Introduction: Wonky Log Cabin Quilt
In January Wisconsin, there are few things to make for a happier life than a live fireplace and a handmade quit to crawl under on a cold snowy night. While there are many designs (traditional and contemporary) that yield beautiful results, the traditional approach of a quilt just covering primarily the top of a bed doesn't work if you truly want a warm, "heavy feel" cover to sleep under. Finding a pattern to cover a King Sized Bed and drop down over the sides meant that I had to design my own, and why not - I want it to be truly a custom job because I wanted it handmade as a bonus!
THIS quilt's design requirements are:
1. Large enough to drape over the entire mattress AND box spring.
2. Large enough for the quit to cover the pillows and be easily tucked under the pillows. in other words, the gap to the headboard cannot show any sheets.
3. Large enough to cover the sides at least to bed rails so that NO mattress/ box spring shows.
4. Natural fiber (cotton) top and flannel underside for warmth
5. Batting to be cotton and of significant weight.
In short... I want to feel the heaviness of this quit for the best snuggle factor possible!
Because of the extreme size and desire to make this truly an original, I designed the entire pattern myself using a traditional "Log Cabin" pattern, but made with a twist (wonky in quilting terms) that resulted in 9 different block patterns.
Supplies
Yardage for the material is dependent upon the exact size you want the quilt to be with an "overage" factor to allow for salvage or waste to ensure you get enough patches to sew together.
Three things make up the "heart" of a great quilt:
1. Design - Making the pattern fit the finished quilt dimensions and how the colors in the blocks sum up to an over all look is vital to a great quilt. Play with the design to ENSURE it is the look you want. There is too much work in actually making the quilt to not have the design come out as you truly wanted. Use graph paper and colored pencils etc. to experiment now versus thinking 'it wasn't exactly what I was looking for.." :o(
2. Yardage - Determine how much yardage you will need of each fabric and how the colors "mix" together to give you a repeat pattern or theme / feel of the entire quilt. There are many Apps you can use to help you calculate how much you need of each "block" or Patch to help you get the right amount. See my raw notes I took to the fabric store on yardage that the app told me to buy for each block. Buy it all at once so you are not running back to the store only to find out it is no longer available!!! Choose fabrics typically of the same blends and of quilt shop quality. Poly based fabrics for me were not an option as they are not traditional as cotton, do not breathe as well, and can be a bit slippery to sew.
3. Sewing Quality - Take your time and sew accurately! Take your time and sew accurately!! Take your time and sew... ACCURATELY !!! Ok, you got it. Making sure your corners come together at the junctions is critical to a great look and ease further down the project. Tolerance stacking of poor alignment will make for huge problems down the road. If you think is was a bad sew job, then rip it out and do it again! This project is far too expensive to feel bad about its quality if you rush it.
Materials -
Moda cotton fabrics - Approx. cost $380.00
Thread - Use the thread your machine seems to run best. For our machine it was Gutterman Brand. It took 2 full spools for the top. For the binding it took 1 spool.
Batting - About $120 - I used 100% Cotton "Warm & Natural".
Long Arm Machine - Rental & Labor $300 because my quilt was so large, I could not find a shop where I could personally rent and perform the long arm quilting process myself, so I had to contract this out. Since a 14 foot arm was required, and these are very expensive machines (upwards of $15,000 and more), very few if any owners will allow others to operate their machines.
So.... all in all I was well over $800.00 for this project - but I now have an heirloom and a project that i can be proud of and others truly are impressed by the undertaking of the project! But with patience, a good teacher and determination, you can do it too!
Iron and Best Press (it's a light weight starch)
Cutting board
Rotary Cutter
Cutting rulers - Clear, long and with markings for aligning straight cuts.
Sewing machine, Scissors, pins, masking tape (for labeling the part numbers).
Step 1: Design It
FIRST OFF - The patterns shown in the pictures are NOT in millimeters but in INCHES. The CAD software I drew up the pattern in had defaults set for metric and I didn't want to change them. Anyway, since the dimensions were in easy "full inches or half inches", it was easier to see and understand the drawing this decimal format versus fractions.
The design is based off a traditional LOG CABIN design. This is an easy rectangular pattern that has only square corners coming together (no points) which makes this a great pattern for first timers like me!
A basic Log Cabin has a nice geometric look to it that can be greatly exaggerated by how the colors are selected and laid out. Gradients of color can really make this look a lot different than mixing up fabrics as I did. But note that my fabrics have all the same tones to them and they play well with each other. In fact all of the fabrics I chose are from the same manufacturer from the same line - making this a very easy and cool way to get the look you want (low risk!).
BUT - a basic log cabin was not for me! I wanted a twist to the pattern so I made it "wonky" style. This means I took the basic log cabin BLOCK, then rotated it to the left just a bit to allow for the most outside "logs" still to have some coverage in the block (approx 8 degrees).
Study my drawings to understand that there are multiple pattern repeat frequencies in this quit.
- Minor Block - 9 total different blocks before it repeats. Hence no two blocks are the same on any row.
- Minor Block Wonky Rotation - Every Other block goes "Wonky" in the opposite direction. No column or row has the same wonky next to each other.
- Major Block - Consists of four different minor blocks - 2 different wonky rotations. Not two alike in a row or column. Identical Major Blocks have a strange repeat pattern that actually overlaps itself. Can you find 7 major blocks throughout the quilt that are identical to the first in the lower left hand corner?
COUNT - Count all of the various pieces needed (part numbers) to make the entire quilt.
Step 2: Fabrics & Cutting
Fabric selection - Use similar fabrics that will have the same cutting and 'pull' behaviors when sewing. As mentioned before, fabrics of the same blends and from the same manufacturer will make this much easier for you to sew.
IRON FIRST - Iron all of your fabric to remove the wrinkles from the bolt. Line up you fabric along the salvage side (where you see the weave surplus - print registration markings etc.) and overlap enough of the fabric to cut this salvage completely off. A little starch will help hold the fabric nice and smooth for cutting.
Fold the fabric back onto itself for no more than 4 layers of fabric. We will cut through 4 layers at a time with the rotary scissors. No block or part number was more than 3.5 inches wide.
Cut for WIDTH -
The intent here is to cut long strips of very precise widths (2 inches for the blocks and 3.5 inches for the sash), then we will cut them to the various lengths needed for the pattern. Lay the fabric onto your cutting mat.
Use the clear ruler guide and cut off the edge of the folded material so it is visually parallel but approx. 1/4" in from the edge as to not leave any salvage remaining on the fabric side to be used in the quilt. Use the rotary scissors and cut the edge slowly and steady, taking care not to disturb the fabric and do this in a long continuous cut. You now should have a long straight cut edge to the folded stack of fabric.
Move the ruler 3.5" inward and parallel to the first cut, to make the second strip cut. repeat the cut and you have your first strip. Repeat cutting the strips until you have enough to make the necessary parts for that color for your quilt.
Cut for LENGTH -
Take a strip and use your rule to align to the cut edge and square it up to cut the very end of the folded strip with a "boss" end that when cut will be perfectly 90 degrees the the edges. Cut the end off (about 1/4" inward). Now relocate your ruler and cut to the required LENGTH for the parts you need for the pattern.
VERIFY your piece part counts as you go along cutting the fabric. Rushing could cause you to over cut and not have the right lengths for the project.
Measure TWICE Cut ONCE! Then COUNT!
Repeat that phrase in your head (Measure TWICE Cut ONCE! Then COUNT!) until done cutting (or if you need a beverage of your choice then stop and save some cutting for tomorrow) No sense cutting fabric while tired!
Group the cut fabric and organize for ready access to the correct color as sizes (see layout table in the photos).
Step 3: Assembly Methodology (Wonky Optional)
The Pattern is very important to get assembled correctly or you will mess up the quilt or have rework!
As the Mandalorian would say... This is the Way:
Assemble a Block, Verify the Block, Sew the Block, Label the Block, Stage the Block.
Assemble the Block - I developed a method of walking around my fabric table picking the parts for the blocks. Each fabric was assigned a position in the rotation ( 1 - 9) see photo. I started with the first fabric and chose it to be part "A" then went to the next fabric and picked part B, then onto the third fabric, and so forth, until I had all the logs to make the first minor block. I arranged those loose pieces on a cookie sheet from the kitchen to lay them out and visually verify the block was correct for the location for where I needed it.
VERIFY THE BLOCK - This is in large capital letters so you do not have rework or waste fabric. If need be, go through the pattern and list out each of the 64 minor blocks on a sheet of paper as a reference check for each time you pick fabric from the staging table. If something doesn't match up - then you have a chance to figure it out and fix it before you sew it together!
Sew the Block - Each seam is for a 1/4" seam allowance. I started in the middle of the block (part A) and then aligned up to first two pieces of fabric (faces together) and machine sewn along a 1/4" set up guide at the foot of the sewing machine. This was set up with scrap fabric first to ensure I had a solid seam of exactly 1/4". This is important so you do not get error build up over the entire assembly. Open the two sides of the sewn seam and press them flat on the underside. Take part B now, and align that side of part B where it belongs on the first pieces you just sewn. Again 1/4" seam, and press flat on the underside. Keep checking for how the sewn pieces align on their sides. This should always align up on each side and overages or under sewing should be remedied as you sew. Use of pins is highly recommended to hold the pieces while machine is swing them together. Rotate this assembly and add part C and so forth until all the logs for Block 1 is complete.
Label the Block - Label this block with masking tape or a numbered post it as pinned to the block to ensure it is not mixed up when aligning the proper sequencing of the minor blocks. Note this is a perfectly square block (not wonky).
Stage the block - Lay out the blocks or stack them in the order in which the Major blocks will be sewn.
I would suggest to sew ALL 64 minor blocks before cutting for wonky.
Wonky cutting is OPTIONAL. I just wanted another dimension to my quilt so I decided to cut half of my blocks on a slant to the right and half on a slant to the left. To do this I made a custom square clear ruler out of acrylic sheet 1/8"thick. It was exactly 10.5" by 10.5" so the finished block when sewn would be exactly 10" x 10" . I basically placed a non-wonky cut block on my cutting board and overlayed the acrylic square on top of it but at an angle to match the outer most log to run to a point on each of the four sides. I then used the rotary scissors and cut the block square. Then I assembled the minor blocks into major blocks (4 minors each).
Step 4: The Sandwich (Backing - Batting - Top)
When assembling the finished quilt, there are three layers. Backing - the back fabric, Batting - the snuggly soft center that adds warmth and weight and the beautiful Top! This is called the sandwich. It's important that the batting is larger than the top and that the backing is larger than the batting. This is called overage and allows for shrinkage that naturally occurs as the sandwich is quilted together. It also allows you to see all layers while quilting them together.
Backing - once you have selected a fabric, you will need to cut it and then sew those pieces in a manner to create a square that is 10" wider and longer than the quilt top. In this case the finished backing must measure at least 137". This is called an overage and allows for shrinkage that naturally occurs as the sandwich is quilted. This required 16 3/8 yards of backing material which was cut into three sections of the same length (slightly over 4 yards) and sewn together side-by-side. Press, gently fold and set aside.
Batting - for most quilts you can purchase pre-cut packages that meet the need of the quilt size. For large or uniquely sized quilts you may need to piece patting together to obtain the desired size. In this case I used Warm and Natural from a role that is 90" wide. I cut one strip from the role, 135" long (135" x 90") and then a second of the same length that I then cut in half lengthwise to 45" (135" x 45") I joined the pieces by butting them together and using a zigzag stich across the butted edges, so as to avoid overlapping batting within the quilt which would produce a bump in the finished project. When complete the batting measured 135"x135". Press, gently fold and set aside.
Top - your top is complete! Press, gently fold and set aside.
Bring the sandwich pieces to the long arm quilter of your choosing. They will work with you to select your preferred quilting pattern from many choices (from traditional to modern) and they will help in choosing a thread color for the quilting stitching.
Once the quilt pattern is chosen, the quilting process of sewing the sandwich together begins. The three layers are fastened to a machine called a long arm which is basically a very large industrialized sewing machine that sews through the three layers and creates a continuous stitch pattern in the design you chose. Often this is a computer controlled process and the machine does most of the work with monitoring of the process by the user. Smaller and less automated long arms are operated by hand and the pattern is worked by the operator. In either case the intent is to bind the three layers together all the way out to the edges with a uniform stitching design that is centered over the quilt in both the longitudinal and latitudinal directions.
To finish this step we must trim the sandwich to the final dimensions as determined by the top. In other words, trim off the overage to be exactly sized as the top!
Once quilted and trimmed , the final step can finally start!
Step 5: Binding
Cut the fabric for the binding into 2.5 inch strips. This will be sewn into a very long "spool" of fabric that will "edge" the quilt or cover the trimmed edge from the previous step.
You will need a finished spool of at least 520 inches to cover the perimeter with some allowance. It was calculated as 127" on a side rounded up to 130" and multiplied by 4.
Fold the entire spool in half (wrong sides touching - finished sides out) and press it smooth.
The binding will have hidden seams along the entire edge for the entire perimeter. To get this result, first lay the binding on top of the quilt with the finished side of the binding to the finished side of the top. Align the edge of the binding to the edge of the quilt and pin the two pieces flush on the edge. Then sew the 1/4" seam of the binding to the top of the quilt, pinning and sewing as you go around the perimeter. Once sewn, then flip the binding over to the rear and hand sew (blind stitch the binding) to the backing. I prefer to use a mitered corner to give it the finished look such a project deserves. There are many videos and online resources that show this technique well that I would suggest you try.
This is ALMOST DONE! Last step ...
Step 6: Breaking It In!
Take the quilt to a laundromat and bring some color catchers, your favorite detergent, and fabric softener. Color catchers are a product that is a "sheet" product thrown into the washing machine with the quilt that captures the loose dyes that comes off the new fabrics and keeps the dyes from settling back onto the quilt ruining your good work!
This is a must !
Use a large commercial washer as to fully wash the quilt well and get it really "loosened up" in the washing process.
Wash the quilt then dry it on medium heat as to not risk burning the fabrics. When done your quilt will have a nice crinkly look that gives your quilt that extra comfy feeling on that cold January night!
Last step... find someone to cuddle underneath your new heirloom!
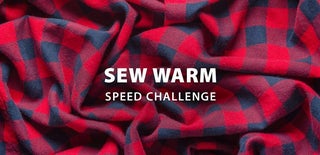
Participated in the
Sew Warm Speed Challenge