Introduction: White Concrete & Live-Edge Waterfall Table
This instructable shows how I made a live-edge mahogany and concrete waterfall coffee table. I used a glass fiber reinforced concrete (GFRC) mix to get the gleaming white concrete. The live edge slab is Cuban mahogany and the legs are made from African mahogany.
If you haven’t worked with GFRC before, it might seem a bit intimidating; but it isn’t. It really isn’t a whole lot more difficult to work with than standard concrete, and the results that GFRC produces are amazing.
Step 1: MATERIALS
CONCRETE (GFRC) PRODUCTS:
• GFRC Concrete Mix: https://goo.gl/izSggQ
• 1.5 Bag of AR Glass Fibers: https://goo.gl/c9Vw9x
• Hopper Spray Gun (for face coat): http://amzn.to/2Cf9dxi
• Cake Fondant Tool for perfect edges: http://amzn.to/2w0JCVx
• Concrete mixer (HUGE help for GFRC): http://amzn.to/2kEnZFi
• concrete sealer: http://amzn.to/2xW7Gth
• Black 100% Silicone Caulk: http://amzn.to/2B64iRY
• Paste Finishing Wax: http://amzn.to/2kF565e
• Compaction Roller for GFRC: https://goo.gl/KJV3nv
• Powdered Concrete Pigment: (1 lb) http://amzn.to/2DXZU5k, or (3 lbs) http://amzn.to/2DXZU5k,
• GFRC Recipes (w/ product links): https://goo.gl/35RvFM
TOOLS I USE:
• RZ dust mask: http://amzn.to/2wM8F1t
• Bosch 18V cordless circular saw: http://amzn.to/2wcDgnN
• Bosch 18V cordless Drill & Impact Driver Kit: http://amzn.to/2BCI753
• Dewalt Table Saw w/ 32” Rip Capacity: http://amzn.to/2yQd2Fy
• Concrete mixer (HUGE help for GFRC): http://amzn.to/2kEnZFi
• Cordless Track Saw: https://amzn.to/2Glyf2c
Step 2: Flatten and Prepare the Live Edge Slab
The slab I used was mahogany, but the species you use is up to
you. Just take your time and pick out a shape that fits in the size of table you are making.
I used a router planing jig to flatten both sides of the live edge slab. Just search Google or YouTube for "how to flatten a slab with a router" and you'll find plenty of instructions about how to make this simple jig and the process. I then used a random orbit sander to remove lines left by the router planing process.
Next, you’ll want to create the miter. Since you don’t have a flat edge you’ll need to eyeball a good point to cut the slab for the waterfall. Use a straight edge to mark the line, then make a 45 degree cut on the line with a circular saw or track saw (you could probably also come up with a table saw jig to make the 45 degree crosscut). Remove the piece with the 45 degree overhang, grab the other piece and rotate it 180 degrees. After rotating the other piece, make a 45 degree cut at the very edge (removing little, and ideally none, of the top of the piece).
Note: come back and glue up the two halves of the slab at 90 degrees after you make the form – you want to make sure that the angle of the miter is identical to the angle of the form, so that the live edge is flush to the base and the waterfall of the form. After checking the miter is identical, use glue and 90 degree clamps or braces to glue up the live edge waterfall. If the angle of the miter isn’t identical to the form (like what happened to me – see video), use an angle bracket to temporarily hold the live edge miter at the angle of the form during glue up, so it is flush with the form during the concrete pour.
After gluing up the slab, pre-drill ¼” holes in the sides of the slab, and drive in ¼” lag bolts. These help secure the slab to the concrete (in case the wood moves over time).
After glue-up, seal the slab with your choice of finish (I used polycrylic). Sealing the slab before the concrete pour is important so it doesn’t soak up water from the concrete when the concrete is poured around it. Also, use a couple layers of painter’s tape to cover the underside of the slab to protect it from concrete during the pour.
Step 3: Cut the Foam Inserts for the Tabletop
To reduce weight and the amount of concrete required, you will cut inserts from 1/2" pink insulating foam (i.e., Foamular) to go inside the form. This way, the concrete is only 1" thick (except at the sides, where it is the full 1.5" thick). Just use an exacto knife to score the foam sheet so it is about 1-2" away from the edges of the form (and slab). After you score the foam, it snaps easily by hand. If you want it precise, you can also cut the foam with a circular saw or table saw.
Step 4: Make the Melamine Form
This is a pre-cast design, so the table is being cast upside
down. To make the form from melamine, you'll need to do the following:
(a) CUT COUNTERTOP BASE: Cut a base piece of melamine to the exact dimensions of your table top. I made mine with abstract angles, so I started with a rectangle, and then drew lines using a straight edge and pencil until I got a shape that I liked. Then use a circular saw or track saw to cut along the lines and create the polygon. (Or just simplify this, and do a rectangle
(b) CUT WATERFALL BASE: Cut a base piece for your waterfall to 3/4" longer than the height of your waterfall section. The sides will need to be angled at the same angled at the same angles as the corners of the bases that they touch. I measured and cut one side at the correct angle, then did the same on the other side, cutting the second side so the front of the piece was slightly wider than the table base, then snuck up on the second side with repeated table saw cuts, until it was the exact width of the end of the base piece.
(c) CUT SIDES: Cut melamine strips for the sides of your form to the height of your countertop plus 3/4". In my case, the table was 1,5" thick so the sides were cut at 2.25". It is easiest to cut these strips on a table saw. Cut all the strips at once, so the height is identical. Then use your miter saw or crosscut sled to cut the strips to the lengths you need, mitering the corners. If you do an abstract shape like I did, you’ll need to measure and cut the angle for each corner as you go.
(e) Go back to the previous step and complete the glue-up of the slab as noted.
(f) ASSEMBLE THE FORM: pre-drill holes, and then screw your sides to your base and waterfall. I used 1.25" drywall screws for this. (d) place your wood slab in the form upside down (with top of slab against bottom of the base and the waterfall piece). (d) Apply paste wax to the inside of your form and bottom/sides of slab. (e) caulk the inside edges using black silicone caulk and the cake fondants. (Check out my GFRC videos on my YouTube channel to see this process in action.) After the caulk cures and you pull the excess to leave clean caulk lines, and your form is ready.
(g) CROSS BRACE: Use scrap 2x4s and plywood to build a bridge where the bottom of the bridge is even with the top of the sides of the form. You’ll take scrap melamine pieces and cut them so they extend above the sides by the width of your scrap plywood (in my case ½”), and screw them to the sides of the form, adjacent to the area where your foam insert will go. That way, when you screw 2x4s to the tops of these melamine supports, and screw the plywood to the bottom of the 2x4s, the bottom of the plywood will be level with the top of your form. Check out the pictures and video for more details on this bridge. It is simple to build, but easier shown than explained in words.
Step 5: Mix and Spray the Face Coat
Check out my previous Instructables on GFRC concrete for more details on mixing. However, for this project I made it easier using Fishstone's just-add-water GFRC mix. You mix it by adding 1 gallon of water for every 50 lbs (one bag) of mix. Just adjust the ratio for the size of your tile, factoring in about 10 lbs of mix per square foot of tile (to err on the side of having more than needed). For this table, which was roughly 42”x 20” (plus 16”x18” waterfall), I mixed up 100 lbs in total (between two face coats and backer mix), but only used about 75 lbs. The amount you’ll use will vary depending on the size of your live edge slab, but figure 11 lbs per square foot of table at 1” of concrete, and you’ll be good to go.
Take 12.5% of your mix for the whole project, and mix this first as the first face coat. (Again, see my previous instructables for more sdetailed mixing instructions After waiting 5 minutes and making sure face coat was still runny pancake-batter consistency, I used a hopper gun to spray the face coat, spraying corners first, then sides, then the middle of the form. QUICKLY, use a chip brush to lightly brush the coat in and remove any bubbles. Work a bit harder with the brush in corners to remove bubbles there.
Optional: wait until face coat firms up but is still damp to touch, then spray second layer of face coat. If doing this, make each face coat layer no more than 1/8" (so 1/4" total).
Wait for the face coat to firm up before adding backer coat. You want it to be firm but still wet, so you can't push through it easily with your finger, but it still sticks to the back coat.
Step 6: Hand Pack the GFRC Backer Coat
The timing of your backer coat is important, so make sure your
face coat has firmed up enough (but not completely dried out), before you start your backer coat. Usually this only takes 30-60 minutes,
You can wait until the face coat is ready to begin mixing your back coat, so long as you have everything measured out in buckets (so mixing only takes a few minutes). The process is similar to mixing the face coat, except you add glass fiber to the GFRC bag mix (between 1.0-1.5 lbs per 50 lb bag of mix). Again, see my previous instructable for more details on the recipe and mixing process for the back coat: https://www.instructables.com/id/GFRC-Floating-Con...
After packing the GFRC to 1" (approx), put in your 1/2" foam inserts. Then screw the cross brace to the melamine supports. The bottom of the plywood should press against the foam inserts (if not remove inserts and add more backer mix). Now pack in the rest of the form with backer mix.
Step 7: Grind Down the Underside of the Form
If you like, you can use a trowel after the backer mix has set up a 4-12 hours (depending on temp this can vary widely), and scrape the sides of the form to level it off a bit, but this is optional.
Let it sit for at least 24 hours (36 hours if it is under 70 degrees). Then, if your concrete has gone over the edges of the form, you'll want to use an angle grinder with a diamond cup to grind down the underside, before you remove it from the form. It is important to do it before removing the top from the form, so that you can use the sides of the form as a guide to grind the underside evenly all around.
When grinding, make sure that the underside of the countertop and waterfall don't jut out at all, which would prevent them from being placed flush against cabinets.
Also, grind down the bottom side of the waterfall section (which at the top when in the form, since its upside down).
Step 8: Demold the Concrete, Sand, and Seal
After grinding the underside down to be even with the edges of
the form on all sides, it is time to demold the table top. Just unscrew / and pull the form apart.
If the side walls don't come off easily, use a rubber mallet to gently tap the sides of the form away from the concrete. If you flipped the piece over before demolding, it should be fairly easy to remove the bottom of the form (which is now on top). If it doesn't come off, then use a plastic putty spackle (not metal or anything sharp that could scratch the concrete!) to gently pry the bottom off. If it is really tough, then there is likely a vaccum between the form and concrete. In this case, you can use an air gun attached to your air compressor to shoot air between the form and concrete. This will break the seal created by the vacuum, so you can remove the bottom of the form. Next given the whole service a quick wet sand, by hand, with 400 grit sandpaper. Just sand until you feel it smooth a bit. You'll feel it when you've removed the texture of the melamine, which is all you need to do. Then, apply a concrete sealer of your choice. Just follow the instructions that come with your sealer.
OPTIONAL: before sealing apply a slurry coat (or two) to fill in voids and get a perfectly smooth surface, and then sand off the slurry coat(s) to get a pinhole free surface. Use the mix you set aside earlier, which is the same as the face coat. You can add a tiny bit more plasticizer, if needed. If you do a quick search for "slurry coat concrete countertop" on YouTube, you'll find a number of good videos showing the slurry coat process.
NOTE: If your live edge slab gets concrete on it or gets scratched while grinding, you’ll need to sand it down and re-finish it. If you need to do this (like I did), then do this before you seal the concrete, being careful not to get finish on the concrete when you re-finish the wood.
Step 9: Make the Supporting Wood Leg
You could make the leg opposing the waterfall in many ways. I used three 8/4 mahogany boards, and made mitered rip cuts to join them so they followed the angles at the end of the table. I just used wood glue to attach the three boards and form an oblong U-shaped leg mirroring the angles of the table top.
Step 10: Assemble the Table
I removed the ½” foam from the underside of the table using an exacto knife. I then screwed a ½” piece of MDF to the top of the 8/4 mahogany leg. The ½” MDF will go into the inset left when the ½” foam is removed, so it won’t be visible unless you crawl under the table. I then used Fuze-It to adhere the MDF and leg to the underside of the table.
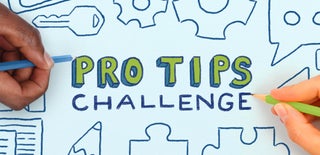
Participated in the
Pro Tips Challenge