Introduction: Making High End Furniture From Plywood - DIY Modern Dining Table
Most people don't look at plywood furniture as high end, but it truly can be. Baltic birch plywood is the cream of the crop when it comes to plywood. Its very straight with tight, even plies that look really good, and unique when exposed. Its only slightly more expensive than the furniture grade plywood you'll get at the big box stores. Check out the video for more details.
Step 1: Cutting the Plywood for the Table Bases.
This table sits on two trapezoidal table bases that are comprised of 6 layers of 2 inch thick baltic birch plywood. That sounds like a lot to do, but this table is very simple to build if you have the right tools.
- Break down the 4'x8' panels into more manageable panels. You'll need a 29" x 56" panel, a 24" x 29" panel, and a 16" x 29" panel.
- Set your table saw fence to two inches and its time to start slicing everything up. Cut (24) 2" x 29" strips, cut (12) 2" x 24" strips, and cut (12) 2" x 16" strips. These dimensions will give your room to work with when you cut them down to the final dimensions.
Step 2: Gluing Up the Table Base Blanks.
Each piece of the table bases are 6 strips of plywood laminated together to form a 4 1/2" wide base with exposed plys.
- Arrange 6 strips and apply glue. I use Titebond II.
- Clamp the blanks up making sure to keep everything as even and straight as possible.
- You'll end up with 4 blanks at 29", 2 blanks at 24", and 2 blanks at 16".
- You can run them blanks through the jointer after they dry to remove excess glue, and get them perfectly flat. I took very shallow passes to remove as little material as possible.
- Sand the blanks smooth and even. Its surprising how smooth the exposed plys of baltic birch plywood get.
Step 3: Cutting the Table Base Angles and Final Dimensions.
These trapezoidal table bases are 27 1/2" tall. Make sure to tape all the ends to prevent tear out.
- Set your saw blade to 9 degrees. All of the angles are cut the same since these pieces are butt joined together.
- For the long sides of the table base (2 on each side) I cut the first side at 9 degree removing as little material as possible lengthwise.
- I measured to 27 1/2" and cut the long side accordingly. The 9 degree angles on top and bottom face the same direction on the side pieces. (see pics for reference) This first long side piece is the template for all others.
- Cut the remaining three 27 1/2" side pieces to match.
- Now cut the top pieces of the table base. There is one on each side. The width of the base is 26" total. With the two sides being 2" thick that makes the top piece 22" wide. This time the 9 degree angles face opposite directions. Once you have the first top piece cut use it to cut the other top piece to match.
- Now for the bottom piece. This time you need to mock up the table base to find the exact width of the bottom piece. (see pic for reference) Again the 9 degree angles face opposite directions. Mark your lines referencing off each side. Cut the first side, and then creep up on the second side until it fits perfectly
Step 4: Assembling the Table Bases.
- I used 5/16" 1 1/2" lag screws to attach the table top. Its easiest to drill these attachment holes before you assemble the base. Mark out three evenly spaced attachment holes, and drill about 1 1/4" through with a 3/4" forstner bit.
- Drill out the attachment holes for the table base itself. I spaced these 1" up, and 1 1/4 inch in from either side. Drill 1" through with a 1/2 forstner bit. Do this for the top and bottom of each side piece. (16 holes total)
- Pre-drill another hole for the screws. I used 3" Spax #14 star bit screws.
- Apply glue before screwing together.
- Drive in all screws. Be mindful of the angle and how deep they seat so as not to drill through the piece.
- Plug holes with 1/2" dowels. I used leftover walnut dowels from my last project.
- Sand the dowels flush and sand the entire base. You can use an orbital sander on the end grain, but be careful not to sand through the veneer face. I used a sanding block for this part.
Step 5: Building the Table Top.
This whole table can be built using two 4'x8' sheets of plywood, however you'll need three sheets if you want a solid 1 1/2" thick table top. Otherwise you can build a frame with the remaining cut offs that gives the top the appearance of being twice the thickness.
- The table top is 66" x 32". Cut two panels at 68" x 34".
- Glue these together. Its really important to spread spread the glue all the way to the edges, and use lots of clamps and things to weigh it down. I did not do this, and I had to spend an extra day on this project fixing the resulting gap between the two panels.
- I used a track saw to cut the edges down to final dimensions (66" x 32"). I set the saw to a 9 degree angle to match the legs.
- Tape the top and sides of each edge prior to cutting to prevent tear out.
- Once the top is cut to size sand the edges smooth, and use a sanding block to break over the sharp corners.
- Lay out the table bases on the bottom. They are inset 8 1/4" from the ends, and 4" from each side. Pre-drill the lag screw attachment holes by first drilling through the middle of the holes you cut with the 3/4 forstner bit. Drill through just enough until it hits the bottom of the table.
- I added tape an inch up on my drill bit to as not to drill too deep. Drill the holes the rest of the way.
Step 6: Finish With Wipe-on Poly and Attaching the Base.
- I added 3 coats of MinWax wipe-on poly in satin. Sand with 220 grit paper between coats, and make sure to remove all dust.
- Use (3) 5/16" 1 1/2" lag screws to attach the base to the table top.
Thats it! You're all done! This table is very sturdy even though there is no stretcher. Thanks for checking it out, and please watch the video for more information. While you are there please subscribe to Jonny Builds to see what I am making next. Thanks.
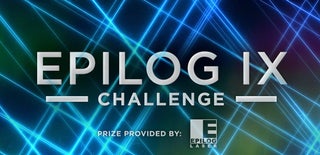
Participated in the
Epilog Challenge 9