Introduction: Collapsible Spring Clamp Camera Mount / Tripod
I needed a small and easy-to-use device with which to mount my phone on something so I can take well-framed shots that include me. A common and effective DIY solution is a spring clamp to which a 1/4" bolt has been installed. It's small, and quick to mount and dismount. There are in fact several Instructables with this very idea. The main limitation with it is that it can only be used where there is something horizontal to clamp on to because the bolt is on the top jaw of the spring clamp. The camera ends up too close to whatever it is attached to, so the places where it can be used are limited. Other models address this issue by adding a flexible extension to hold the camera, but the result is too bulky for me. And because of the weight added by the extension, they require a bigger and stronger clamp.
This instructable improves upon the design of spring clamp camera mounts by adding a few components to allow it to hold on to a lot more things. And when there's nothing to clamp on to, it turns into a tripod. I tried not to use any 3D printing but I'm guessing these days most people have access to a printer anyway. The result is a stable, versatile, cheap and definitely pocket-sized mounting system for a phone or action camera.
Step 1: Materials and Tools
Materials:
- A 4" long plastic spring clamp. The jaws should open at least an inch wide. A smaller one would limit where it can be attached to, and a bigger one won't fit in a pocket. A metal one might be too heavy. Mine is a cheap one sold in a multi-sized pack. I also found a very similar one at a dollar store sold in packs of four.
- Two 1" M4 bolts. I needed hex-head bolts, and this type was the only one I found. One will replace the short original bolt that serves as the axle of the spring clamp, which in my case turned out to be also an M4 so I was able to use its nut. You can use another similar bolt as long as it has a hex head and its nut fits in the cavity on the side of the spring clamp.
- An M4 wingnut. With the other hex head bolt, it will be used to tighten the ball-and-socket joint. You can also use a thumb bolt with hex nut of similar size if you can find one.
- Two metal washers for the M4 bolt. One of them should be less than 1 cm in diameter; the other can be slightly wider.
- A 1/4"-20 bolt about 1-1/2" long. This will be the mounting bolt for the camera and will be attached to the socket. There are several options to go about it.
- Option 1: a plastic 1/4"-20 bolt, the kind used for toilet seats. It usually comes with a thumb nut. It's a good option because you'll need to cut off the head to attach it to the socket.
- Option 2: You can use a metal bolt but it will be much harder to cut. Good thing I already had one from a failed project.
- Option 3: If you want to avoid cutting a bolt, get a regular 1/4"-20 hex-head metal bolt, then use the two-piece socket 3D model that has a cavity for the head. I included a model for that. The disadvantage of this option is that it results in a bulkier socket assembly.
- A 1/4"-20 thumb nut. This will be used to tighten the camera mount. Option 1: a wingnut. If you chose the plastic bolt, it usually comes with a plastic one. Option 2: an ordinary hex nut, then 3D-print a handle for it. I included a model for that. Option 3: a knurled nut from the head of a mini-tripod, which is what I used.
- Strong rigid glue, like epoxy
- Thin (1/8" thick) foam pads or rubber strips (like from an inner tube) for lining the spring clamp jaws
- Scrap 1.75-mm 3D filament or similar material, about an inch long. This will be used as a hinge pin.
Your action camera or phone holder should have a standard 1/4" camera mount.
Tools:
- A 3D printer and filament. If you don't have one, the parts should cost about $5 at a commercial printing service.
- Medium grit sandpaper and needle files
- Something to cut the bolt with, if you choose this option
- Eye protection -- you should know this already.
Step 2: Print Out the Parts
The following parts are to be printed:
- swing arm
- third leg
- sliding spreader
- ball
- socket
- knob.
PLA or ABS will do. I attached all the STL files needed, including options for a couple of parts. I also attached a model for the nut handle if you need one.
There are two options for the ball. It can be printed in one piece, but I had problems due to its overhangs, so I created another model with two halves that are glued together.
The socket also has two versions. The first is what I used, which is in one piece. The other one is split in two, for when you are using a bolt with its hex head intact.
After printing, sand away excess material and burrs. Don't sand too much -- the parts need to fit tightly. And don't smoothen the ball because it will work better if it is a little rough.
If using the 2-part ball, use a caliper to check if assembled ball is spherical after gluing the two sides together. It's OK if it's off by a bit as long as the socket can hold it evenly in any orientation.
If using the split socket, just put in a lot of glue inside the cavity where the bolt goes. The model comes with a ring that goes around the top of the socket to reinforce the bond. Remove any excess glue along the gap on the side of the socket and inside the socket itself.
Step 3: Assemble the Swing Arm
Slip on the knob for the M4 bolt, followed by the small washer, then the swing arm, then the other washer.
Take the spring clamp and loosen its bolt until the nut comes off. Don't remove the bolt, as this will dismantle the clamp and set loose that pesky spring. Instead, use the new longer bolt to push the old one out. If needed, use a screwdriver to unscrew the old bolt but make sure the new bolt follows it as it comes out. Then put on the nut.
Note that the flat side of the swing arm should be towards the clamp, and channel side out.
The sliding spreader goes on the arm. The spreader itself should be over the flat side of the swing arm (not the channel side). That the piece is asymmetric, so make sure the spreader side is towards the axle end of the arm, not the ball end.
The third leg goes into the channel along the main arm. Make sure that the holes for its axle lines up with the hole on the arm. The ball sites at the end of the swing arm. The ball should be over the flat side of the swing arm, and its holes for the axle should line up with the others.
When the holes on the swing arm, third leg, and ball are lined up, insert a piece of 1.75-mm filament into the hole to serve as a hinge pin.
Step 4: Test the Swing Arm
Try moving the spreader up and down the swing arm. It should be easy to do that. If not, sand the parts that are in contact. Don't sand too much that the spreader can slide along the arm on its own.
Move the spreader right next to the ball, then test if the swing arm can rotate all the way without the legs and jaws getting in the way. If they do, we have a problem. If the legs are a bit too long, you might be able to trim the ends. If not, the device will still work, but you might not get full functionality. Consider getting a smaller spring clamp.
Test the tightness of the third leg. The leg should sit snug in the channel, but you should be able to fish it out with a fingernail. If you can't, you have to sand it down a little. There are a couple of bumps on the channel designed to hold that leg in -- those bumps can be trimmed if needed but don't sand them all off.
When satisfied, glue the ball and the ends of the pin on the arm. For the pin, you can also just leave a little out, then melt the ends flat with a soldering iron or the tip of a glue gun. Avoid getting glue on the sliding spreader or on the third leg.
Step 5: Build the Socket Assembly
The camera is mounted on the bolt whose other end is attached to the socket.
If using the headless bolt: test how far the bolt can be screwed in. You can use pliers to hold the middle of the bolt to twist it in, but avoid damaging the threads at the ends of the bolt. If the hole is too tight, do not force the bolt in or you might crack the socket. Use a tap to cut more of the thread, or patiently screw and unscrew a metal bolt in a few dozen times to wear down the thread. You can stop when 1/4" of the bolt goes in. When it does, glue the bolt in place.
Check the inside of the socket, and remove any burrs. Then carefully cover the ball with the socket. It should be a snug fit, but it should still be possible to swing the socket assembly around the ball to any position. Sand or file off any excess material on the socket or on the ball that gets in the way.
Attach the phone using its holder to the mounting bolt. When the wingnut on the socket is tightened, the phone should be locked in place. It should also be possible to slightly reduce the tightness such that the phone's angle can be changed but will stay in place without slipping when it is released.
Step 6: Finishing Touches
Take a strip of foam pad the same width as the jaws of the spring clamp, then determine how much will be needed to completely line the jaws when they are fully open. Glue the ends of the strip to the two swiveling pads at the jaws of the clamp. The foam pads will improve the grip, protect surfaces, and prevent the swiveling pads from moving about too much.
I also reduced the profile of the knurled nut by cutting off two sides. I thought it was plastic when I started cutting it with a hacksaw. When I found it was aluminum, I ended up using a rotary tool and cutter to finish the job. I should just have printed out a nut handle.
Step 7: Start Using It
Check out pictures of how the device can be used to mount a smartphone or action camera.
Step 8: What Does This Third Leg Do?
Release the third leg by sliding the spreader out of the way to its Home position deep into the swing arm. Move the spreader to the other end of the swing arm beside the ball. Rotate the arm so that it ends up over the jaws. Slide the separator down so that the jaws can clamp on it, thereby immobilizing the arm. Swing out the third leg as far as it will go, and voila, it's now a tripod!
When using this mode, make sure the camera mount is fully vertical and the socket is locked tight. You'll need to balance the phone on its holder. Obviously this mode should only be used when the legs can rest on something level and unmoving, and should not be used when it's too windy.
Step 9: Pocketing It
To fold the device, take off the phone/action camera. Swing the arm back between the legs, slide the spreader home, then tuck in the socket assembly into the space between the legs.
When folded, device is about 4 1/4" long and about and inch thick. The added components add just an inch to the length of the spring clamp and 1/2" to its thickness. It fits in a shirt pocket without pulling down on it.
Step 10: Notes
1. One thing to remember when setting this up is to wait a moment to make sure that everything stays in place before you let go of it. If the clamp slips, move it to another location. If the camera tends to swing down, tighten the socket.
2. This mounting system is designed for smartphones and action cameras. Take care when using a point-and-shoot camera with it. Do not use it on professional cameras.
3. One tip that makes levelling the phone easier is to place it on its holder such that the phone's center of mass is right over the mounting bolt. This center may not be at the geometric center of the phone, so you need to be aware where this is. When the phone is horizontal and supported right under its center of mass by the bolt, it is in balance and therefore has less tendency to fall to one side. This reduces the required tightness on the socket to hold the phone, allowing fine adjustments to be made to its orientation. When the phone is not balanced on the mount, everything needs to be tighter and harder to adjust.
3. Push the spreader in between the legs to lock in the clamp's grip everytime. I should have printed this piece in a brighter colour, because I keep forgetting to slide it out again.
4. The knob on the bolt axle lets you tighten the position of the swing arm. You can in fact hold the swing arm horizontal with it even without the help of the spreader. But it has another purpose. When the spring clamp is attached to something vertical like the side of a shelf, that handle is pushed into the shelf and increases the leverage provided by the jaws. A longer leverage distance would be a good idea, but I couldn't come up with a simple way to make it fold. Suggestions welcome.
5. A water bottle can be used as a tripod using this. But I don't recommend it because the footprint of a water bottle is too small. If you have to, don't use an empty bottle.
6. If you use a higher quality spring clamp, you'll find its jaws to be harder to open. It's a good feature to have so if that's not a problem for you, go for it. They do tend to use a rivet rather than a removable bolt as an axle, so it might take some effort taking it apart.
7. There will be setups that will prevent the smartphone or camera screen from being viewed, such as when it is facing a wall. This is not a problem with newer action cameras, which can be linked to a smartphone for remote viewing and shutter control. You can also do the same thing with two smartphones using an android app called Bluetooth Remote Camera.
Finally, if you build this: May you always find something to clamp on!
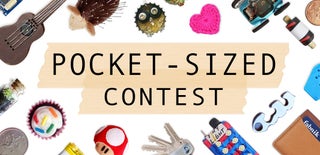
Participated in the
Pocket-Sized Contest