Introduction: Motorized Screw Organizer With Jam Jars: the Caroustore
I suggest to you a practical and original system to find your hardware (screws, nails, bolts ...): a carousel of 32 jam jar, motorized with a wiper motor.
Finding a piece becomes quick because a sample of each piece is visible in a numbered rack.
Working: the desired part is marked on the display, the corresponding button is pressed, the system rotates in the shortest direction, slowed down, stops, the light comes on for 10 seconds and the parts can be taken by unscrewing jar of its lid.
Video : https://youtu.be/_vXFOUmiD2g
Time spent:
- about 70H
Tools used:
- Circular saw,
- miter saw,
- drill,
- screwdriver,
- router ...
Main materials:
- MDF Wood,
- 32 Glass jam jars 375 grams (empty is better !),
- Wiper motor,
- GT2 40 Teeth Alumium pulley
- 2 Ball Bearings 52x25x15mm
- 16 Ball Bearing 12mmx6mmx4mm
Electronic part:
- Power supply 12V 10A,
- Arduino Uno,
- Single Chip 30A VNH2SP30 Monster Motor Diver Module
- 74HC165 (for buttons),
- LED strip 12V,
- 2pcs Sensor Magnetic Switch with 9 magnets
- Emergency Stop Switch
- 8 Momentary Push Button
- 9 x 1 Kohm resitors
- BD 137 transistor
Step 1: Studies and Plans
The jars being suspended by their lids, they are on a rotating axis to always have the head up.
So I started by doing a simulation with the software Physion, then a "model" cardboard to check that the jars would not touch during the rotation.
Attachments
Step 2: Pulleys
The pulley is cut into 16 mm MDF with a router in "compass" mode.
The throat of this pulley is dug with a router mounted under the workbench. I fixed the piece in order to make it turn on its axis. I then stick a piece of belt to make a notched pulley...
The trays are cut with a router in 10mm MDF.
I cut a circle in a recovery board (white on photo) to make a router template, it serves to hollow the center of the trays on 5 mm to accommodate the ball bearings. (52mm outside, 25mm inside).
The bearings are thus trapped between the trays and the pulley (or the freewheel).
Step 3: The Motor
Intermediate test and I realize that the motor will not be "sturdy enough". So I switch to a truck wiper motor (24V but it works very well in 12V).
I enlarge the hole of a pulley and I tapping it and it takes place on the axis of the motor (Secured with 2 BTR screws)
Step 4: Jar Holders
The supports of the jars are mounted on small 12mm ball bearings, I trace their pitches to create a housing for the router (12mm milling cutter only)...
The supports of the jar are cut in wood battens and then drilled to receive the wooden piton.
The axis of these supports is provided by a wood piton engaged in force in a bearing.
These pins are driven into the mallet battens.
8 other cleats are screwed to close the "cage".
Step 5: Installation of Jars
I drill holes on the lids of the jars of jam.
These covers are then screwed onto the movable supports (using a cardboard template)
Step 6: The Built
On the sides of the fixed part (the frame) I drill the holes of 25mm for the axis.
Then come the 3 holes to fix the motor.
The frame is made in a 15 mm medium (MDF), screwed and glued.
At the rear you can see the fixings for the wall.
Step 7: Sensors
To detect the 8 positions, I use reed switch (alarm sensor with magnets).
They take place on the motor side :
- magnets on the moving part
- 1 fixed sensor for the 8 positions
- 1 fixed sensor for position 1 (init)
Step 8: Axis and Light
The axis is cut in a 25mm steel tube.
I plan a hole to fix it and one to pass the wires of the lighting (LED strip).
So that it can not rotate (are the bearings that must rotate) I block it with a square.
On the axis (which is fixed) I add a strip of self-adhesive LED which lights 10 seconds after the position reached.
Step 9: Electronic
For the electronic part I used an Arduino Uno. It simplifies the circuit very much!
And for the power part (motor control), I used a module VNH2SP30 (H bridge) which supports 14A and allows to vary the speed, reverse the direction ...
The plan and the code of the Arduino are available for download.
Step 10: Control Board
For the control board I drilled the holes of the buttons in 3mm medium.
The sides of the control panel are glued with a frame press.
The polycarbonate (plexi) will allow to see the samples.
The facade is painted black and is then screwed onto the frame with hinges.
Step 11: Specimen Box
For the specimen box I used falls of plastics coming from corner rods. They are glued to the glue gun.
The specimen box is installed behind the glass. It is easily removable to add / replace a location.
I also add numbers to locate locations
Step 12: Done!
The system is installed on the wall (in a lost corner) and it is ready to make my life easier!
And you ? What would you classify in the Caroustore? Candy? Jewelry? Other?
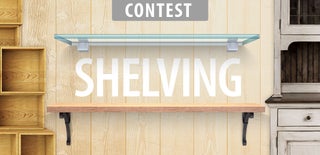
Third Prize in the
Shelving Contest 2016