Introduction: Borderlands 2: Maliwan Hellfire Foam Prop
Greetings Vault Hunters!
I have another Borderlands build! This time it's my favourite weapon from Borderlands 2: The Maliwan Hellfire.
It has a really unique design and it looks incredible in the game, and there are so many versions of this design too with different paint schemes and alternate body parts, allowing for tons of combinations!
In this build we'll be making this gun out of EVA foam: An amazing material, very user friendly to work with and extremely light, perfect for conventions! You don't need workshop tools to make this either, just a place to sit down with some standard hand tools, a place to paint and a Dremel.
Let's get started.
Step 1: Materials
Materials:
- EVA Foam [10mm]
- 5mm PVC Sheet
- 1mm Styrene
- 5mm Styrene tube
- 20mm PVC pipe
- Nylon Webbing + Buckles
Consumables:
- Contact Cement
- Superglue/Epoxy
- Painters/Tamiya paint
- Neodymium Magnets
- 120, 240, 400 Grit Sandpaper
- Flexible Filler
- PVA glue
Tools:
- Dremel [various bits]
- Utility/Snap/X-Acto Knife
- Heat Gun
- Assorted Paint Brushes
- Needle files
- Pipe Cutter
Paint:
- Acrylic pack
- Black & Light blue paint markers
- White & Blue Spray paint
- Plasti-dip (black, white or blue)
One last note: Safety gear is recommended, especially for neodymium magnets, contact cement & Plasti-dip; wear goggles & a respirator!
Step 2: References
Here are the templates for the build. The detail template is for detail lines, required late into the build, the foam templates shows each section divided and the mag/rail templates are a mix of foam and plastic parts. Download the PDF's and print at 100% scale! You'll want to add overlap to print in sections.
Before diving into this project, it's worth gathering extra images online of screenshots and renderings, especially if you paint your prop an alternate paint scheme or more drastically, if you want different body parts to work from.
Step 3: The Core
Despite this being a foam prop, the very first part we make is actually made of 5mm PVC sheet. This will be the spine, adding rigidity and structure to EVA foam. Without it, the foam would bow like a, um... bow.
For the foam halves, It's easier to stick the PVC onto a large piece of EVA foam with contact cement and trim off the excess. Use 10mm foam for both sides with the texture removed with a drum sanding bit. Final thickness should be 25mm.
When the excess is trimmed, smooth over along all edges with a rotary tool and a drum sanding bit.
Step 4: Main Body Parts
Each body piece requires a stack of 2 X 10mm chunk of EVA foam, stuck together to build up the correct thickness. Like the core, it's easier to glue 2 chunks together and cut to size.
To reduce mess [rotary tools throw material everywhere] trim off excess first; it'll save you time and clean up.
Following the peak line, taper out both ends, keeping the curve consistent with a bit of roundover. This will take a couple passes, so don't try and get it perfect the first time! It's also advised to take off less material, rather than more; adding foam back on is much harder than removing it.
To smooth out foam, wet sand with 240 and 400 grit, and pass over it with a heat gun [let it dry from wet sanding first]
When the top and bottom chunks are close to shape, contact cement them together. The left side needs a hole cut out for the magazine. I used my knife to remove quick material and my rotary tool to its final dimension.
Step 5: Styrene and Magnets
On top of using PVC, we're also using styrene plastic. By all means, plastic isn't 100% required and the whole thing can be made of nothing but foam, but some areas benefit greatly from this addition.
For the visible parts on the top of the prop that will become the rail, I wanted a hard-edge, mechanical like appearance and that's tricky with foam, 1mm styrene is perfect for this. We can also take advantage of this addition with the introduction of magnets!
Before cementing down my styrene strips, I embedded neodymium magnets into the gun for parts later on in the build. These magnets are strong enough to pull through the styrene layer.
A disc of styrene with the same diameter of the hole on the left side of the gun is added to the cutout.
For a sharper looking front opening, roughly cut out some trenches (doesn't have to be perfect) and stick more styrene.
Before gluing on the body panels to the core, I cut holes for some massive 20mm neodymium magnets to embed. This is completely optional but it's really cool what this will be used for later... [Note: Handle these magnets with extreme care, they're very powerful!]
Step 6: Stock + Blending
Just like the main body panels, the stock pieces are rough cut, shaped and refined with sandpaper, though this time the EVA foam is thick enough without stacking.
The hole where your thumb goes requires a lot more work and finesse. Depending on your thumb size you will have to modify its diameter and taper; I kept removing material with a tapered grinding stone bit to get a smooth, comfortable transition.
When these pieces are glued on, you can begin to blend them together. The seams will be dealt with later, but this is the time to get the gun into its final shape.
Step 7: Detail + Sealing
Once you're happy with the shape and smoothness of your foam, it's time for detail lines. Transfer the detail lines from the references provided.
A really cool trick to get sharp grooves like these is to score the line with a knife and gently blast with a heat gun. The heat causes it to split slightly, revealing crisp defined lines.
For round details, twist a copper pipe into the foam. The pipe cuts through with ease. The trench on the right side of the gun was made with a ball rotary bit in my Dremel.
To deal with pesky seam lines and errors, flexible filler is all you need. With a wet finger and a paper towel, apply the filler to all of your seams and smooth out with extra water. The key here is to use just the right amount of filler. This stuff cannot be sanded with clean results, so go easy on how much you use and apply more if necessary.
When every seam is filled and all details are done, seal the entire prop with standard PVA glue.
Step 8: Paint Base
Foam is quite tricky to paint because of its porousness and flexibility; paint tends to flake and wrinkle without prep work. The PVA glue applied in the last step acts as a base for the following paints to bond to. I used Plasti-dip to get a wonderful, tough wearing base for the gun. I applied 2 heavy [but not dripping] coats of Plasti-dip and let it set. [Note: Work with Plasti-dip in a well ventilated area & wear a respirator!]
To get the right blue base, I sprayed the whole prop with Montana blue. After the blue base coat, white paint follows. Tape up the stripe border and spray a few coats of white until the blue is completely gone.
Step 9: Paint
It's time for paint! This stage is all done with acrylics and paint brushes. This can be done with spray paints or even an airbrush if you have the supplies.
Mentioned before, you'll want to gather references for your chosen paint scheme!
To start, all yellow parts need a white base to paint on; this can be done during the stripe stage, but I had to fix a couple errors I spotted. Follow up the white with a yellow coat and a dark yellow on top to mix up the colour a little. Paint the handle and trigger grip grey.
To accentuate the cel-shading, most edges need highlights. Using a lighter shade of blue, paint lines across the edges; again, use your sourced references to see what needs highlighting.
When highlighting is done, the fun part can begin; cel-shading. With a 0.7mm paint marker, draw all the black lines around all the details. This magic step transforms the prop into a whole new thing!
To bring out even more highlights, an even lighter shade of blue can be used to mark lines. I used a 'Montana shock blue light' marker pen for this.
The last parts are the orange, red and grey highlights. Getting a gradient effect requires a few shades of your desired colour, and adding light washes over certain areas to break up and blend the shades.
When the entire gun is painted, string it up and clear coat!
Step 10: Magazine
The gun body is complete, but we're not done! We got more pieces to work on.
The magazine is made exactly the way the gun was made, albeit, far quicker and easier.
The magazine is made of 2 blocks, one 100mm wide and one 115mm wide, glued together with contact cement. The top piece is sculpted with a Dremel to round the surface. The lines were etched with a knife and expanded with a heat gun, followed up with PVA sealing.
For paint, a white base coat is best. The stripe is taped up and the orange is applied in washes for a gradient effect. This is followed up with yellow and a dark yellow wash on top to break up the colour. Last main colour on the surface is a blue that matches the base colour of the gun. Apply a couple layers for a strong, bold blue.
The last part is again, the best part; more cel-shading! Follow the reference and outline everything that needs outlining. The paint marker can also be used to paint in the black ring around the orange. It's crazy how different it makes the piece look; it's like a makeover!
When all the paint is dry, follow up with a clear coat.
Step 11: Plastic Parts. Pt.1
There's a few pieces on this gun I felt could do with some extra rigidity and refinement, so the following pieces are mostly made from more 5mm PVC sheet, since it's already on hand. Mentioned before, these pieces can be made with regular EVA foam, just as everything else has. It's up to you what you use.
The front top barrel is made from 2mm styrene with a magnet in the middle. This is how these pieces will attach to the gun (remember the magnets we included?)
The rail is made from PVC, stacked to 20mm thickness, cut out with a coping saw and refined with body filler and putty. Another magnet sits in the back of the rail to attach to the gun later.
The front sight is another 20mm stacked block. For the orange sight, a 5mm hole is drilled all the way down and the block is shaped. Same approach for the back sight, though this hole is horizontal and 18mm wide.
Lastly, the rear iron sight are made of single chunks of PVC and shaped; these are the easiest to make.
Step 12: Plastic Parts. Pt.2
There's still more to do on these parts, let's keep going!
The top of the front sight needs sanding down until it hits the halfway mark of the diameter. For the orange sight, I'm using a 5mm styrene rod, cut to the angle and blended to shape. This piece will be left separate and painted individually. The back sight gets more shaping, adding a slight taper, thinning out at the front.
I made the back sight round piece with a piece of dowel with Milliput to thicken it and pushed through a PVC pipe to get a consistent cylinder. This is not a conventional way to make this kind of piece but I didn't have a piece of pipe the right size; you gotta use what you have on hand ;) I would advice just buying a piece of 18mm pipe :D
To go with the top barrel, the under barrel is made from 20mm PVC tube and shaped with a drum bit, cut quarterly. [every 90°]
These main parts can finally start to be glued together. Glue the under barrel to the top barrel and the sight pieces onto the rail. The rear iron sight needs a small block of PVC glued in between.
Base coat the rail, barrels, rear sight and trigger grey. Glue the barrel and rail together and wash over with Nato Black. Paint the orange sight, well... orange, and the backsight piece white, blue and orange on the sides.
Step 13: Magnetic Harness [Optional]
Remember the giant magnets embedded into the gun? This is what it's for. Video game weapons always seem to float on the players back with no visible straps; this is how you can achieve that effect! It's also crazy convenient for long days at conventions and photoshoots.
The 20mm magnets in the gun are so strong they can be held up with a single 20mm magnet; we're gonna use 2.
Following the template, cut the pieces out and assemble. I used 1 layer of 2mm styrene as the core and 4 layers of 2mm self adhesive foam; 2 layers on each side. Cut a length of webbing that can wrap around your body from the front, over the shoulder, and down the back.
Add a few extra inches and cut it in half. The extra length is for attaching to the mount with contact cement and for adjustments. Add buckles to each corresponding strap.
[Note: the measurements provided in the layout are lengths that fit my proportions. Everyone is a different size, so make yours fit!]
Cut another strip that threads through the side, wraps around the side of your body and overlaps the main strap. Mark where it overlaps and loop a piece of webbing with a buckle and glue in place with more contact cement.
You'll have to do a lot of tweaking to get the harness to sit comfortably on your back, so make sure you have spare webbing to allow for adjustments.
Attachments
Step 14: Complete
Here it is! All done, and ready to roll.
Weighing in at a delightful 670 grams and being made from soft materials it is the ideal con safe prop, and if you ever tire from holding it, you can sling it on your back over your costume with no fuss!
The magnet harness has so much potential for other projects and I'm glad I got to exercise the idea for this prop; you'll be seeing more of this kind of innovation in my future projects. The magnets are so strong in the gun they can connect with metallic objects like signs or containers!
It's taken a long time to complete this prop and I'm pleased with the outcome. I hope you guys like it enough to try it out for yourself, or make your own props using this method. Either way, I'd love to see what you guys come up with.
If you're in the mood for more Borderlands, I've got my Claptrap build right here.
And lastly if you liked this build, please consider voting for this build in the Game Life Contest :)
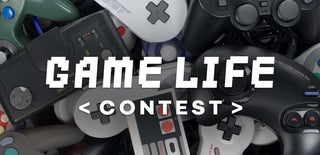
Second Prize in the
Game Life Contest