Introduction: Wooden (Floating) Windowsills
In this article, I will show you how I go about making wooden windowsills. It is quite easy and can be done with basic woodworking tools.
I will show you three different sills that I have made recently. Although the wood material varies, the process itself is the same. As a bonus, I will teach you how to make a floating windowsill - a little idea I came up with to increase the useful area in one of my tiny rental apartments.
If you prefer a more visual approach I suggest you take a look at the two build videos.
You can also find me on Instagram! Let´s get started!
Step 1: Tools and Materials
The timber I have used for making sills varies. I mostly use finger-jointed hardwoods like birch, ash or oak. These are most common in my area (Estonia). I really love the look of hardwood when it is finished with clear oil or varnish plus it stays beautiful for a long time. I have added a photo of what a finger joint looks like. A "sheet" of this material consists of many small sticks meaning the price can be quite low. I personally do not mind the "multi-tone" look that the different pieces create, but some people do. Of course, I would prefer to use one single piece of lumber but as of right now I really do not have the required tools for that (jointer/planer). The finger-jointed board comes already planed and sanded and in my case even prefinished. I paid 40€ and got four sills out of it. Talk about cheap!
But do not worry if you can not get your hands on some nice hardwood. As my experience shows windowsills can be made out of pretty much any wood. For example, I used 2X10 pine timber to make three sills in one apartment. We opted to use pine mainly for financial reasons and also because the sill would get painted. I bought a 6m/20ft piece of 2x10 making sure I would get the straightest and least knotted beam.
Tools:
- Circular saw (plunge saw)
- Miter saw
- (Jig saw)
- (Router)
- Personal protection equipment
- Measuring and marking tools
- Silicone gun
- Painting tools
Materials:
- Wood
- Silicone/caulk
- Varnish, oil, paint, etc.
- Wood glue
Step 2: Preparation
The first step is to prepare the opening for the sill. In the newer apartment, where I also built the walls, this meant just cleaning the area from dust. I knew that everything was plumb and square so no additional work was needed.
In the older apartment, I had to first remove the old sill, clean out a lot of gunk and old insulation, flatten the surface and clean the corners.
Be careful when rumbling around a window. I had quite a few close calls with the glass when prying the old sill out.
Step 3: Measure
Probably the most important step -take your time. Here in Estonia, we have a saying "Measure 9 times, cut once!"
It is a good idea to leave the sill just a hair short so it would not be so tight fit and damage the walls (especially gypsum). The cracks will be caulked anyway.
I usually go about first cutting the board to length so I can butt it against the window and then mark and cut the width. Most likely the window and the wall do not run parallel so the cuts have to compensate for that.
Step 4: Cut
Use some of the woodworking magic to turn the lumber into the desired shape! My choice of magic wand for such purposes is almost always plunge saw with a guide rail. I never fail to get straight cuts with it.
If I am doing a sill with an overhang (which I almost always do) I also use a jig saw to remove the small corner. I still try to make the majority of the cut with a circular saw as it creates a much straighter cut. The jig saw blade tends to wander especially when the wood is over an inch thick (25mm).
As you can see in the last two photos I also cut away the one edge facing the window. This was so it would fit with the profile of the window better. I think it is meant so that you plane the whole board to that thickness but once again I still do not have a thickness planer. I am super happy with the result as the sill ended up being perfectly against the window and no caulking was needed.
Step 5: Install
To install the sill I just glue it down with whatever adhesive (in a tube) I have. Most likely it is a leftover of some sort of silicone. I have also used fast-drying glue but I can't say I noticed a difference. To me, it seems that a flexible adhesive would work better because of the wood movement but I could be wrong.
If the wall is not so perfect I like to use expanding foam and shims in addition to the silicone. The silicone itself I also apply in blobs so to create support pillars. Whatever gets the sill to be firmly in place. Let's just hope no one has to remove these sills any time soon....
Step 6: The Floating Sill
No for the fun part - the floating sill. The idea manifested to me when I was looking out the window one day. I got annoyed that the bottom sill was filled with plants whatever else was on there. I figured it would be so much nicer if the ornamental stuff would be higher up not obstructing my view. And so the floating sill came about.
The process of making one is quite similar to a normal sill. The only difference is that both ends need a groove routered in them. I used my palm router with a fence for that.
Step 7: Installing the Floating Sill
Then I just cut a piece of plywood that would fit in that groove. No to lose and not too tight - just so that it slides in and out nicely but does not bind. It might take a few tries (it took me one because I am a pro 😁 ). It is much easier to do on a table saw.
The little block of plywood needs to be then attached to the window jamb. In my case, the jambs were made out of gypsum but as I knew there was wood behind it I used long enough wood screws. I there was no wood I would have used dowels.
To mark the location of the block I made a little jig from the offcut of the sill. Little water level to make sure it was plumb and voila! If the exact height of the sill does not matter then you can just use a longer water lever or a laser level to mark the locations. I was aiming so that the top of the window divider would match up with the top of the sill.
To install the sill I just added a few tabs of Gorilla glue on top of the plywood block and slid in the sill. This method does not damage the window in any way and the sill can be removed somewhat easily. Alternatively, a screw or a small nail can be used as well.
Step 8: Sanding and Finishing
This probably does not need too much explaining?
All the imperfections were filled with matching colour wood putty and the sill was sanded with 120 grit paper. On the prefinished sills, I just sanded the edges. Of and by the way it is so much easier to sand the sill before installing it. Hopefully, you read the whole article before making your own sills!
Finishing I usually like to do once installed. Taping all the surfaces that you do not want to varnish is a good idea as well.
Step 9: Be Creative
Now, what if you run into problems while making a wooden sill? Easy - improvise - adapt - overcome!
For example, I managed to crack the wood while installing it. Luckily it was the sill that would get painted. So I just opened the crack up a bit and squeezed in some Gorilla glue. Once dry, whatever was left of the crack can be filled with wood putty and once painted you could not even tell that the carpenter messed up.
As I have mostly made sills for small rental flats I usually run into problems where other objects want to interfere with the sill. In one case the fridge was right next to a wall and when opening the door the sill got in the way. Instead of doing a silly cutout in the sill, I opted to leave out the overhang altogether. It was a bit different from the sills I have done before but think it does not look too bad. The third photo is before I cut it to the final width - you can see that the fridge door can not open. The final overhang was maybe 2 mm - just enough for nice caulking.
On two other occasions, I have run into a problem where an oven door cant be opened. This I fixed with a simple cutout. Luckily both times the height of the sill was pretty OK and I did not have to remove too large a chunk of wood.
Step 10: Caulking
And do not remove the tape just yet! It might still be handy when caulking. It keeps the majority of caulk off the wall and greatest a nice crisp line afterwards.
I used to be a soapy finger kind of caulk guy but boy was dumb! The key is to use a popsicle stick to get super nice caulking. I modified the stick so it could lay flat on the sill and I think the results speak for themselves. I mean, of course, it could always be better but compared to where I used to be this is day and night! I am so happy with the results!
Step 11: The End
And that is it! A sill that looks good and is tough. And best of all you made it with your own two hands - priceless!
If you have any questions, suggestions or ideas let me know in the comments. I would love to hear what you think!
Do not forget to watch the video to get a better understanding of the process.
If you are interested in my work be sure to subscribe and find me on Instagram!
Take care!
Andu
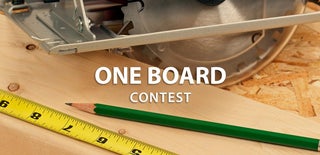
Participated in the
One Board Contest