Introduction: Zbrush Tips and Techniques for 3D Printing
This instructable is designed to give users new to 3d printing some qucik tips and techniques to create better designs suitable for Desktop FDM 3D printing in the software ZBrush from Pixologic. This instructable assumes the reader has some knowledge in navigating the ZBrush interface.
Step 1: Setting System Units Reference
- Download and import the 1inchbox.obj. The models is as the name suggests, a 1 inch x 1 inch x 1 inch box model. Once imported into the scene turn on the Edit control. Under geometry in the toolbar tab change the box's origins to 0 on each axis. Under scale change each axis to 1.
- Turn on Floor grid. Make sure Perspective is off.
- In menu bar, click on Draw. Change grid size to 0.5 and tiles to 2. This will generate a floor grid that is 1 inch big (or 25.4 mm) with squares that are 1/4 inch per square or 6.35 mm per square. You can now adjust the grid size and tiles according to your needs.
Attachments
Step 2: Transpose As Measuring Tool
The transpose tool can be used for more than moving,scaling, or rotating your design. It can also display ticks on its line so that it can be used for measurements.
- Switch to TransPose by clicking on Move, Scale or Rotate while in Edit mode.
- With your 1 inch box model in scene move the ends of the TransPose line to define the beginning and end of the box. This is what will be the unit length.
- Open the Preferences > TransPose Units sub-palette.
- Click on set units and enter the unit name of your choice. For example, MM for Millimeters.
- Change the Calibration slider value to suit your chosen Units. For example, 25.4 input into the Calibration field will define 25.4 mm (1 inch) as the set length
- Now drag an end of the action line to increase or decrease its length. Notice that new tick marks will appear or disappear. Also, the total length will be displayed in the status bar.
Step 3: Designing for Assembly
When designing models that need to be assembled, it’s important to provide enough distance between the parts that will be attached together. A perfect fit shown in the software does not mean a perfect fit after 3d printing. Why? Because 3d design software ignores the friction and material inaccuracies present in the real world. Therefore for snap fits, always leave at least 0.25-0.3 mm between the different parts.
For looser fittings such as hinges or chainmail, the spacing between your surfaces is crucial. Spacing will determine the flexibility/bendability of your design. A minimum space of 0.4 mm is recommended between surfaces.
Setting up your transpose tool for measuring can help give you accurate spacing between your design's parts.
Step 4: Exaggerate the Detail
When sculpting details onto your model, it is recommended to slightly exaggerate details for 3d printing. This means making your surface details with slightly deeper cuts and more pronounced surface texture. It also means making slender parts slightly thicker.
Why?
Printing resolution limitations. Most desktops FDM printers available today come with a 0.3 or 0.4 mm nozzle that can print at resolutions of 0.1mm (highest) to 0.3 mm(lowest). As a result you can lose shallow engraved or embossed surface details. For standard FDM printer it is recommend to apply details with a minimal depth or height of 1 mm for best results.
3d printers printing parts one layer at a time. If a feature is too thin, there’s a risk of the printed part deforming or detaching during print due to insufficient material contact to the rest of the design. Recommend minimal wall thickness for generic FDM materials such as ABS or PLA is 1 mm to 1.5mm depending on the brand and type. Note parts under 3 mm in thickness are prone to breakage during and after printer, especially when removing print supports.
*Bonus Tip: Utilize the Clay Polish tool located in the Geometry subpalette. If your mesh is under 1000000 polygons in Zbrush (even after using Decimation plugin to optimize mesh) you can use the Clay Polish tool to estimate potentially how much detail you will lose during 3d printing on a desktop FDM printer with a standard 0.4 mm nozzle.
Step 5: DynaMesh & Zmesher
High poly models are nice, but a design with a resolution that is too high can bog down a computer processing power and the exported files can be too large in size for a 3d printer slicer software to handle. Utilizing ZBrush's Dynamesh & Zmesher tools can allow you to create elaborate sculpts while keeping your computer from bogging down in memory and speed.
DynaMesh allows you to maintain the uniform resolution and polygon distribution of your mesh. ZRemesher will recreate a new polygonal structure for your model, with a controlled flow of polygons and a global polycount value. In just a few seconds you can convert a 200,000 polygon DynaMesh to a 10,000 poly retopologized model with a natural flow of polygons. From there you can project all the fine details from your original sculpture.
Step 6: The "Y" or Rule of 45°
The “self-supporting” or “safe” zone does not require any support to print the model. For most models, this area ranges from 135° to 45°. When designing an object you would like to print in a FDM material such as ABS or PLA, keep this safe zone in mind if you are concerned your model will require support to be constructed.
Transpose tool can help you measure angles to determine if you would need supports when printing the design.
Step 7: Set Polygroups
When working with a solid mesh that may need to be split apart later on into subtools (such as a character), Polygroups are one way to organize your mesh. Polygroups are selection areas set on your mesh. These areas can help with quick masking (CTRL+Shift+Click on PolyGroup) when designing while keeping a contiguous surface. For characters, Polygroups can make splitting a mesh to subtools later on easier especially after posing.
Step 8: Split Mesh to Reduce Print Supports
Printing supports require additional printing material and therefore incurs additional costs and print time. The supports also need removal, creating more work for the 3D printing service provider which can also increase the total cost of the print job.
One of the limitations of using printing supports in FDM printing is that post-processing is always required. Supports can cause marks or damage to the surface where it is in contact with. Layers printed upon supports will be less perfect as the supports will be slightly less stationary than the solid layers.
Supports can also be difficult to remove from small intricate features without breaking the model.
Step 9: Use Live Boolean to Help Make a Watertight Mesh.
A Design might look great for 3D printing from the outside but intersecting parts and walls on a design can make it unprintable and confuse printers about what you want to print exactly. But luckily Zbrush has a Boolean feature to help optimize your design by removing unneeded geometry inside the mesh.
Boolean operations are mostly composed of multiple models flagged for addition or subtraction mode, stacked on top of each other in the SubTool list. When the "Make Boolean Mesh" button is clicked, Zbrush will create a new mesh using all visible meshes with the result being a single watertight mesh.
Step 10: Decimation Tool
A file with a resolution that is too high will make your file too big and sometimes impossible for a slicer software to handle. It might also contain an extreme level of detail that the 3D printers simply cannot print. It is recommended to stay below a file size of 100MB when uploading your model to a website or importing into a slicer software.
To help keep file size under 100MB, you can use the Decimation tool to optimize your design's file size without losing detail.
Step 11: Credits
Nier Automata 2B shown in this Instructable was designed by me and hosted for free download on Myminifactory.com. Nier Automata was developed by PlatinumGames and published by Square Enix. You can see this design and others created by me on my myminifactory profile.
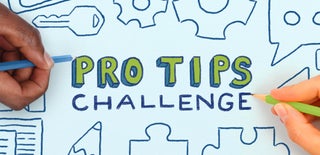
Participated in the
Pro Tips Challenge