Introduction: Stairs, Stairs, Stairs,...
Back in 2007 I decided to build my own stairs to get more room in our new home. There was a straight prefab concrete staircase (that we had removed through the roof) switched for a 180° run. 35 years ago my parents did the same in their flat to gain another 2m² of room. Their wooden staircase cost 70.000ATS (5000€) back then which would be 9250€ in today’s money. I got some offers and decided that it would be worth trying it on my own and probably a lot of fun too.
So here I am in Corona lock-down and recently built my third and 4th stair at my brother’s house (4th and 5th if you count one I only designed for a friend). Why not write about it.
Step 1: Build to Code
The first thing to know is your local building code which may vary from city to city and can change over time. It will tell you how wide your stair has to be, how the walking line should be calculated to code, minimum headroom, maximum steepness, etc.
With the maximum steepness you get you first clue how many steps your stair will need. It is a good idea to try lots of different stairs to determine which run and riser measurements are still comfortable for you to walk. I did keep a tape measure in my pocket for some weeks to catalogue as many stairs as I could.
A French architect named François Blondel came up with an effective formula to develop a comfortable and effective staircase.
The idea is to get a step of around 63-65cm. A step is 2 risers + 1 tread.
2 Risers + 1 Tread = 63-65 cm
In reality the step of an adult is between 59cm-65cm, 63cm is a normal stroll.
If you go up you only do half the distance thus you take the riser times two.
Staying on the lower end will keep your stair comfortable for smaller and handicapped people too. Maybe Blondel had a strong male step in mind when he came up with his formula or had a great emphasis on effectiveness/space saving.
There is a second formula for comfort ability which says
Step depth (tread+nosing) – Riser = 12 cm
My steepest staircase is the one to my basement which I shortened around 95cm by switching from 15 to 14 risers and shorter treads. It’s 19.7cm/27cm-3cm nosing (63.4cm step) and still rather comfortable to walk if not a little steep for smaller people than me.
The main stair to the upper level is 18.5cm/29cm-3cm nosing (63cm step).
My brothers upper stair is 16.6cm/30cm-3cm (60cm step), the lower 17.5cm/29cm-3cm (61cm step).
The nosing adds a little length for your foot that you don’t hit the riser. More nosing is needed for shorter treads (which can be as small as 21cm in DIN 18065…Germany got very clear and exhaustive norms for everything - fortunately I am Austrian).
18cm/27cm or 17cm/29cm are known as very comfortable. Older public staircases (subway ~1900) are even 15cm/35cm which is good for older people. Today we got much steeper stairs but that’s because people use the elevator or escalator (which is usually really steep if you ever try to walk one).
Ultimately you will be limited by the opening and space you got to design your stair.
A good resource are technical school books. I learned from such a book, online resources and got assurance from a professional stair builder that my final version was perfectly fine. Ultimately you are liable for the safety of your stair so please consider consulting a professional when you are not sure.
Another great inspiration was the best architecture forum that ever existed. Unfortunately pushpullbar.com only exists as a (relatively unexciting) FB group by now. In reminiscence I named my Ibble after the longest and best thread on stairs that ever existed...and got lost when the forum ceased to exist.
Step 2: Materials and Tools.
Wood
We always used massive wood countertops for the stairs. My main stair is made from 38mm IKEA birch which I used with the B side up for a very rustic and wild look.
My basement stair and my brothers stairs are all 40mm beech. 40x630x3000mm/99€ , we needed 4 boards for each staircase.
The boards even fit into my Sharan if I take out all four childs seats ;)). These massive boards are rather heavy, you need two people to handle them and two boards would exceed the carrying limit of my rack/roof.
Stringers on all 4 stairs I built are made of 60x120x6000mm KVH (KonstruktionsVollHolz/solid construction timber) which are 5€/m or 30€ a piece. They cut them to length for you at the big-box-store.
As you can see in the pictures we drew everything up on the computer to know exactly where we had to cut.
We had to buy 4 pieces for each staircase.
The wood for each stair was 520€ at my brothers place. My birch stair was around 700€.
Unfortunately IKEA doesn’t sell massive wooden countertops anymore.
All these countertops are made of short pieces of wood and you will see a zigzag router pattern where they are glued together. They are very subtle though and you will never notice them if you don’t look hard. Alternatively you can buy boards with stringers running the whole length (often especially made for stairs) or rip your own wood and glue your own stairs. I have done that (my father in law got board-jig/clamp for just that) but I only do it for special wood and when a special pattern is required.
4 pieces of KVH 60x120x6000mm 120€
4 countertops 40x630x3000mm 400€
We always use the outer edges of the countertops for the front edges of the steps. On one side they are rounded. You can use that same radius on the steps cut from the back of the board also.
Stair paint
MDF for the raisers
Screws and fastening
Wood glue
Tools
My first Christmas present from my father in law 2007 was a cheap green Bosch circular saw. I used it to cut all my stairs and by the time I was done the blade was done too. We used some wooden battens for a fence to cut along. The only other tool I used to cut all compound cuts in the stringers was a Japanese Ryoba pull saw.
Some years ago and some grandchildren later I got a Makita divesaw with a rail and used that one for the next 3 stairs.
For the 3rd stair I used a miter saw for some of the compound cuts in the stringers and also the dive saw. Only problem with the dive saw being that it is limited to 50mm depth with the rail and the stringers are 60mm.
For that reason we bought a 75mm dive saw for the last staircase. There are only two of these available here. The Festool TS75 (800€) and the cheap PL75 Scheppach dive saw (160€+40€ for the rail). We bought the cheap one and it has been a real time saver for the stringers, we didn’t even use the miter saw anymore since setup time for cuts is much faster with the rail+divesaw combo. You will still need the Ryoba for long compound cuts or finishing corners the circular blade can’t reach. We also used a jig saw with a 200mm blade for finishing corners or doing some cuts when it was possible or easier than using the dive saw. For the countertops the Makita is still the stronger choice. We also used routers for rounding the front edges of the steps and routing hole into the stringers to sink nuts.
CAD program
Circular saw/dive saw
Ryoba saw
Angle and ruler for marking
Tape measure
Laser level (2 are better)
Jig saw with the mother of all blades
Router
Step 3: Designing a Staircase
There are different regulations for designing a winding (double winding) stair. Like I mentioned before regulations changed quite a bit over the last 10 years in my city. With the old drawing method my main stair only got one straight stair in between (first picture). The new recommended construction method is much easier and demands only the next stair after the corner to wind. (last pictures and pdf.)
The circle method
The later is very easy to learn. You need the opening, draw a middle line and add +10% out of the middle (or 60% from the inside). Thats your walking line. Add 300mm radius around the corner on the walking line. An R200 circle where the first edge meets the inside wall. Draw a circle at the intersection of the walking line with the first steps edge and a 120mm circle at intersection of the edge with the 200mm circle. The radius on the walking line has to be your steps width without the nose. On the inside you use a minimum desired width which is often found in regulatories (the step can't narrow to a point on the inside so you can't just draw all edges to one point). In the first drawing you can notice that all inside width are dimensioned to see if they aren't under the minimum length. That can't happen with the new method since you will draw an inside circle of 120mm radius (the pink one) for every step. Then you draw a tangent through on the circle on the walking line and the 120mm circle and get the next edge. Where your new edge meets the walking line you draw the next circle.
Important: The edge is always the tangent on the circles. The circles middle is at the intersection of the walking line and edge of the step.
Start with a new 200mm circle where the new edge meets the wall and go on from there. You can add or substract some millimeters on the inside if it you need a wider step there. The most important part is the step on the walking line. Since we got two feet set apart and we never walk exactly on that walking line we have to compensate for shorter or longer steps anyways while walking a corner on a stair. The objective is to keep these deviations relatively uniform.
When you are done you add a nose to every edge (30mm in our case).
The idea with this method is to only have the stairs wind around the corner. The step after the corner should be drawn straight (meet the wall at 90°) again. Here's a PDF to show the method.
You will in any case have to consult local regulations before designing your stair. In some regions railings are also mandatory. For the sake of children safety there are rules for gaps, openings and climb ability of railings. In the UK the minimum width of a step on the narrow side seems to be a minimum of 50mm.
First thing in any case is to determine your riser. Just take your floor to floor height and divide it by 18 to get your number of stairs. Take the next full number and divide your height.
Floor to floor = 280cm/18=15.55(16)
280/16=17.5cm riser.
Now you extrude all the treads to the thickness of your material (40mm in my case) and move them each up to their final level.
For the stringers you draw a 2D beam the dimension you intend to use and place it on each side so that you don't get too little beam width. On straight Stairs you can just add triangles on top of your support beam and have the angle follow your stair. On a wound stair you have to optimize this by hand. I always try to cut as little as possible from the beams to save work. On the screenshots you can see that this is not that easy on the outside where short and long outer edges won't let you use one optimal angle. You just have to set the beam lower so you have it running from top to bottom. On the upper inside I added a triangle to support the beam. Additionally the beam was screwed to two massive posts hidden in the wall. Those would not be necessary but why not...
When you have drawn your stringers/beams you can extrude them to their depth and move them to the place where they belong.
Now this is just how I do it in Rhino and your CAD program may vary. There are lots of ways get to the desired outcome. I like to work with solids and use the Boolean Difference command to cut away the parts from the stringers that I don't need. I just need to subtract the steps and risers from the stringers and I am done.
Now I can extract the surfaces of the steps and the stringers and draw out these parts on the material. I use that to have all the stringers cut to length at the store.
Attachments
Step 4: Building My First Staircase
Our first stair (my brother was with me from the first stair on) was all drawn to the lumber by measuring distances and angles from the computer. We would measure points perpendicular from the edge of the lumber and check by measuring the angle.
That worked perfectly fine and everything is accurate up to +-1mm up till today.
We are a little proud of that considering every cut on the beams was done by hand with the Riobo saw.
We still use the computer on site but now we can just leave it in a dust free place and snap the pictures we need with our smartphone.
The stringers are mounted to the wall with threaded rod glues into dowels (construction anchors). I routed a shallow hole first to sink the nuts planning to hide them later (never did it...had enough work with finishing the rest of the house). The outer top beam is just routed and sitting on a rod.
You can see both mounting details in the last two pictures.
The steps are bedded on cork which I felt necessary to eliminate noise. Turns out it isn't necessary at all so we just screwed all following steps tight to the stringers. When we removed the old staircases at my brothers house there was 50 year old newspaper under the flooring which was used back then to mitigate noise. I don't know if it really works but hiding newspapers in any building project to be found in some decades is always fun.
If there is noise from the risers you can stop them from creaking by pressing in clear silicone which also helps against cold air coming through small gaps from the basement.
All steps are fastened to the stringers with self cutting, V2A torx patio screws. They also draw the steps to the stringer. I used four per step, sunk them some millimeters and hide them with wax (picture in the next step). You can also hide them with wooden dowels before painting if you like a more refined finish.
My father in law helped me spray paint the steps and the risers.
All subsequent staircases where painted with rollers and water based paint for stairs.
Step 5: Stairs to the Basement
As you can see in the drawing this staircase was just shortened approximately 95cm and built on top of the concrete stair.
The red line is the concrete stair, the blue hatched surface the beam. The beam was fastened to the wall with threaded rods glued into the concrete walls.
I still have the option to do a hatch in the top landing for some kind of root cellar.
In the picture with the screws you can also see the wax cap hiding the head.
Step 6: #3
For the last two stairs we had the luxury of using 1:1 CNC cut cardboard patterns for the treads as well as for the stringers (one pattern for the outside and one for the inside of each stringer). We would just trace the patterns on the wood and check by comparing some points to the computer drawing.
The cardboard patterns also allow for easier set up on site. We just nail them to the wall, level them in with the laser levels and draw lines to indicate where to put the final stringers. They cardboard treads are then used for final fitting and modified if needed before cutting the steps using them as templates.
For the steps the new drawing method was used.
Step 7: #4
The upper staircase is always a little more challenging to install since you got a deep void under you. We opted to be save and installed temporary platform under part of the stair so that we could reach the back corner easily.
The triangles are glued and screwed to the stringers. We use high force screws to glue the triangles. They can be removed and reused after the glue is set.
Step 8: Conclusion
A stair is a very special thing to build. Walking it every day multiple times I am so glad it did turn out so good. If you plan to try it too please take your time since you would regret a mistake every day you walk up and down.
I guess it is still worth a try anyways since you don't sink that much money and can always buy one if it turns out a dud.
If you got any questions or need assistance drawing your stair please just ask. I really enjoy this work and would gladly help (for free of course). If you want to build your stair in Vienna I might even drop by to help.
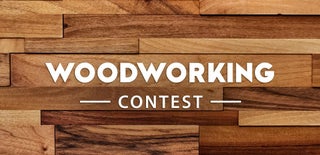
Participated in the
Woodworking Contest