Introduction: Chonky Hall Table
My sister, Laura, didn’t want anything “fancy” or overly expensive for a hall table in her new house but needed to fill a space. Of course, “not too fancy” quickly became “this specific thing I found on Pinterest”.
This isn’t my original design - I don’t know whose it is, I am just working off the one super low resolution screenshot I was provided. The dimensions are also designed to fit her space, not necessarily the dimensions I think would be best for most cases - this is a fairly narrow and chunky table.
If you do end up making something like this for yourself, I'd strongly encourage you to make it 100-150mm (4-6") lower than what is listed in the plans.
Attachments
Supplies
- Hardwood (see cut list in PDF for quantities)
- Glue (I used PVA and liquid hide glue, though PVA is fine for the whole lot, just can be a bit more time sensitive!)
- Finish
- Z Clips & Screws
Tools
- If you buy rough sawn material, you'll want the "standard" combination woodworking machines for milling lumber - table saw, surfacer/jointer, planer/thicknesser.
- Sander
- Router with a 1/8" round over bit
- "Joinery tool" - I used a domino, but this project is perfect for dowels. The plans (PDF, attached) have layouts for both dowels and dominoes
Step 1: Cut List
Instructables doesn't allow table formatting, please see the attached PDF/plans in the previous step.
Step 2: Milling
If you're using rough sawn material like I did, you'll need to bring everything square. First, cut everything to a rough length (its easier to joint a shorter board than it is a long board!) - tabletop pieces, long stretchers, and then leave the legs + "feet" together because the feet alone would be too short to joint easily.
Joint one face, then one side side, and finally use the thicknesser/planer to surface the other face.
Using a tablesaw, bandsaw, or circular saw to rip material down to width. Because the pieces are so chunky, you can cheat by running them on their narrow (and jointed) edge through the thicknesser/planer to clean up the cut edge to bring everything to a uniform width.
Step 3: Top
I’m using the Festool Domino as a biscuit jointer here (I don't have a biscuit jointer). The top will come in at about 50mm wider than my thicknessers maximum capacity, which would make flattening the top afterwards difficult.
Mechanical aides (Biscuits, dominoes or even dowels) restrict the boards from shifting up or down during clamp up. I recommend that for this length you have at least 5 "aides" along the length, making sure that the ones on either end are far enough away from the ends that they won't be exposed when you trim the top to length.
It’s not important that the dominoes are glued in (#2), they’re not there for strength. Glue can just be rolled over those holes. Plywood cauls (#3) help distribute pressure and stop the clamps from marring the top
The top is cut to length (#4) after the glue is dried using a tracksaw. A circular saw with a guide will do a good job too. It’s too heavy and large for a regular crosscut sled. I use XPS/insulation foam boards underneath so I can cut all the way through without cutting into my workbench.
Step 4: Cutting Base to Length
All the parts in the base will end up the same width and thickness – 90x40mm (#1)
Once they’re a uniform width and thickness, they can all be cut to length at the table saw. First by squaring one side, flipping, and cutting to length. This works well for the shorter ‘foot’ pieces. (#2/3)
For the larger legs and apron pieces, they can be squared at one end, but it’s a bit more complicated to cut due to the length exceeding my table saw's fence. Using existing t-track on my crosscut sled, I made up a very quick plywood L shaped extension fence. Alternatively, any sort of engineered wood (MDF or plywood) could just be clamped straight to the fence.
The extension fence lets me clamp a block of wood to act as a stop, so all the parts end up the same length.
Why not use a mitre saw? Often mitresaws aren't setup for dead accurate cuts, or if they aren't built into some sort of station with a stop block, it can be difficult to get repeatable cuts. If yours is dialled in for a perfect 90 degree cut and you have a stop, go for it!
Step 5: Joinery (Legs & Apron)
All parts receive the exact same joinery pattern – two dominoes per side, spaced 25mm (1") in from the sides. In the photo (#2), I'm using Incra's T-Rule, but any combination square or double square makes this easy.
Why not integral mortise and tenon? I’m using the Domino here for expediency so my sister could get her table before a (pandemic related) full lock down - integral mortise and tenon are A-OK if you have a little bit more time!
Step 6: Surface Prep
For sanding, I use the pencil scribble method. Lightly scribble all over the piece with a HB/#2 (or softer) pencil, then when its all sanded off, you know you’ve sanded enough and can move onto the next grit.
I sand through 80, 120 and 180 grits. The combination of the particular finish I will be using and the density of the wood recommends 180 grit or no more than 220 grit for best absorption/bonding to the wood.
Step 7: Edge Treatment
After sanding, a light round over is added to all the pieces. My sister wanted to retain the sharp edge look, but I managed to convince her a round over was a good idea for her toddler. For the base pieces, this is done at the router table.
For the table top, it is easier to 'bring the tool to the wood' rather than the other way around, and I used a plunge router. While I used a full size plunge router, a fixed base and/or trim router will do the job just fine - this just had better dust collection of my tools.
In both cases, I used a 1/8" radius round over bit. You can sand a round over onto all the pieces, but a small radius router bit is much more consistent.
Step 8: Table Top Clip Time
I'm just going to go ahead and quote from my previous Instructable, the Mission Style Side Tables, where I covered z-clips
Z-clips are a way to attach table tops to the base while still allowing wood movement.
If you were to just glue on screw the top on without allowing for movement, eventually the table top would likely split. In this case - being a relatively small side table - you could probably get away with it. However, it's good practice to always avoid restricting wood movement when possible. The Z-Clips I use need a 5mm slot that's about 10mm from the top of the apron. I've just used the Domino to cut the slot, but a biscuit jointer or router will work great too. You could even use multiple passes with a table saw - the kerf is on the inside, so it'd be invisible anyway. Make sure you add in the slots before glue up!
In this particular project, you could also drill and screw through the long aprons. There are no short aprons. The long aprons grain goes with the table top grain, so wood movement would not be restricted.
Step 9: Glue Up #1
Due to the size and weight of the base, the glue up will be done in three stages – the two leg assemblies, then joining them with the aprons. Dividing glue up always reduces complexity and stress! Due to the fiddly size, it may still take awhile, which is one of the reasons I've opted to use liquid hide glue.
Add glue to the mortises (both sides) using a brush (acid brushes with the bristles cut to about 10mm are perfect for this), then slide the dominoes/dowels/etc in.
Clamp across the "foot-to-leg" connection.
On the end with no glue up, I quickly cut some spaces the same length as the foot to make sure everything was kept square and didn’t pull in.
If you use a wet rag to wipe away the excess on PVA, you run the risk of contaminating your surface. PVA glue will show up very brightly under your finish. If you are using PVA, wait for it to gel over before scraping it away.
This is not the case for liquid hide glue - a warm, damp rag will clean up and leave no evidence!
Step 10: Glue Up #2
The second stage glue up is done in a very similar manner - squeeze glue into the mortises, slide dominoes in, clamp up. Because of the length (>1000mm), I had to use pipe clamps for the clamp up. Pipe clamps can be extended nearly infinitely by using pipe couplers to join lengths of pipe together.
Another advantage of the hide glue is the way it lubricates the joints, this very tight fitting set of dominoes needs hammering in when its dried, but with hide glue is able to be pushed in by hand.
Step 11: Attaching the Top
In the previous step I outlined cutting the slots for the z-clips, this is when it's a good time to line everything up and actually screw them in.
Step 12: Finish
Books have been written on finishing furniture, so unfortunately I don't think I could properly explain all the options on finishes, let alone all the varied ways to apply them!
I opted for Livos Kunos, as I've been wanting to try it out. Oil based finishes, like the Kunos, will impart a richer colour than most water based finishes. Even if the Kunos isn't the most durable (I don't have enough experience with it one way or another), "occasional" tables like hall tables do not see frequent abuse like a dining table or desk, so are perfect candidates for "close to the wood" finishes.
To apply this finish, wipe on a thin coat with a cotton rag or paper towel. After 5 to 10 minutes, buff off any excess with a clean rag.
After it is dry (~12 hours), a second coat can be applied in the same manner, though considerably less finish is used/absorbed.
Do not bunch up your rags, lay them out flat on some concrete while they dry. Drying causes heat, and the rags can self ignite, this is especially true of any finishes containing linseed oil.
The danger is real, but avoiding it is super easy.
Step 13: All Done!
Because it's such an odd shaped table, it's hard to get it all in frame. To the garden path!
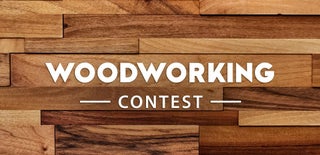
Participated in the
Woodworking Contest