Introduction: Minecraft: Steve Model! With Bonus Double Chest!
My little brother is a big fan of Minecraft and Christmas is coming up, so I thought instead of buying a Minecraft related present, why don't I make him a Minecraft gift? My answer was to make a model of Steve!
This model is fairly straight forward and is essentially just a bunch of geometric shapes, but because it's geometrical, measurements and angles need to be precise so keep that in mind. Other than that, it's a lot of fun to make!
The movement includes the Head being able to rotate a full 360 degree, and the arms can move back and forth on it's point at a full 360 degree. Unfortunately, the legs are static, this is because a lot of visual accuracy would have to be sacrificed to make the legs move back and forth so instead, they are permanently fixed to the body at an upright position.
Based off Minecraft measurements, Steve is 32 pixels high which makes him 1.875 metres long, meaning that 1 pixel is roughly 5.859cm long in the game. The Styrene Square Tile size I'm using is 6.3mm (or 1/4") so the scale of this piece is about 1:9scale. The total length of this model is 20.8cm long. (or 8 inches)
P.s. If the scaling is wrong and you can provide evidence why, feel free to notify me.
Step 1: Requirements for Model:
Here are the following requirements needed for this build:
Steve Model:
Materials:
Evergreen Square Tile Styrene (This product is quite specific for this build as it provides the square grid which makes up the pixels, it's also a little pricey depending on what size grid you want)
1mm Regular Styrene
Styrene Tubing or similar model making supports
Polyurethane Rigid 2 Part Foam ( Aerosol expanding foam will also work for this, I just prefer using 2 part expanding foam)
2 Part Epoxy Putty (I use Milliput)
6 inches of 1/4" OD plastic tube and 1/4" ID spacer (You can use any thickness, but the tube and spacers must match
N45 Neodymium magnets (optional)
Tools:
Power drill with a drill bit equal to the plastic tube and spacer diameter (I chose 1/4" drill bit)
Needle Files
X-acto Knife (No.11 standard blades)
Steel Ruler
Misc. Measuring Equipment (right angles, protractors, etc.)
Consumables:
Sandpaper Grit; 80, 120, 200, 400, 800
Polystyrene Cement
Precision Super Glue (liquid)
Lots of Plastic Cups and Mixing Utensils
Paints; Skin, Blue, Purple, Brown, Grey, White (I'm using Citadel Acrylic paints for this)
Paint Primer (optional)
Clear Coat Spray
Step 2: Templates
The templates for Steve are very simple, since he is geometrical and his pixels show how long each part of him is, but I've supplied the templates anyway which saves the trouble of doing it yourself.
The template layout is based on the Evergreen 1/4" Square Tile size sheet which measures at 15cm/6" by 30cm/12", resulting with a grid thats 24X48 tiles.
Pieces:
Head: 6 8X8 tiles
Body: 2 8X12 tiles, 2 4X12 tiles, 2 4X8 tiles
Arms and Legs:16 4X12 tiles, 8 4X4 tiles
Caps: 8 4X4 tiles
The pieces with the marked drill holes are areas that meet up; the marked blank head piece connects to the marked blank body piece and the marked arms pieces connect to the marked body pieces.
The holes are for inserting the 1/4 tube (or whatever thickness your using) so the arms and the head can connect to the body and have movement.
P.s. I've uploaded a 3D model I've made of Steve to show in three-dimensions what the model will be like when you build it. Feel free to do what you wish with it.
Attachments
Step 3: Cutting and Drilling
Once you have your templates, you need to cut out all the pieces on the Tiled Styrene; this is particularly easy because the X-Acto blade run along the grid lines, meaning you'll always have a straight line. The easiest way to cut Styrene is to score the line, then gently snap the score line and it will snap cleanly.
When you cut your pieces, organise the pieces in order to keep track of what pieces you have already cut, and what pieces need cutting next.
Holes need drilling for the Head and Body meeting point, and the Arms and Body meeting point. The Head and Body meeting point were drilled at the same time and the same was done for the Arms and Body meeting points, this is to ensure that the holes meet up for when the 1/4" tubes are fixed in place to give movement for the Head and the Arms.
Step 4: Building the Head, Arms and Legs
Once all of your pieces are cut out and organised, you can start adhering the pieces, but beforehand, you may want to lightly sand the lines of each piece to ensure their flat; just place the line of the piece on top of a sheet of 120 grit (or similar grit) sandpaper and lightly sand along the surface.
Note:We only want to bond 5 pieces together at this stage, make sure that the pieces that have a hole are the ones that are glued last.
With your pieces, you can begin using polystyrene cement to bond the pieces together. The best way to get a 90 degree join is to place both pieces against an edge with a flat horizontal surface, and a 90 degree vertical wall and sparingly run a line of cement along the join of the plastic and hold the plastic in place for about 10 seconds.
When the initial bond has set, you need to adhere some reinforcement. For this, we will use the round tube Styrene and simply adhere a piece of the tube along the inside edge. Let the bond cure for another 10 seconds and you should now have a strong bond. There are a fair amount of joins to adhere so just take your time and be gentle during this process; the last thing you want is to bond 2 edges which are out of line!
Note: If you want even more reinforcement along the joins, 2 Part Epoxy Putty can be mixed together (Ratio 1:1) and squished into the join and when it cures, (roughly 4 hour cure rime) it will be rock hard and it won't budge at all.
Step 5: Building the Body
You may be wondering why the body is a separate step, well the reason for that is, the method of building the body is different to making the other parts. It is crucial that the body is built properly as it is the central piece; any areas that are not made properly will mess up the composition of the piece.
To start with, you will want to build the body by starting with the back piece and glueing on the lower piece where the legs meet; this is the only side piece without a hole and it will help align the pieces that do have holes.
With the pieces that do have holes, you will need to glue on a spacer for each hole as these will help guide the tube and keep it straight to aid the articulation. To glue the spacers, rough both surfaces that meet each other and use the 1/4" tube as a guide to keep the spacer in line with the hole. I drilled a hole that's slightly larger than the tube in a scrap piece of wood and I fed the tube through that so the tube would stay vertical when the spacer is glued.
Now you will want to glue the side pieces where the arms will meet to the base. Feed the tube through both spacers and out both ends to make sure both side pieces are perfectly lined up and glue the pieces in place, this is critical that you line it up perfectly, if there not, the arms won't line up flat against the body and it will look crooked.
When you are absolutely sure the pieces are lined up, super glue around the spacer and the tube so the tube can't slide around; cut a piece of 1/4" tube off, ( I cut the tube 3'3/4" long) leaving some of it poking out of the body.
The last piece for this step to attach is the neck. This piece needs a spacer like the other pieces because the tube will connect to the head. (I had to cut the spacer in half so it would fit.) When the piece is glued in, glue in the end of the tube to the tube that feeds through the arms and glue around the spacer; on top of the tubes now being lined up, the tube will also act as structual supports for the body.
Note:Do not glue on the last piece as this piece needs to be filled with foam first, then the piece will be attached.
Step 6: Extra Reinforcement
This step isn't entirely necessary, but I highly recommend adding extra reinforcement and pouring expanding foam to ensure the piece is a strong as possible.
With your open pieces, you can cut some strip styrene to length and glue the strip from wall to wall. This helps prevent the styrene walls bending towards each other and prevents the joins from cracking and breaking, in the event that the piece is dropped, or someone applies too much pressure when handling.
The last thing you can do to strengthen the piece is to fill it. You can use resin but resin can get heavy and in some cases, melt the plastic so instead of resin, we will use expanding foam to make the piece dense.
You can use either 2 part rigid pour foam, or regular aerosol expanding foam. (you will need water to activate the aerosol expanding foam) Simply pour (or spray) the expanding foam into the piece but be careful as foam can rapidly expand, so use a small amount, otherwise, your foam will go out of control! If it does go out of control, just let it cure and carve/sand it off.
Note: This, again isn't necessary but I decided to glue a piece of extruded polystyrene in the body instead of pour foam; you can use pour foam as normal.
Step 7: Final Glueing and Piece Assembly
So you now have your pieces filled with foam (if you chose to) but your pieces still have a piece missing, so they will soon need to be added on but first, we need to do a couple of things.
You need to glue a spacer to the drilled holes on the inside of each piece, just like with the body. The spacers act as guides for lining up the 1/4" tube.
Next is to drill and carve out cavity's for the pieces with spacers to fit into. I simply used a drill and drilled out the foam so the spacers can fit in.
All of the final spacer pieces can be glued together by placing their respective pieces on top of them. Make sure you line up the last piece properly as you only get one shot at doing it right. The legs are glued in a different way however; a piece of 1mm regular styrene is glued between both leg pieces to distinguish the separation of the leg pieces, otherwise they will look like one merged piece instead of legs.
The last steps before painting requires you to adhere the legs to the body, this is fiddly to do since you only get 1 good shot at gluing it right. I chose to use superglue to bond the pieces together. For extra strength and to hide the tile gaps between the legs and body, I sculpted a line of Milliput around the seam.
Once all of the pieces are assembled, sand any edges and blend everything flush to ensure that everything meets up flat.
Step 8: Painting
Once your pieces are clean and to your liking, you can start the painting process.
You can choose to "prime" the surface with primer if you wish but the paints I used stuck very well to the styrene so I chose not to do so.
Your choice of colours and shades for Steve can be pretty much anything you like since in the game, you can personalize your character so it's really up to you what paint job you want to do.
For the sake of simplicity, I chose to paint the "Simple Steve" paint scheme found on the cover of the game; there are only 6 colours for the "Simple Steve" scheme because the tiles are all the same shade of colour, instead of individual shades on each tile which would require loads of paints. I have also uploaded a layout of Steve that can be referred to for painting.
I decided to start with all of the skin tiles, for this I used a mix of Kislev Flesh and Ceramite White to lighten the skin tone.
When all of the skin tiles were applied, I started with the arms since there the simplest. The rest of the tiles are painted blue, these are the shoulders of the model.
I then moved onto the body/legs. The blue was added most of the way down, leaving a 2 tile gap for the purple band to around. For the front and back, you can see blue tiles along the purple strip, I'm not sure what they are but they are on the model so staying true to the model, I added them. Most of the legs are purple with a couple rows of tiles being grey; I didn't have grey paint so I mixed a touch of Abaddon Black with Ceramite white to make grey.
Lastly is the head, I saved this for last since it's more complicated than the rest. The mouth is the same brown as the hair and the nose is straight Kislev Flesh. The basic model has blue/purple eyes but I wanted to so brown eyes instead.
Once all of your colours are painted on, spray all surfaces with Clear coat to protect the paint job. Let the clear coat cure for 24 hours to ensure the pieces are dry.
Step 9: Bonus Steps: Double Chest Storage Box
To add an extra touch to this model, I decided to make a Double Chest that Steve can be place inside to protect him from the Creepers! Actually, it's just to keep the model safe for transportation and storage instead of placing him in a cardboard box.
P.S. I have made a 3D model of the chest in Google Sketchup for reference so feel free to do whatever you wish with it. You will need Google Sketchup installed to open the uploaded file.
Attachments
Step 10: Requirements for Chest
Materials:
MDF (I chose 12mm thickness)
2 Hinges with the same width as your material thickness (Brass Hinges are a nice choice)
Foam for padding (I chose EVA foam)
Neodymium Magnets
Tools:
Power cutting saw (Table saw, Jig saw, Band saw etc.)
(Optional) Belt Sander (not needed but massively beneficial if you have access to one)
Power Drill
Orbital Sander
Various Rasps/Files
Hammer + Nails (or nailer if you have one)
(Optional) Rotary Tool
Consumables:
Masking Tape
Sandpaper
Paints; Brown paint, Black paint, Silver paint, Clear coat
MDF Sealer
Cheap Liquid Super Glue (The sealing step for the chest explains why you want this kind of Super Glue)
Wood Glue
Dust Mask
Step 11: Double Chest Templates and Cutting
The Double chest is very simple; it has a lid, a box and a small silver block. In centimetres, The box and lid together is 16H, 32W, 16D and the lock piece is (in inches) 2"H, 1"W and 1/2"D.
The templates above are specifically made for working with 12mm thick material so if you are not using 12mm, you will need to make new measurements to account for the thickness of the material.
Cut out each piece using any cutting power tool you have; Anything that cuts straight like a Table saw is ideal for this but I made do with a good ol' Jigsaw.
Important warning:MDF contains Formaldehyde which is not pleasant to inhale over long exposure so always wear a dust mask when working with MDF, especially when you are sanding it.
Step 12: Glueing and Assembling the Box and Lid
These pieces need glueing in a specific way; the pieces which make up the walls for the lid and the box need glueing AROUND the base, NOTON TOP. This is very important because the thickness and the length of the pieces account for each other and the templates were made to be joined in this particular way. If you do choose to make your box with a different method, always consider the thickness of the material and how they all piece together.
When you have checked what pieces go where, you need to assemble the pieces. I chose to use small nails and wood glue to assemble my box and lid, alternatively you can use wood screws. If you're using nails to hammer it together, hammer the nails in part way before assembling so when you join them together, you can tap them in without the nails falling out.
For the hinges, you will need to channel 2 grooves on the box and on the lid. I used engraving tools since their small and neat but if you have small chisels, I would advise using them instead. I cleaned up the channel with a rasp and sandpaper to level it as best as I could.
If you do have areas with overhang and the meeting point isn't flush, you'll want to sand it flush with a power sanding tool; this will be very beneficiall when it comes to the hinge and lock stage. A belt sander is the ideal tool since it sands flat and tears away excess material but an orbital sander will get the job done as well.
Step 13: Filling Gaps
If some areas have a gap, or you accidentally removed material that needs to be added back, using filler is the only remedy to resolve the situation, fortunately, filler can fix a whole magnitude of problems that can hide a lot of sins.
I had a gap on the side of my lid where I accidentally cut a couple extra mm of the edge, resulting in an obvious slit down the side, using car body filler (commonly referred to as "Bondo" in the States) will sort the mess out; just use a filling knife or similar spatula and fill along the gap.
When the body filler cures (around 10 mins depending on the mix) it can be sanded smooth, a massive bonus to body filler is that it sands gloriously smooth so it blends right in so when the box is painted, it will look like as if the gap never existed.
Warning:Body filler is a little bit toxic, so work in a well ventilated area and wear a respirator; it's not going to have an effect if you use it infrequently but if you have prolonged exposure with it (like every day for a year with no protection for example), it may cause health problems.
Step 14: Hinges
The best time to apply the hinges is when the box and lid are assembled, that both the lid and box fit flush with no overhang and all gaps have been filled and sanded.
Wit the slots that have been chiselled out, line up the hinges with the box and lid and mark the countersunk holes where the screws will go so you can see where to drill. The best way to ensure the hinges will freely pivot and that the lid and box will line up, fold the hinges down the side of the box then mark your holes.
Drill pilot holes for the screws to screw in; make sure you use a drill bit slightly thinner than the screw itself or the screw won't have anything to "bite" onto thus rendering it useless.
Either screw in the screws through the hinges on the box with either a screwdriver or a power drill with the right head. (in this case, phillips head) Make sure the hinges are lined up properly and that they can freely pivot.
When the hinges are screwed into the box, line up the lid and repeat the process, making sure everything is lined up. If everything was done right, your lid and box should now open and close freely and the join should be flush.
This isn't recommended but as you may see, I have used body filler over my hinges. This is to disguise the fact that this box is on a hinge because the game model has no hinges at all and I'm trying to make it as close to the game model as possible.
If you choose to body fill over the hinges, ensure that everything is perfectly lined up as you will not be able to take the hinges off once you start, and please keep in note that if you do this, you may clog up the hinge mechanism if you apply too much over the pivot. I did a few passes to slowly build up thickness and so I can avoid clogging the pivot. Once the thickness is built up, sand it flush with the edge.
Step 15: Magnetic Lock
Now that the lid hinges up and down freely and that the the front meeting point sits flush, we can now move onto the latch. It's very important that the lid and box are flat with each other because the magnets need flat contact to be effective; if the magnets don't have proper contact, the latch will lose magnetic contact and be rendered almost useless.
With the lock piece cut out from the template, find the centre of the box (since the box is 32cm, my middle point was 16cm) and draw an outline of the lock piece around the box. The lock will be glued to the lid so I drew the outline 1/2" above the box.
You will need to drill a hole that is slightly wider than the diameter of the magnets in the back of the "lock" piece and a hole in the box parallel to the hole drilled in the "lock" piece.
Adhere the magnets into the holes and use a filler of your choice to enclose the magnets inside forever; be sure you glue them facing each other so they attract, not repel! Another note is you will need to use a plastic spreader or similar object (like an expired credit card) to spread the filler since the magnet will latch onto your filler knife because it's magnetic!
Lastly, just sand back the filler to be flush with the MDF and adhere the top 1/2" of the "lock" piece with wood glue to the lid using a small clamp. Hammering a nail in the back of the lock through the lid is optional but it will further increase the strength of the join.
Step 16: (Optional) Bondo Squish
Despite making the lid and box edge as flat a possible, sometimes it's just not possible to flatten it without removing too much material so a great way to resolve this is a method called the "Bondo Squish." The "Bondo Squish" is a very cool trick you can use to make 2 parts seamlessly join together.
To start with, you'll need to decide what side you want the body filler to stick to, in my case, I chose the box. Once you've chosen your side, tape the other side with tape, preferably one with a shiny surface along the edges that you want to fill.
Once prepped, apply body filler along the edge evenly and close the lid; apply some force to really squish it down.
When the body filler has "mid cured," (when it's formed, but not fully hard) open up the halves to reveal the squished filler; if done right, all of the filler should be on the edge you chose and none should be on the tape.
Trim the excess while it's still mid curing with a blade. Once it's fully cured, sand any undesired areas.
Step 17: Final Preperation
With the box fully assembled, you are close to painting but beforehand, the MDF must be prepped properly to ensure the painting process goes smoothly.
MDF deteriorates when it comes into contact with moisture so the fibres need sealing to prevent this. My 2 favourite items for sealing is a tin of MDF sealer, and cheap liquid super glue.
MDF sealer is great for the faces of the box since they apply on thinly and they dry clear, the edges on the other hand needs more attention. Since these edges are raw cut, these are the most important parts to get sealed.
I love using cheap "pound/dollar" store liquid super glue because it soaks into the fibres, this means that when you sand the edges, they remain sealed and strong whereas other sealants would be removed if sanded too much. Simply run lines over the cut edges and let it soak into the fibres.
With all of the MDF sealed, I decided to apply a layer of polyfiller on surfaces that were a little uneven and sanded them smooth with a sanding block. Even if you don't use polyfiller, I would recommend hand sanding all over the box because power sanders can still leave a rough-ish surface depending on the tool and grit.
Lastly, a couple of minor gaps may need patching up so if there are any gaps left that you have missed, now is the time to address them. In my case, the outside area of the hinges looked a bit ugly so a simple pass of filler was applied and sanded smooth.
Step 18: Painting
Note:Although I went for the traditional colours and paint scheme of the box, you can be quite creative with your choice of colour and paint scheme if you wanted to.
The painting process is pretty much the same method as painting the model, except masking tape is required for this step if you want the black lines.
To begin with, Apply a couple coats of primer and sand lightly in-between layers for a smooth surface to paint on.
Next, apply a couple coats of light brown paint on the outside of the box (I used Rust-oleum Nutmeg Satin as my choice of brown.) When the outside had cured for 24 hours, open it and spray a couple coats on in inside. Let this cure for 24 hours as well before touching it as you might leave fingerprints.
When the light brown paint is dry, you will need to run masking tape along all the edges so the black paint can be applied to create the black edges. I left a 1/2" space between the edge of the box and the tape so all of the black strips were the same width.
Remove the masking tape when the paint has dry and spray the inside and outside with 2/3 layers of clear coat, then let it dry for 24 hours to be sure that the clear coat has cured.
Lastly, paint the lock with either a silver or grey colour. I used acrylic model paints to paint it instead of spray paint because there is more control with hand painting. If you use spray paint for the lock, mask the surrounding area.
Step 19: Foam Padding
The box may be done and Steve is ready to go with it, but as it stands it's just a hollow box and if you want Steve to sit inside, the box will require padding.
I chose 12mm EVA foam floor mats as this is the material I had on hand, I chose 12mm specifically because you want foam that is 2 tiles thick to your model and because my model is 1/4" thick per tile, 12mm add up almost exactly to 2 tiles. I have made and uploaded a 3D model of the foam pieces to help visualize the task on hand.
Whatever foam you use, you'll need the same outline as the model. The simplest way of doing this is to simply draw around the model on a piece of card and cut it out. I've provided a template if you wish to simply print it off and use that instead.
You'll need to cut out the sheets of foam to the same measurements as the base of the box (in my case, 13.6 X 29.6.) When you have your pieces, transfer the template to the foam and cut it out with a box cutter and a steel ruler; one is the whole outline of the model, the other is just a slot for the head.
The pieces can now be inserted into the box; the head slot goes in first with the outline on top. there is no need for glue because the foam is locked in with friction but if you wish to glue the foam, you can use contact cement (UHU glue or Super 77 contact adhesive) or just use good ol' hot glue to tack it in place. Steve is now secured!
Attachments
Step 20: Complete!
Hurrah! This project is complete! You can now do whatever you want with your Steve model, I wrapped mine in Minecraft diamond wrapping paper to give to my Brother this Christmas; what will you do with your Steve?
If you guys have any questions, just ask and I'll do my best to respond and if you guys use this Instructable to make your own model, please share it with me! I would love to see anyone who has made one.
P.s. If this Instructable gets a strong, positive response from you guys and you want to see it, I could make Instructables for accessories like pickaxe's, swords, armor and extra models such as Creepers, Pigs, Wolves and loads of other stuff; let me know what you think.

Grand Prize in the
Minecraft Challenge
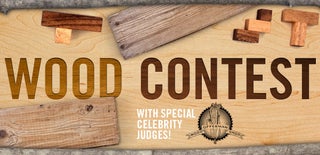
Participated in the
Wood Contest
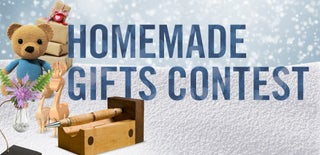
Participated in the
Homemade Gifts Contest
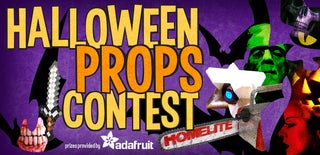
Participated in the
Halloween Props Contest 2015