite well at gap filling, I'm pretty sure you usually want to use super thin layers of glue, but it does not seem to matter much with this stuff.
Step 19: If Things Don't Fit Perfectly, Just Press Harder.
Unlike most things, this is a very forgiving project, so when the pins were just a hair away from lining up correctly, I decided to just use a vise in order to press everything together more firmly. At worst, the nails would just dig into the wood in new places. Structurally, it probably wont matter much.
Step 20: Clamps and Curing
With all the glue applied, I clamped everything together and let it sit overnight.
Step 21: The Next Day
The next day there was tons of excess woodglue that had gobbed out. It was pretty quick and easy to get in there with a chisel and clean it all out.
Step 22: Setting Up the Pivot
Here is another place where things didn't end up as perfect as I wanted. The forked part of the arm bar was just a touch looser than I wanted, but still would work totally fine and perhaps even better since there would be less friction. However, this did not make clamping very easy. I ended up adding a piece of cardboard to shim the arm in place.
I marked off the center of the arm pivot, then used a super long thin drill bit I had in order to drill through the whole assembly. Initially I wanted a smaller diameter but long drill bit so i could use forstner bits to drill the major hole. Turns out the forstner bits I had were not long enough to drill all the way through in one go. If you are looking to do this, i'd recommend using something like an extra long 1/8"- 1/4" bit since it would be a bit stiffer.
Step 23: Forstner!
See how that little hole lines up with the tip of the forstner? That's what I wanted to do at first since I love forstner bits. Honestly they are just such a joy to use!
This hole was drilled to 3/4"
Step 24: Big Stiff Twist Drills
I ended up caving in though and using a bigger twist drill since it'd be longer and stiffer which is ideal considering we will need to have a number of holes all line up pretty tightly.
I hope it goes without saying that you really need to make sure these bigger holes are as perpendicular as possible!
Also this is the step that made me wish i had used 1/2" rod instead of the 9/16 that I had on hand. 1/2" bits are really common to have in twist drill sets, but 9/16 is less likely to be in your tool kit.
Just to be clear, the pivot holes on the arm are drilled with a 9/16th bit. All the holes on the head part are done with a 3/4" bit. Very very important to not forget this!
Step 25: Press Shaft Holes
Ok so for this part I know that I made the hole a touch off center, it bothers me, but the two halves of the head were not identical in thickness so this I think is a bit closer to the true center.
Anywho, not pictured here is the part where I place the bushing in the arm pivot hole of the head and the rod though the arms and head. Once you have all that assembled you can make a mark on the top of the head where the "tip" of the arm lands. I only realized this after the fact, but you really want the center of the hole a little bit behind this point because math.
These holes are all drilled to 3/4"
Step 26: Epoxy the Bushings Into Place
Alrighty, so now we mix up a little batch of 5 min epoxy (I used double bubble brand for this, but any will do) and spread it along the outside of your bushing. Be very careful not to get any on the inside of your bushings!
PROTIP: leave your mixing stick in the left over epoxy, when its cured you should be able lift the stick and the mixing cup with it.
Step 27: Rod Cutting
I cut a 5 inch length of my 440c rod for the main shaft. The length of that part is pretty forgiving so don't sweat it too much.
For the pivot rod, I shoved it through just the arm piece until it was flush at one end, then marked where it would be flush on the opposite end. Be a touch more careful with that cut.
Step 28: Deburring
Be professional and chamfer the ends of your rods with a file. It will look nice, prevent people from cutting themselves, and will make the press rod function much nicer.
Step 29: Panic, Just Panic a Bunch
After everything was all done and setup I place the main shaft through the top bushing only to find that it did not line up perfectly with the lower one.
Correcting this was a matter of panicking a bit while running a drill bit through the bushings to try and force them to line up, sanding the bushings to remove any traces of epoxy and to open them up just enough to make everything work.
I ended up using the mill as a lathe and turning down the diameter of the rod a bit. This both worked really well, but also was a bit dangerous so i decided not to document that part.
This is another reason why I wish I had used a 1/2" rod instead of 9/16. At 1/2" you can just chuck that into a power drill and sand it down.
Step 30: Springs!
I am not sure exaclty what size of spring this was, but it felt like it offered a good bit of resistance. I ended up cutting it a little longer than needed since that would provide a bit of preload and would hold the shaft collar in place.
With these components in place I tightened it all down and gave it a test.
Step 31: Well by Golly It Works!
After spending all this time designing, planning and building the thing, I was still a little surprised that it actually worked!
Step 32: A Totally Functional Press
At this point the press was totally functional, but a bit too rough around the corners for me
Step 33: Final Shaping
Here is where we get to clean up all those gnarly bits on the belt sander. Make everything line up, feel comfy in the hand etc. Belt sanding is its own art form so have fun with this step. If you mess up well, you can always file and sand stuff by hand.
Step 34: Sand and File
For all those delicate touches and features a rasp or file tends to work a little nicer than a belt sander. Now is also a good time to whip out your sandpaper and sand all the surfaces down to your desired grit. I could have sanded with much finer grits, but honestly a 150grit finish worked just fine for my purposes.
If you end up making one of these, this is the part that will really make your piece stand out if you take the time to do so.
Step 35: Wipe Off Dust, Wipe on a Finish
Once everything is sanded to your desired level of finish, wipe all the surfaces down with a damp cloth in order to pick up any extra dust. Then apply your favorite finish.
At first I was going to use a spray varnish, but I worried that it might jam up the mechanism, so I opted for my favorite beeswax and citrus oil finish. It colors things well in my opinion, and smells amazing!
Step 36: Lets Test It Out!
Hey look at that! A rivet that looks nice and is actually sturdy! This is a game changer for me!
Step 37: Reinforcement
I wasn't sure exactly how well the wood would hold up to the force being applied, and turns out it will deform a bit under the pressure. To remedy this I just cut out a little strip of brass, bent it to fit the edge then epoxied it in place. So far it seems to work well!
Step 38: Options for a Future Version
Now here I just wanted a quick fix, but I could absolutely see someone going at this with a jewlers saw and making some really rad functional inlay. Just an idea!
Step 39: FIN
Thanks so much for looking or reading this far! I'll be entering in the one board contest, so if you enjoyed this I hope I get your vote! Outside of that I hope you learned a thing or two along the way, and it'd be rad to see if anyone else tries to make one of these!
Have an awesome day you amazing person you!
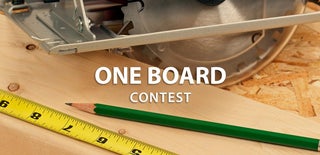
Runner Up in the
One Board Contest