Introduction: Live Edge Hall Table
This Instructable is more of a look at how I built this table, and hopefully it'll give you some inspiration.
You can watch the YouTube video of the build process here:
Step 1: Milling the Slab
The first step was to get this slab flat. This slab of silky oak had been air drying for 2 years so it was dry enough to work with. The challenging part was how to get it flat using a router jig when there was no flat side to use as a reference.
I laid the live edge side down and used bits of wood and spacers to hold it in place. Luckily the slab was big and heavy enough that it didn't want to move very easily, so it never budged when the router went over it. There's hundreds of tutorials out there on how to make a router jig to flatten wood, I highly recommend using this method.
I did 4 passes over the slab and got it to where it was almost done, then filled all the cracks and knots with a slow hardening epoxy. Then one final pass under the router and it was flat.
Then, using a circular saw and handsaw, I cut the ends parallel to each other. I also cut a line along one side of the slab, this would serve as the back of the table. As a hall table I see this either sitting up against a wall or a couch, so having a flat edge at the back makes sense.
Step 2: Building the Legs
The legs were made from merbau. This is a common hardwood here in Australia, mainly used for decking. I got these decking boards from my local big box store and started by removing the ridges with a thicknesser.
Once they were milled I cut them to length and glued 2 boards along their edge to form a panel, 280mm wide.
After this panel had dried I could send it through the thicknesser again to clean the surface for more glue.
I took another wide board and glued that into the centre, to cross over the join on the panel. My concern at this stage was that this panel was going to cup so building up the panel with a running bond would hopefully stop that movement.
Then I glued 2 narrower boards on the outside of that wide board. By this stage the legs were getting heavy but that wasn't a problem. The slab was even heavier so the lower I could get the centre of gravity, the better!
The final step was to cut the legs to size with a circular saw.
Step 3: Cutting the Slab to Accept the Legs
Now that I had the legs made I could use that to mark the cut for the slab. It was a bit of a chicken and egg situation, where I could've used the legs to mark the slab or the slab to mark the legs, but I went with making the legs first because that was stock I that could easily get if I made a mistake. I only had one shot at the slab.
Using a similar setup to the router flattening jig, I lay the slab face down on the workbench. I then pushed the flat end of the slab up against one edge of the 2x4 jig (offset with a couple pieces of timber) and made sure the sides of the jig were 90 degrees to it.
It needed to be square so I could measure up the jig (42mm if I remember correctly) on both sides and this would be where I line up my first saw cut. I could place my homemade track saw on those marks, lower the blade to a specific height, then make multiple cuts to remove the material.
The pictures do a better job of explaining. Essentially I had created an upside down table saw.
After removing all the excess material with a chisel I could drill some 25mm holes using a spade bit. These would accept the figure 8 clips.
I made the same depressions in the legs and screwed the clips in place.
Step 4: Leg Rails and Assembly
Next I cut 2 mortises into each leg. I did this with a router and chisel. This would accept 2 rails made from more decking boards.
After cutting the mortises I sanded everything up to 240 grit. It was easier to do it now while it was all disassembled.
The rails were glued into place and the join was filled with tinted epoxy. I was thinking about hiding the mortise but I felt like the extra detail of the join would look good considering the overall size of the very plain panel.
Step 5: Finishing
Now that all the pieces were ready I used a wipe on polyurethane on all the parts. After that I could assemble the top onto the legs and it was all done!
Thanks for reading.
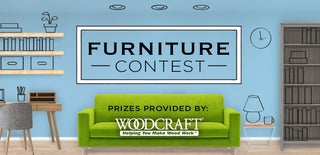
Participated in the
Furniture Contest 2017