Introduction: Making a Chessboard With Live Edges and Piece Storage
One of the first times I ever went to a true hardwood dealer, I was amazed by the sheer amount of color. I didn't know many woods but walnut and pine at that time, so my eyes were opened to species like purpleheart and zebrawood. Not having a very large budget, I walked out the door with only one or two pieces of wood, but I knew exactly what I was planning with them. I had never made a chessboard or worked with live edge wood, but I figured: why not combine them? Since then, I have added to how I made my original board and made improvements to get to this point, which will probably not be the end of the chessboard journey. This is my first build of the base that accompanies this board as well, so feel free to give any suggestions.
Supplies
Here is what you will need to complete this project, and I posted what I suggest as the asterisks:
- Wood!-- You will need two colors of wood that you think have a nice contrast. Here I just used some cedar boards' light (sapwood) and dark (heartwood) parts.
- Glue-- The glue most likely doesn't matter much. Unless for some reason you commonly get this board wet, any wood glue will work. I used mostly Titebond Original.*
- Finish-- I just used lacquer because I wanted to protect the soft cedar, but normally, with harder wood, I would use a hardwax finish like Rubio Monocoat. *
- Sandpaper-- preferably an orbital sander as well.*
- Thin Wood- for drawers and thin walls, 1/4 inch thick.*
- Clamps
- Paint Brushes-- or sponges.*
- Miter saw (or box)-- One that you trust to give you accurate angles.
- Table saw-- For ripping boards.
- Circular saw
- Black paint-- any kind will work, and if you don't want to do step 17, don't bother getting any.*
And some extra supplies for the drawers in the base
Step 1: First Rip and Glue-up
The first step of making any chessboard is to rip four pieces of each color at an equal width. I chose 1 3/4 inch strips to make a 14-inch board. After that, glue the strips against each other, careful to keep them flat (weights work well if you don't have the right clamps). In the picture, I am working on two boards at once.
Step 2: Rip Again and Glue
In this step, you will rip the strips across with the exact same width, then rotate them, every other one, to make the checkered design. Afterward, glue it the same way as before. Once you have finished this step, you can either call it quits or continue to take it to the next level. The left board above was wet to show how it would look with finish.
Step 3: Add Borders
For this step, I used a circular saw to cut the rough (live) edges off of one of my cedar boards at around 3 inches wide at each end. I then mitered the edges and glued them onto the sides, using tape to keep pressure.
Step 4: Rounding Off the Edges
After the glue had dried, I went back with my sander and rounded off the edges after sawing off the large chunks.
Step 5: Fixing My Mistakes
In order to fix my poor angles (both my fault and that of my saw), I simply used a hand saw to cut the corners, using two clamped scrap pieces as a guide. From there, I sliced a couple of heartwood pieces on the table saw to perfectly fit and glued them in. I used heartwood because even if I used the same color of wood, it would have been visible. I opted for contrast to make it look more intentional.
Step 6: Sanding for Finish
This step is fairly straightforward. If you've ever sanded something, then this is the same, but it is necessary to be a little bit more gentle on the live edges to keep from rounding them off. I went from 80-grit sandpaper to 120, 180, 220, and 400. 400 hundred was definitely overkill, but I just wanted to feel the perfectly smooth board. This step will be repeated for the base later.
Step 7: Applying the Finish
I applied the lacquer after blowing all of the dust off. You can also use acetone or the likes to wipe the dust off with a clean rag. I then applied the first coat with a sponge brush, but since I had the window open for ventilation, the dust from my shop quickly got blown in. I then, after about an hour, gave it a quick sanding with 400 grit again and reapplied in a cleaner area. I found it is better to go thin rather than thick on the second coat, if you use the lacquer that I did.
Step 8: The Base
The first step of making the drawer base is to cut the bottom "floor" with a thin material. I used 3/8 inch particle board since we had it lying around, but and quarter-inch-ish material would work better. Cutting it to a 13 1/2-inch square allows for the walls to expand it to exactly 14 inches. Cut one more piece to this exact size to later be the top plate.
Step 9: Making the Side Walls and Drawer Faces
I chose to add an angle between the heartwood and sapwood pieces on the side walls for extra flare, but it is unnecessary. The pieces should be ripped one by one-and-a-half inches, with an equal chamfer (mine was a half-inch). Then cut the pieces to 14 inches long and glue the thin edges together. If you wish to add the color "slash" through the middle, you first need to cut the pieces at an angle, glue them end to end, then cut them to length. The drawer faces will be made the same way, and all pieces should be cut to a 45-degree miter on the ends.
Step 10: Cutting Rabbets
Here I set the blade just high enough to leave a quarter-inch of wood on my table saw and nibbled away at the material until enough was removed for the bottom piece to fit. Do the groove on both sides of the wall. I didn't, but I wish I had before some future steps. I then glued the pieces to the square base on opposite edges.
Step 11: Making the Drawer Slides
This part can be quite tricky to make, but once finished, the result is much smoother than any store-bought slides. That said, I would have saved myself some headache if I had not made drawers and rather had the base open from the top, but I thought that boring. I designed a hole spacer to get the right placement on the piece of wood, but unfortunately, if you don't have a 3D printer, it may not be useful. I also 3D printed the quarter-inch spacers, but those can be made of wood (with patience). From there, I used an appropriately sized dowel (though it did need some sanding to fit). I used hot glue to secure everything because my fit was tight enough.
Step 12: Making the Drawers
I made the drawers each with one rail and slider, but you should definitely consider two since mine was a little unstable. The actual drawers I just made by cutting slices of my particle board and gluing them together. I then checked to make sure I had a good layout for the pieces. Once you are pleased with the drawer, place the rail in the slider and set it on the bottom of the drawer, making sure the rail is square. Afterward, mark it out and attach it with wood glue. After I did this, I laid out the pieces to see how I wanted them oriented and noticed that I would have to grind out a small part of the drawer so the pawns would fit all the way in.
Step 13: Attach the Rails
Place the rail squarely in the middle of the base and glue or bolt it down. I used hot glue because I was not sure if I would change it eventually.
Step 14: Drawer Faces
I then slid the drawers into place, clamped the face where it should go, and ran a bead of glue along the drawer front. Next, simply apply pressure between the drawer and its face.
Step 15: Top Plate
Now, set the second square piece that you made into the rabbets on the top of the walls and faces and glue it down. If you did not make rabbets, attach the top plate directly on top of the walls. You can also inset magnets optionally in the top plate and bottom of the chess board to make the two units connect.
Step 16: Handles/ Knobs
At this time, I used my lathe, although dowel rods are an easy option, to make simple handles. Cutting two 45-degree angles on the connecting parts of the knob made the handles sit nicely in the groove and glue in easily. I used a scrap piece to stabilize the dowel while I cut the angles.
Step 17: Sand
From here, sand the base walls so they will be ready for a finish. To get inside the angles, fold a piece of sandpaper over a scrap piece of wood and run back and forth.
Step 18: Painting
To finish up the drawers, both plates, and the inside (if desired), I painted them black.
Step 19: Finish Again
I had the same issue as before with dust since I was technically doing this at the same time as the board. Therefore, the steps are the exact same as #7- Clean, apply, sand, clean, apply.
Step 20: Show It Off
Now it's time: Invite some friends and show off your new prized possession. Who knows, you may even start playing better. Thank you so much for following along, and be sure to add helpful comments so I can become a better woodworker and Instructable-er!
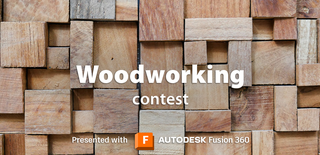
First Prize in the
Woodworking Contest