Introduction: Desk Buddy: Work From Home Accessory
Desk Buddy was a request from a friend for a work-from-home “helper” for her laptop and monitor.
This was built entirely from scrap 9mm & 18mm plywood. As such, there isn’t really a cut list or best case optimisation – I was entirely using what I had on hand. That is why the drawer front had a different veneer (before paint), and that is why the drawer is from 18mm rather than 12mm material!
A NOTE ON JOINERY…The joints are “reinforced” with dominoes, but in truth that was just to stop them sliding around during glue up. I used 4mm dominoes, but any size biscuit will do the same job. It’s plywood – butt joined plywood is plenty strong
REBATES/RABBETS...The rebates on the backside of the cabinet, and for the drawer bottom are 6mm wide, 9mm deep (to match the 9mm plywood). Don’t over think this. Wood movement isn’t an issue, nor is strength in this application – I simply didn’t have anything thinner on hand.
TOOLS
There are a 101 ways to do just about everything, and its impossible to cover all possible combinations of tools. Here is a list of what I used
- Table saw
- Tracksaw (/circ saw with a track)
- Jigsaw
- Drill press
- 54mm forstner bit, though smaller will work too depending on how many cables you want to route!
- 35mm forstner bit
- Router table
- Router
- Router Bits
- Flush Trim Bit
- Straight bit or rebate bit (preferably)
- Biscuit Jointer/Domino (Both optional)
Step 1: Design Files
Attached are the original Fusion 360 file, STEP and a PDF of 2D drawings, should you wish to modify it for your own space.
Step 2: Cabinet
As all parts for the cabinet will be 300mm wide, rip a piece of plywood down to that size at the table saw.
The hardest part of the entire project is the cut is the miter on the long piece (832mm) that forms the base for DeskBuddy. If you have a sliding table saw, or a very large crosscut sled, this could be cut at the table saw, otherwise use a tracksaw or circular saw with a track. Take your time lining up this cut so that its square. Only one end needs to be mitred. If you make sure that the offcut is at least 100mm you can rip that down to width later to act as the "short foot"
The rest of the cabinets parts can be safely cut at the table saw, with the blade tilted - two parts have one 90 degree end, and one has two 45 degrees. The dimensions for these are in the included PDF in Step #1.
Step 3: Joinery
To reemphasize, this sort of project does not need actual joinery.
I used the Domino for alignment only, and a biscuit jointer is a perfect substitute in this scenario. You could also use nothing, or use brad nails to hold things in place later on.
If you do choose to use either the Domino or Biscuit jointer, you might find it easier to cut the joints for the 45 degree pieces by butting two pieces back to back and clamping. This lets you set the fence to 90 degrees, and gives you a larger reference surface.
For the mid-panel alignment, clamp a scrap board across to align the tool. This is much easier to align square than the tool.
Step 4: Round Overs
While you could certainly sand a round over on all parts, using a 1/8" (3.125mm) radius bit is a great way to break edges to give a much softer and consistent appearance.
Step 5: Cable Hole
At the back of DeskBuddy is a semi-circle to route all the cables through. Rough out the semi circle with a jigsaw (or bandsaw, or coping saw) staying 2-3mm (1/16" to 1/8") away from the line.
Using some scrap plywood or MDF, 6mm or thicker, drill a hole through the template. Rip half of that hole "off" at the table saw. You now have a perfect semi-circle template ready for routing.
The diameter of the forstner bit is really up to you - if you're able to move the DeskBuddy out from the wall, all you need is the cable diameter, otherwise you need to account for twice the diameter of your countries power plug to be able to fit through.
Step 6: Cable Hole Routed Template
With the template clamped under the existing roughed out semi circle, use a flush trim bit (or if you are using a pattern bit, the template will be on top) to create a perfect semi circle.
While you should probably route downhill (changing the direction of routing at the halfway point), I found no issues with tearout routing the full length in one pass.
Step 7: Cabinet Glue Up
I found it a little easier to glue up the single short end first, using a series of clamping cauls and tape.
Once that was dry, the other leg and "drawer housing" could be all glued up.
Breaking this into to stages means you can more easily move clamps and the workpiece onto angles that would be impossible if you were to try and glue up the whole thing all at once.
The initial glue up can be a little trickier as you don't have as good a reference for square - apply just enough clamping pressure and check with your best square. Too much pressure will pull the leg in.
Step 8: "Drawer Space Rebate"
Awkward title aside, the rebate on the backside of the drawer space can be made using a rebating bit using either a router or at the router table.
This can look a bit dodgy, but the large cabinet surface makes it very safe. Just awkward. The rebate should be 9mm deep (presuming you're using 9mm plywood) and 5-9mm wide.
The radius of the rebate bit will need to be cleaned up with a chisel (the chonkier the better), then the back panel can be glued in.
Step 9: Drawer
The drawer was the remainder of the 18mm plywood material I had and in my case didn't need ripping (it was already slightly smaller than the opening, which is why the false front is a little larger).
Cut everything to length using a mitre gauge - according to the plans, that should be two pieces at 387mm, two at 273mm but measure the glued up cabinet to make sure thats correct. You want a little bit (1mm or 1/16") of wriggle room, but not too much.
After everything is cut to length, a rebate can be cut for the drawer bottom. The rebate is cut on the inside of all pieces (ie the shortest edge). With all pieces mitred, this can be a through rebate as it won't be exposed like it would be if it was unmitred.
Using a rebate bit in the router table, cut the rebate in two passes - one to remove the bulk of the material, then the second pass to fine tune the rebate to fit the drawer bottom.
Step 10: Drawer Pull and Glue Up
Tape up the drawer front and false front so they're aligned. Using a 35mm forstner bit, drill through both at the same time, aligned with the middle of the false front. This drills and aligns the finger pull hole.
Untape the parts, and the drawer can be glued up. Given the mitres, a band clamp is the easiest way to apply pressure to all parts evenly.
Step 11: Drawer Bottom
Once the drawer is out of clamps, the drawer bottom can be cut to fit.
Alternatively you could have used a dado/floating panel, but the short height of the drawer means you'll lose some additional internal storage compared to gluing the bottom into a rebate.
Step 12: Finishing
I went with OSMO PolyX for the clear finish, and just a basic white spray paint.
For the clear coat, PolyX and other hardwax oils need two to three very thin coats, and are best applied in my experience with a 6mm nap microfibre roller, applying ample pressure. For difficult to reach sections, a brush or rag can be used to apply the finish sparingly.
For the white spray paint, apply very thin coats, sanding between. You won't get full coverage from a single coat, but don't apply it too thick otherwise it'll end up a globby mess.
Fun story: the white drawer front was "by accident". Originally my friend wanted everything clear coated, but I sent through a render with no texture on the drawer front so it was easier to differentiate where things start/stopped. She loved that version and I had to figure out how spray paint worked
Make sure to not completely coat the backside - you want to leave an unfinished area to glue the drawer front onto the drawer
Step 13: Final Drawer Glue Up
After the paint is dried on the false front, it can be glued on, using the drilled finger hole for alignment
Step 14: All Done!
DeskBuddy should be done by this point - it's designed for a monitor on the lower section, and a 14-16" laptop on top of the drawer.
The drawer can hold all sorts of things, including your favourite chisel-sword-logo-on-acrylic-charm!
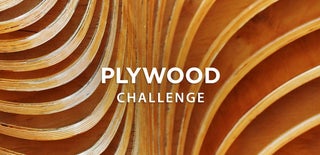
Participated in the
Plywood Challenge